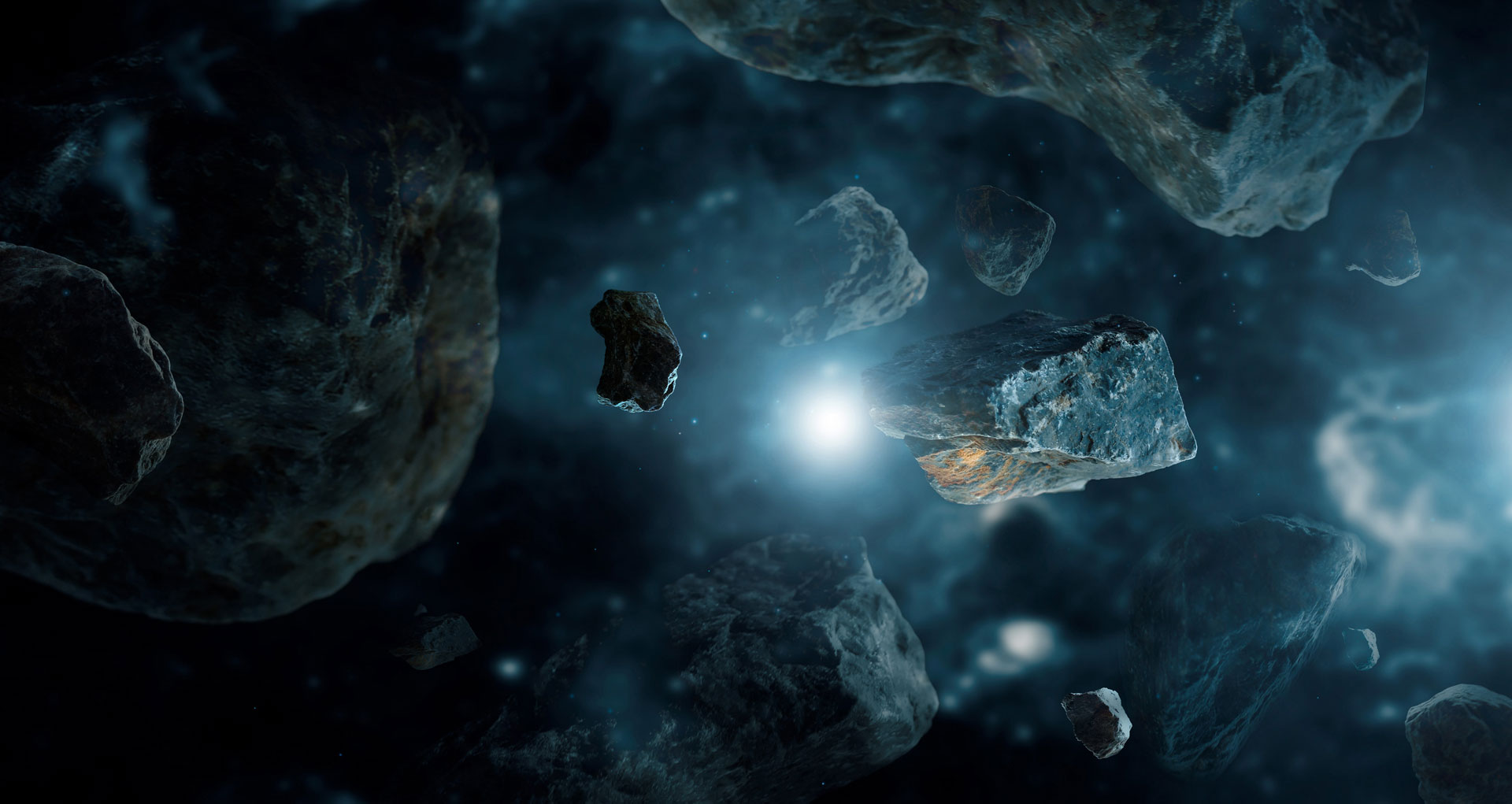
Predicting damage caused by micrometeorites and minimizing the consequences
The commercialization of space exploration increases the need for innovative technologies for space and planetary exploration and satellite missions. To ensure the safety and reliability of space structures, it is important to assess their structural integrity. Harsh space conditions, such as radiation and high temperature fluctuations, increase material degradation and wear. In addition, there is an omnipresent risk of micrometeorite impacts, which can cause severe structural damage.
