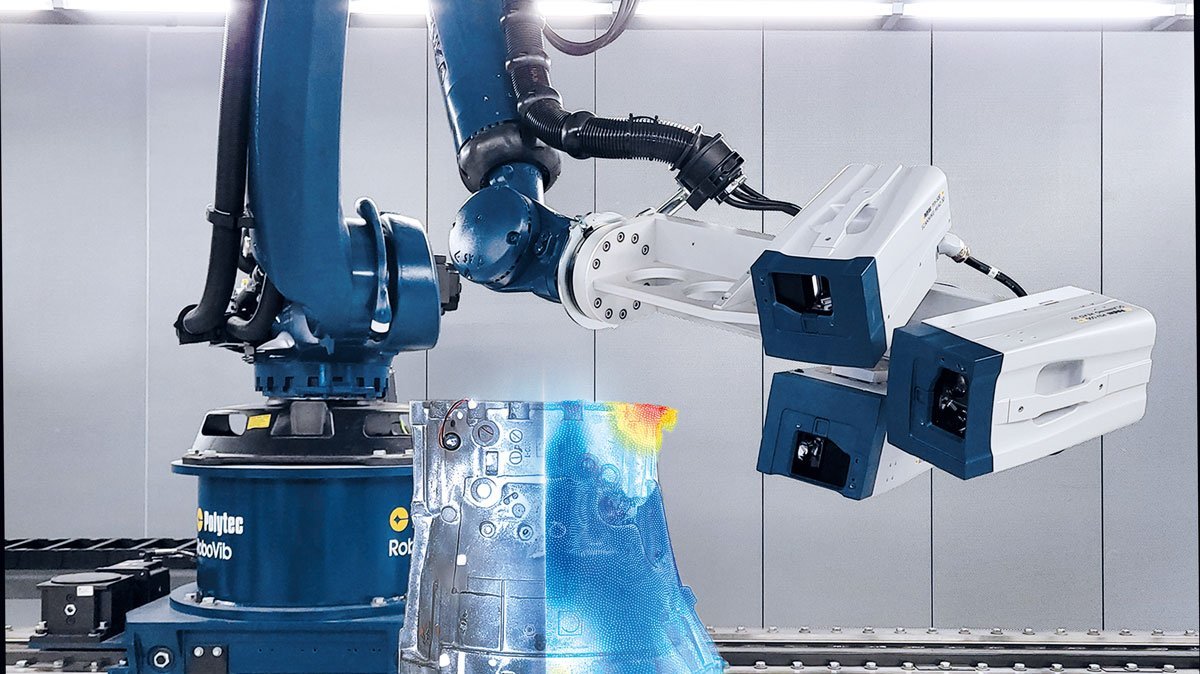
State-of-the-art excitation methods
If you would like to test the vibration behavior of an object that is not vibrating by its own, you have to excite it externally. For modal tests both an electromagnetic shaker and a modal hammer are common broadband excitation tools that has been widely used for many years. For a measurement using a Polytec Scanning Laser Vibrometer, which measures points sequentially, a hammer impact has to be repeated for every scan point. For this reason, automated modal hammers like the SAM, designed by NV-Tech, have become popular in recent years.
Both existing excitation methods have strengths and weaknesses. An electrodynamic shaker leads to faster measurements over many points and repeatable test results. But a shaker with force sensor can have a non-neglectable influence on the structure under test. And, in practice, setting up and aligning the shaker, maintaining alignment, is cumbersome, especially on test setups where the sample is supported by soft rubber strings or soft foam to mimic free-free conditions.
An (automated) hammer on the other side has ideally no impact on the inherent dynamic properties of the part, making it a good choice for relatively lightweight and lightly damped structures. Due to the decay time after each hit the measurements take considerably more time and, for lightweight samples suspended by soft rubber strings, might lead to considerable swaying of the entire sample.
Combining strengths
Recently, a third excitation method has appeared tackling the shortfalls of the above-mentioned methods: Inertial shakers with integrated force transducers from Qsources. These shakers have some interesting features like a self-aligning internal suspension, very low mass and an easy handling and alignment. Being attached to the structure the position is fixed and they avoid the waiting time with automated hammers. On the downside, they only work well above a certain cutoff frequency and load the structure in a similar way as an accelerometer with cable would. For this article, we have tested the Qlws inertial shaker and compared it to a classical shaker and an automated modal hammer.
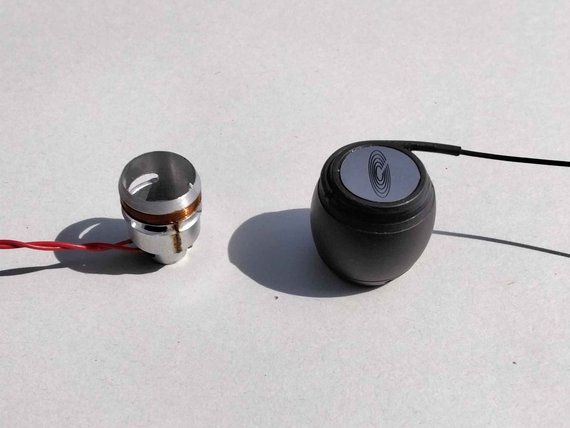
Use of the Qlws light weight inertial shaker
The Qlws itself consists of 2 small parts (+ an amplifier):
- a so-called “force cup” contains the voice coil. It is glued to the object under test.
