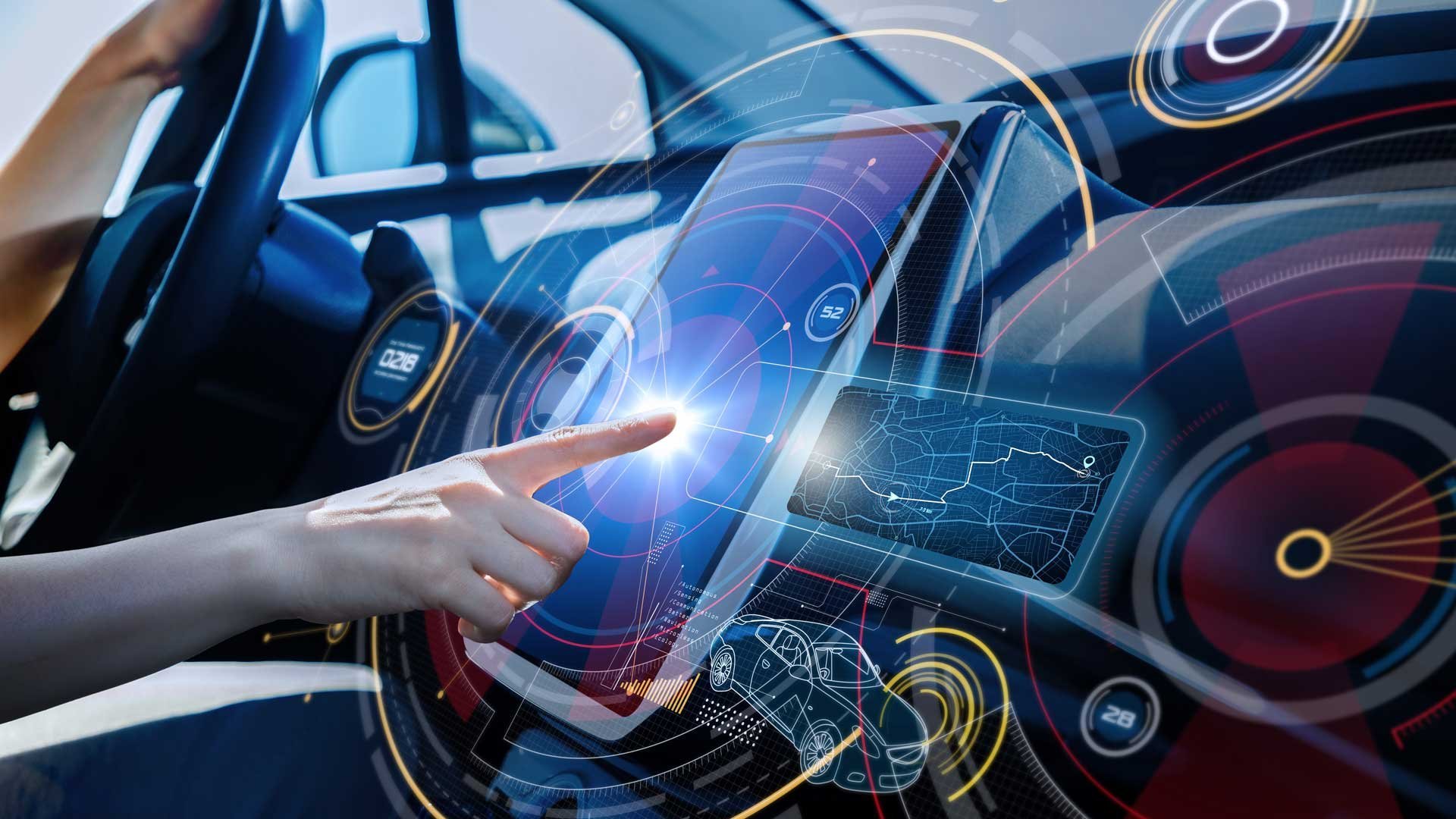
The increase of touchscreen interfaces in automotive applications leads to a visual overload of information that has serious safety implications. Haptic feedback technology is seen as an opportunity to improve the user experience and reduce the cognitive load of interacting with touchscreens.
hap2U’s haptic technology, recently taken over by Vibra Nova, is based on ultrasonic wave propagation generated by piezoelectric actuators. The vibration created by those actuators reduces the friction coefficient between the finger of the user and the glass surface of the haptic display. This phenomenon is known as active lubrication because the fingertip, under the effect of the ultrasonic vibration, undergoes a reduction of its contact area1,2 and therefore of its coefficient of friction. As the human body is very sensitive to friction changes, compelling tactile sensations can be achieved through the control of the contact with the plate surface by activating and deactivating the ultrasonic vibration, creating the friction modulation.
In order to optimize the excitation of the system and to simplify the command, a global resonance of the display is used as it is represented in Figure 1.