Challenge in space
With the growing number of satellites in Low Earth Orbit (LEO), the probability of collisions caused by space debris is increasing. The ESA estimates that there are over one million particles larger than 1 cm in orbit, of which only around 30,000 are cataloged and monitored e.g. by the Space Surveillance Network. Collisions with these particles and impacts from micrometeorites can cause structural damage that impairs the functionality of structural elements and electronic subsystems and, in the worst case, terminate the entire mission.
Goal: In-orbit evaluation
Conventional non-destructive testing methods carried out on Earth are only applicable to a limited extent in space. Therefore, an in-orbit evaluation of the condition of mission-critical structures and systems is necessary to monitor both the degradation process and the occurrence of singular events such as impact damage.
Structural monitoring systems have proven their technological maturity as a non-destructive testing method in various branches of industry and terrestrial applications. The next logical step is the transformation and qualification of established monitoring approaches and systems for use in space, which is being implemented as part of the SeRANIS project through the "Structural Event Monitoring" flight experiment for vibration and ultrasound-based structural monitoring.
By integrating a prototype on the SeRANIS research satellite Athene-1, vibration data from low-Earth orbit will be provided to improve Space Situational Awareness (SSA) and support further research efforts.
Test campaign
The reliable detection of collisions and impacts of small particles is affected by structural background noise emitted by other subsystems on the satellite platform. In order to maximize the event detection rate of the monitoring system, algorithmic detectors must be trained for the expected vibration pattern. To this end, experiments were carried out at the Fraunhofer Institute for High-Speed Dynamics, Ernst-Mach-Institut (EMI) in Freiburg to investigate Hypervelocity Impacts (HVI). The impact campaign was carried out using a two-stage light-gas gun (SLGG), which accelerates microparticles to up to 7 km/s.
