
In order to keep your natural teeth as long as possible and to prevent caries and periodontal infections, home-care methods like brushing your teeth and flossing are essential. Unfortunately, these alone are not sufficient. Biofilm arises even if these home care treatments are performed correctly and can lead to calculus formation and to serious diseases.
Regular visits to a dentist are necessary for diagnosing the formation of biofilm or calculus and applying preventive techniques to neutralize their growth. A specific protocol developed by E.M.S. Electro Medical Systems S.A. from Switzerland, called Guided Biofilm Therapy (GBT®), ensures the most minimal invasive and comfortable treatment. This protocol includes disclosing and preventive steps, biofilm removal with Airflow® technology (air polishing technology), calculus removal with Piezon® PS (ultrasonic scaler) and at the end controls and recall steps.
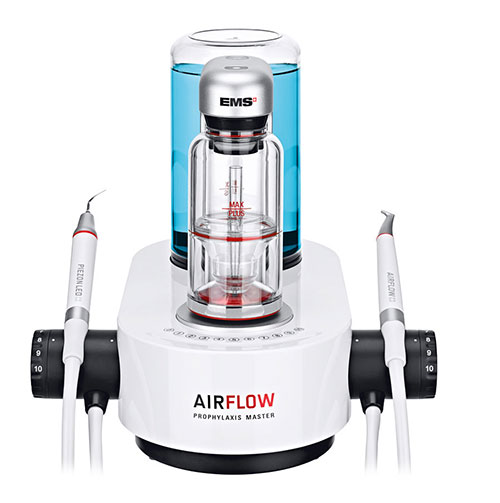
In order to reach the most efficient treatment with a noninvasive and comfortable approach, we need to master the PS instrument motion. Laser Doppler vibrometry plays an important role and can be used in the design and manufacturing of this high-end dental instrument.
In this Guided Biofilm Therapy (GBT®) protocol, Piezon® technology with PS instrument is used due to the linearity of its motion, its efficiency, and its minimal invasiveness on teeth and soft tissue compared to other technologies like manual, air scaling or magnetostricitve devices. The Piezon® system removes calculus through the controlled vibration of the instrument excited by a piezo trans-ducer inside the handpiece. This piezo transducer is driven by the electronic module, included in the unit, which ensures a constant vibration of the instrument.
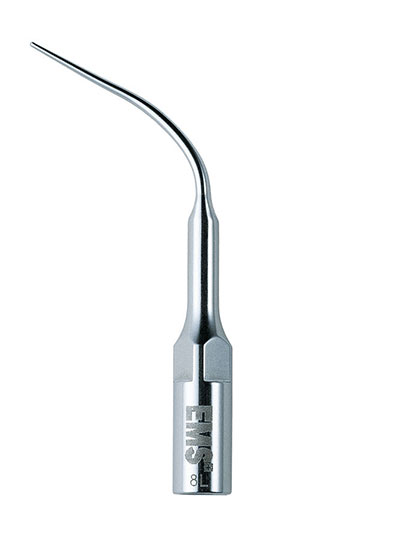
The E.M.S. PS instrument maintains gentle and efficient motion from supragingival to subgingival treatments, thanks to its geometry and the shape of its thin end. The linearity of the motion is ensured only when the entire system is perfectly balanced between the instrument shape, the ultrasonic transducer design and the electronic driving module. It’s not the case for some competitors which supply only tips without control on the entire system. In fact, small deviations in geometry, materials, and treatments can degrade performance. In such cases, proper vibrational behavior of the tip may not be ensured, possibly resulting in dangerous motions and patient discomfort.
To ensure proper vibrational motion of its instruments, E.M.S. uses the most advanced technology throughout the whole development and characterization process. Indeed, in the development phase, scanning laser Doppler vibrometers are used to calibrate and validate Finite Elements Models (FEM). During final validation, they are used to control the small acceptable deviations on the transducers and in the instrument fabrication process. With that, the acceptable wear for each instrument is also determined using this advanced measurement technology.
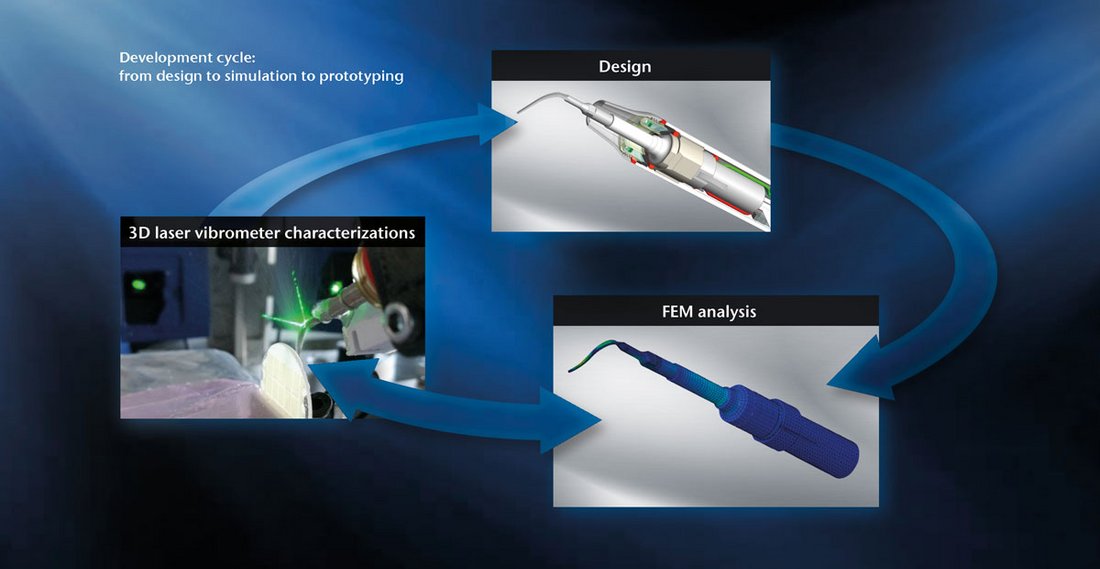
The best technology supporting the best treatment.