- the shaker body, containing the inertial mass and a force sensor. It is simply manually pushed over the force cup.
Between the two, a thin layer of grease is used for dynamic decoupling, leading to a dynamically active mass of < 2 g in the range above 200 Hz.
Attaching the Qlws is easy: clean the sample with alcohol, glue the force cup with instant glue, put a thin layer of grease, slide the shaker body over the force cup and connect the cables to the amplifier box and to a data acquisition featuring IEPE power supply.
No stinger alignment is necessary, as the device is self-aligned in any inclination.
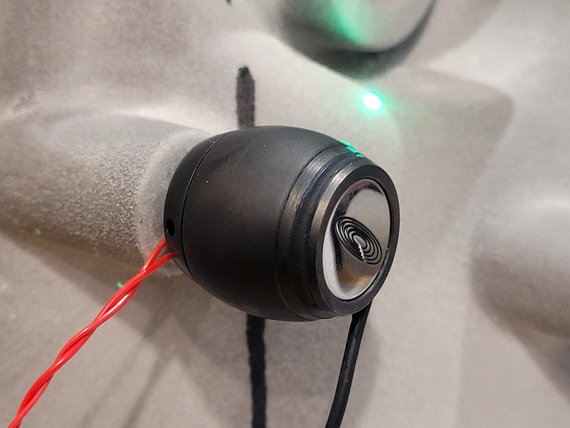
Attaching the Qlws is easy: clean the sample with alcohol, glue the force cup with instant glue, put a thin layer of grease, slide the shaker body over the force cup and connect the cables to the amplifier box and to a data acquisition featuring IEPE power supply.
No stinger alignment is necessary, as the device is self-aligned in any inclination.
Comparison test
Comparison has been done on a 1,5 mm thick aluminum plate, suspended by elastic straps. This plate is excited by a classical modal shaker, an automated hammer “SAM 1” and the Qsources Qlws. To measure the vibration behavior, a Polytec non-contact PSV Laser Scanning Vibrometer is used which has no influence on the test object.
The following images show the electrodynamic shaker (LDS shaker), the automatic hammer (NV-Tech SAM), and the inertial shaker (Qsources Qlws):
The LDS shaker is quickly seen having too much influence on the light test object: resonance frequencies are shifted, and the force spectrum has some dramatic drops, leading to bad signal to noise ratio at the transfer function between response and excitation. The conventional modal shaker is therefore not suitable for this setup and should be used for heavier samples only where it has its strengths.
The NV-Tech SAM automated hammer is the reference in terms of mass loading of the test-object since nothing is permanently attached to the structure. It is therefore the excitation source of choice for objects with very small damping. Its frequency range is also extending to low values. For the very light suspended test sample, it has nevertheless a drawback: It leads to swaying of the suspended sample. This, together with the use of a scanning vibrometer leads to unnecessary noise in the measurements. This effect can to some extent be mitigated by the use of the latest Polytec QTec® technology in the vibrometer, but the signal to noise ratio will still be somewhat reduced by the macroscopic swaying. The swaying also increases the test time, as the user has to wait before the next automated hit can be applied. If swaying can be avoided (e.g., if sample support on soft foam is acceptable), the hammer is still a very good choice for objects with little damping and for a wide range of frequencies.
The Qsources Qlws has only very limited influence on the natural behavior of the sample due to its small dynamic mass. If placed correctly, the influence of coupling the shaker to the test-object eigenfrequencies is very small, comparable to the effect of suspending the test-object, for frequencies below 2 kHz, which covers the first 15 - 20 resonances. No waiting time between excitation sequences is required, therefore speeding up the test considerably. The only drawback that appeared during the test is the low frequency limitation below 250 Hz. It does not mean that the shaker is not working for lower frequencies , but at lower frequencies it has slightly more influence on the natural behavior of the sample due to the higher effective dynamic mass.
Figure 3 shows typical results of SAM hammer (left) and Qlws (right) for this setup.
The main results are:
- Resonance frequencies and corresponding deflection shapes are virtually identical between 200 and 2,000 Hz.
- Below 200 Hz, the inertial shaker only has some minor influence, also above 2 kHz.
- The increase in noise due to the swaying, caused by the hammer impact, can be clearly seen in the depicted deflection shape.
- The scan time for the measurement with the automated hammer was about 2.5 h as compared to 0.5 h using the Qlws.
- And, even a small conventional electrodynamic shaker with stinger and force sensor is not suitable for this type of samples.
Resume
To resume, the Qsources Qlws shaker is a very interesting alternative to an automated modal hammer, as it produces no swaying of the test object which lowers the signal to noise ratio for single channel Vibrometers without the Polytec QTec® technology.
Since this additional noise can be compensated using multi-channel QTec® Scanning Vibrometers both technologies, the inertial shaker and the automated hammer produce test data on the same level. Limitations can be the lower frequency limit of the Qlws and the added mass for extremely light weight or extremely low damped samples.
The setup of the Qlws is very convenient, comparably simple as an automated hammer, has excellent repeatability, and is a lot faster than the hammer and easier than a classical shaker with stinger. As with the Qlws there is no waiting time between hits, the measurement time can be considerably shorter for suspended samples.
Images courtesy: Images courtesy of the authors unless otherwise specified.