The particles were placed in a sabot, which was accelerated to the required launch velocity as a result of black powder charge ignition and the resulting gas compression. Part of the particle cloud, consisting of spherical glass beads with a diameter of 100-200 μm, hit a target sample at approx. 2.5 km/s (see Figures 1 and 2). This consisted of a photovoltaic element, which was provided by Airbus Defense and Space GmbH and was aligned perpendicular to the firing axis in the target chamber.
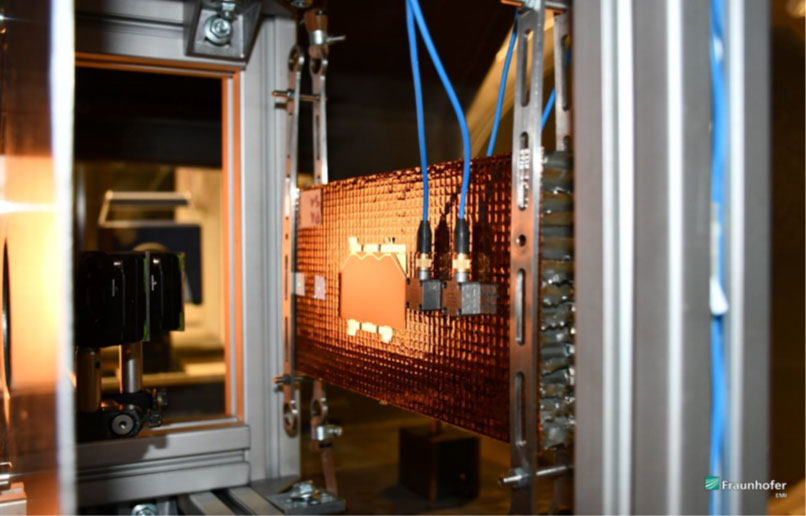
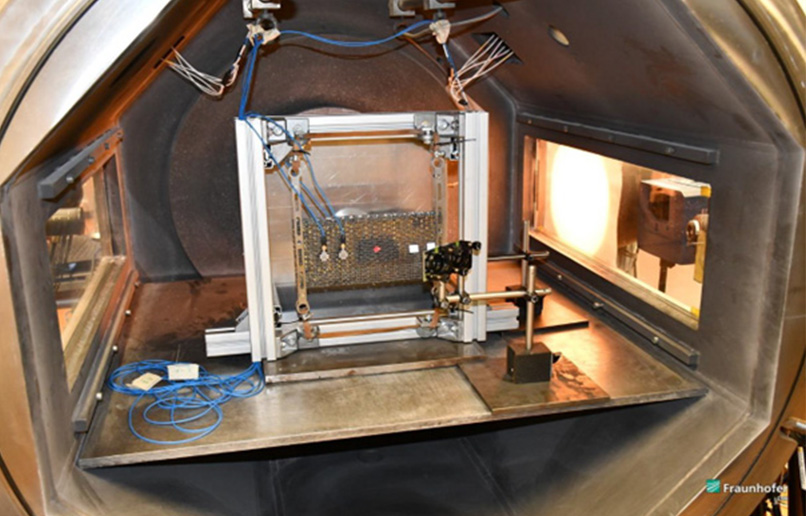
To accelerate the tiny particles to hypervelocity, the target chamber was evacuated to 80 mbar. When the particle-loaded sabot entered the target chamber, the friction of residual atmosphere caused the sabot to separate, so that parts of the particle cloud were isolated and hit the photovoltaic element in a targeted manner.
Piezoceramic acceleration and ultrasonic sensors, which will later be used in space, were applied to the target sample.
Overcoming the performance limits of ultrasonic sensors: The use of Polytec laser vibrometers and signal processors
The mechanical design of acceleration and ultrasonic sensors limits their detectable frequency spectrum. Additional factors such as sensor inertia and physical connection to the carrier structure inevitably influence the measurement quality, as high-frequency signals can sometimes not be fully captured. In order to not impair the information content of the measurement results, four laser vibrometers from Polytec GmbH were used. These measured the impact signal simultaneously at four measuring points, distributed over the front and back of the target sample. For the impact test, the vibrometer’s laser beams were aligned to defined measuring points using deflection mirrors.
Laser Doppler vibrometers use the frequency shift of light, which is proportional to the surface speed of the measuring surface. There are no fundamental limitations to the measuring frequency in this method, which is why even high-frequency movements of several megahertz can be precisely captured. The laser vibrometers therefore make it possible to measure transient signals far beyond the measuring range of conventional sensors.
For the impact campaign, it is also advantageous that the measurement on the test specimen surface is carried out contactless using a laser: On the one hand, there is no mass influence on the test specimen, which ensures high consistency of the measurement data, and on the other hand, measurements can be taken conveniently through the observation windows of the target chamber.