The characterization of the ultrasonic instrument requires contactless analysis methods able to accurately measure small displacements (less than 200 µm peak-to-peak) at a high frequency and in real time, to link the electrical signal sent by the electronic module to the mechanical motion of the instrument. The PSV-3D Xtra system offers the ultimate characterization technique in this field, as it is able to measure the complete 3D motion of the tip by scanning its surface and taking the electronic signal sent to the piezo transducer as its phase reference. The scanning vibrometer makes it possible to confirm the linearity of the instrument’s motion under real conditions, with contacts on a teeth surface and water spray. In addition, the Polytec‘s Xtra vibrometer technology broadens the speed range up to 30 m/s, which corresponds, at a scaler working frequency (29 KHz), to displacements of 275 µm peak-to-peak.
Results
The measurement of PS instrument was performed in air, with no mechanical load. The end part of the instrument is mapped with approximately 135 points to precisely define the X; Y; Z motion of the instrument. The result is shown Figure 4
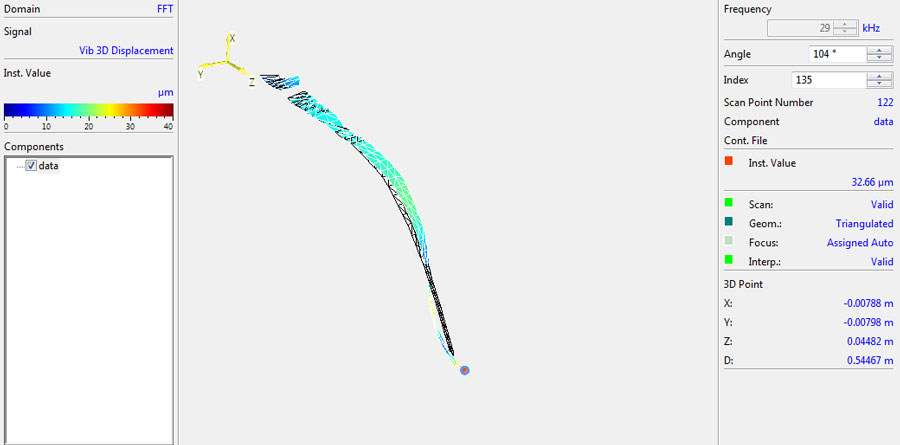
With these results, we are able to verify our FE model (mode of deformation, frequency, linearity of the ultrasonic motion) and calibrate it (losses) to match with the real amplitude of the ultrasonic motion, see Figure 5.
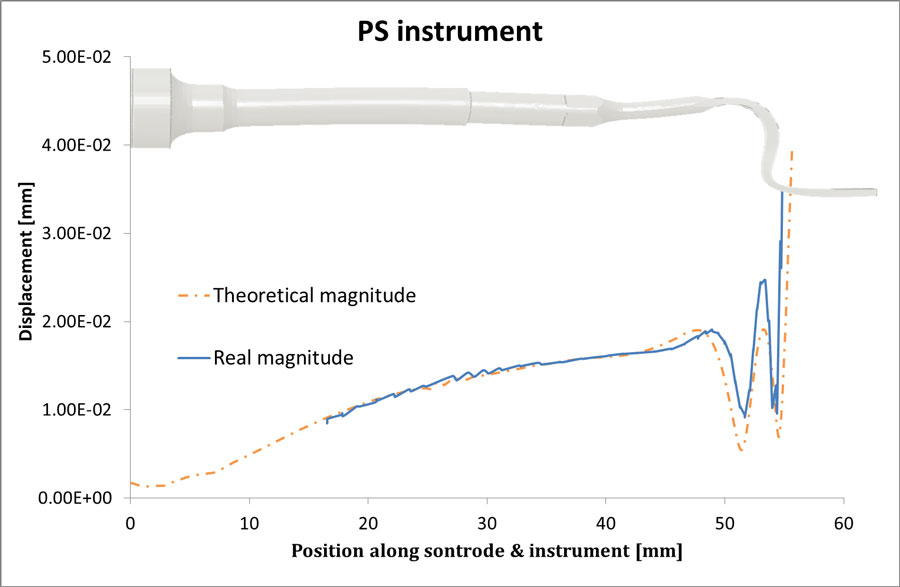
We can also compare the mechanical measurements with the electrical signal sent by our electronic driver to verify the performance of our control on the output vibration regulation. Furthermore, the laser vibrometer is used to measure the instrument motion under real conditions (with load induce by and contact on teeth and calculus) which are difficult to model in simulation. Even under challenging operating conditions we were able to accurately capture the amplitude in-situ and verify the linearity of the motion.
Conclusion
The Polytec PSV-3D Xtra Scanning Vibrometer is able to capture, with an incomparable level of accuracy, the high-speed motion of the ultrasonic PS instrument. Thanks to this measurement technology, we have validated and calibrated our theoretical models, controlled the performances of PS instrument and we characterized how the system reacts during operation. Thanks to the synergy design-simulation-prototyping, laser vibrometer helps us to develop new concepts, to continuously improve our products, and to optimize all key factors in order to ensuring the efficient and non-invasiveness of a prophylaxis treatment: The best technology supporting the best treatment.
Images courtesy: Images courtesy of the authors unless otherwise specified. Cover image: ©Igor Korchak/iStock.com