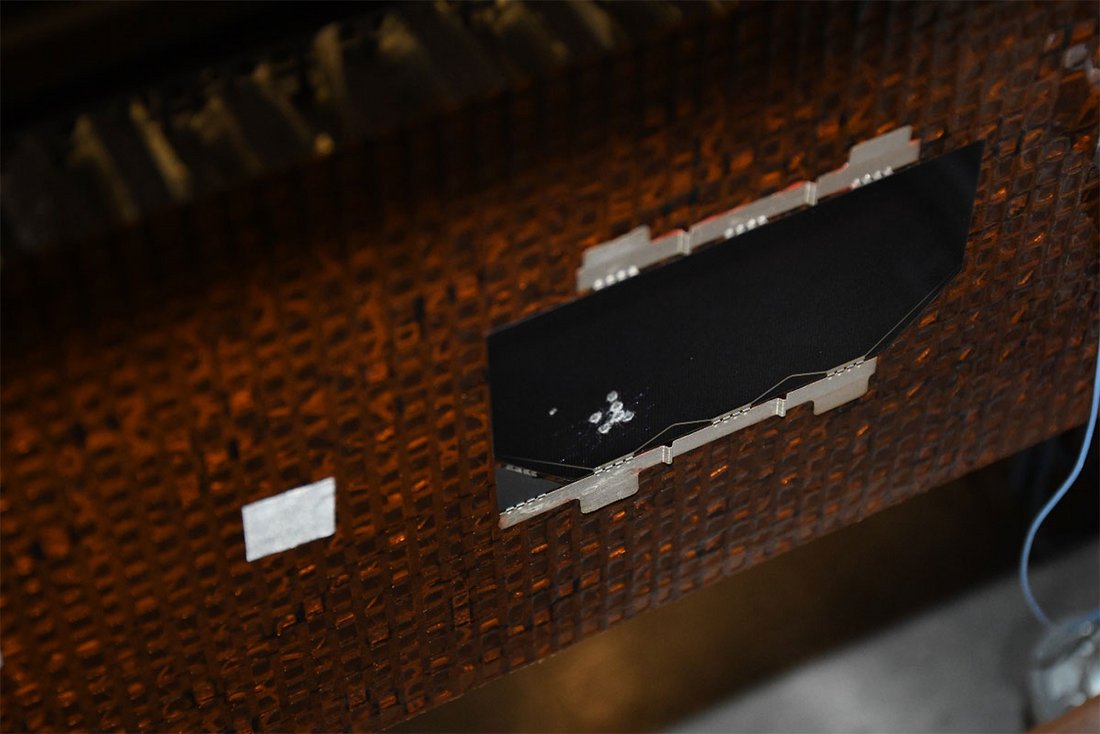
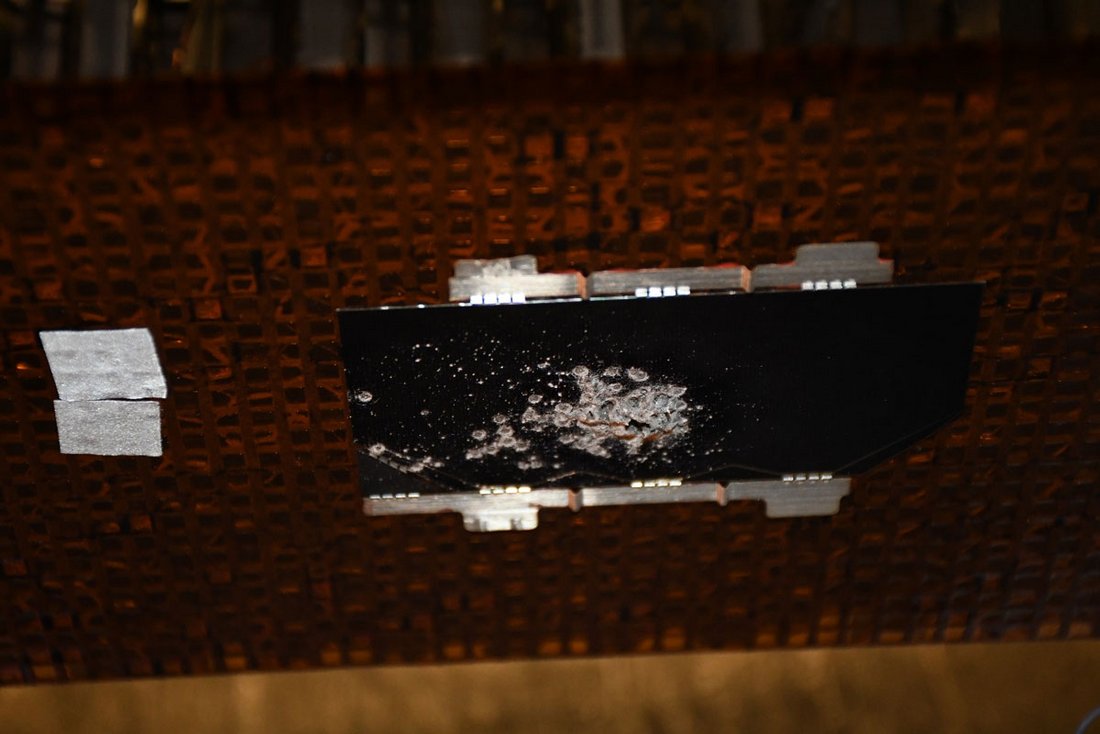
The focus of the experiments is the detection and analysis of so-called acoustic emissions, which propagate through the structure as elastic ultrasonic waves. These emissions, known as Lamb waves, serve as a reliable indicator for detecting high-speed impacts caused by microparticles. Existing structural damage and degradation effects also manifest themselves through similar phenomena, so that structure-borne sound emissions allow conclusions about the health condition of a component.
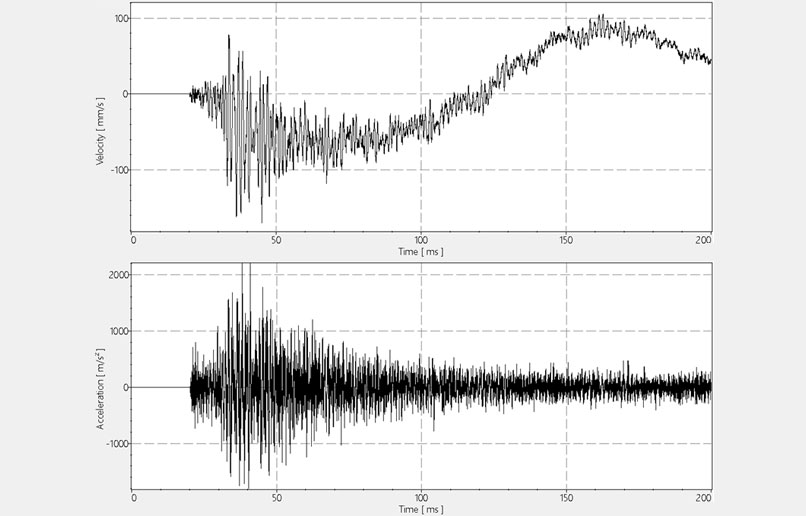
One challenge is that the signal characteristics of the impacts and the required measurement parameters are not known at the beginning of the tests and must therefore be determined and adapted in-between each test. Powerful and flexible analysis software provided by the Polytec signal processor is used for this purpose. By combining software functions such as frequency transformation, filtering and numerical differentiation/integration, the impact signals can be analyzed and compared with the recorded sensor signals in order to successfully optimize the measurement settings.
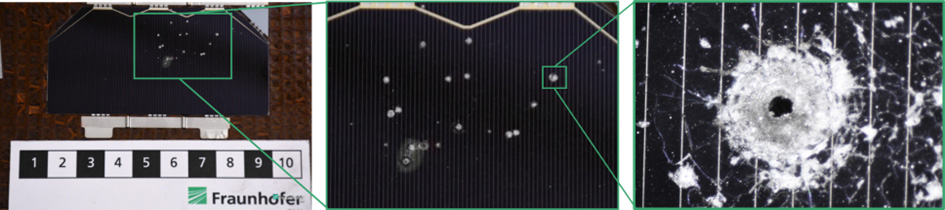
Outlook
The impact induced wave pulse is accompanied by a series of complex physical processes: Electromagnetic emissions in the visible, infrared and microwave spectrum radiate from the impact site, plasma and secondary particle clouds emerge from the crater (see video sequence) and damage ranging from microcracks to complete cell perforation occurs.
In order to reliably detect the occurrence of such impact events, the induced vibration and structure-borne sound patterns of these phenomena must be known. The investigations carried out contribute significantly to the development of innovative detection algorithms, which form the core of the SeRANIS flight experiment "Structural Event Monitoring". In the next step, the findings from the bombardment tests will be used to qualify suitable sensor and hardware components.
Finally, detection and classification approaches based on the vibration and ultrasonic signals will be trained in order to evaluate their suitability under real operating conditions. The developed prototype of the experiment will be tested over a mission period of at least two years in LEO.
Images courtesy: Images courtesy of the authors unless otherwise specified. Cover image: PopTika/Shutterstock.com