Laser Doppler vibrometry is used in this context to evaluate the performance of the mechanical system since it allows the measurement of the amplitude of vibration at the surface of the plate. For automotive applications, the propagation of ultrasonic waves needs to be characterized in the full temperature range of -40 to 85°C, in which the display is required to work consistently.
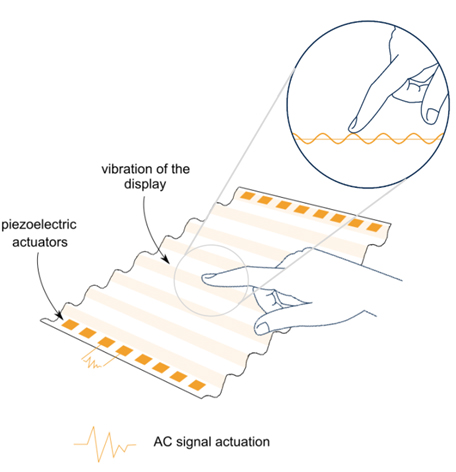
Material characterization
The acoustic characteristics of the system for the propagation of ultrasound waves is very important for a uniform and constant haptic sensation independent of temperature. Today's displays are multi-layer mechanical systems. In these layers, we find many plastic and adhesive materials that change their mechanical behavior with temperature.
Moreover, as the frequency range in which hap2U/Vibra Nova works is ultrasound, it is unusual to find the properties of such materials in this frequency range in literature. Therefore, hap2U/Vibra Nova has developed the know-how to characterize the systems at ultrasound frequencies and at different temperatures.
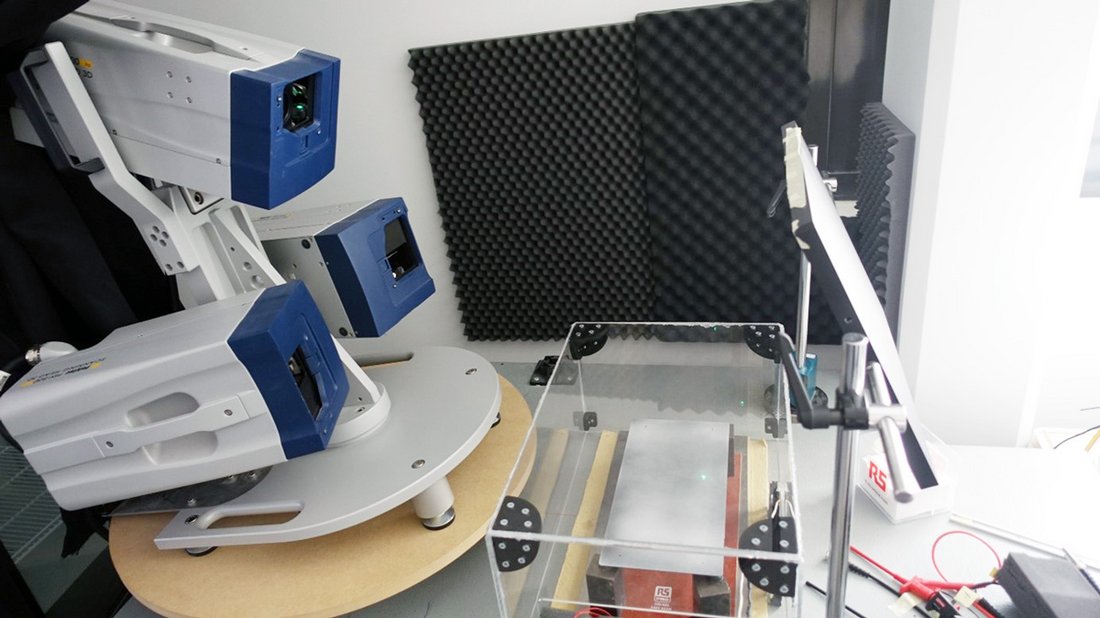
To do this, the system is exposed to different temperatures inside a climatic chamber. Figure 2 shows a simple example, only used for measurements at high temperature. Tests in commercial climatic chambers at both high and low temperatures have also been performed. A Polytec 3D Scanning Vibrometer is used to measure the vibrations generated on the entire surface of the display. The Polytec Laser allows the measurement of very small vibrations in the subnanometer range and this measurement can even be performed through a glass or plexiglass wall (as in Figure 2).
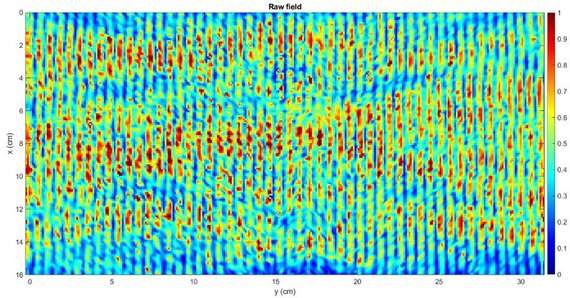
Ultrasonic vibration is generated by activation of piezoelectric elements which create a flexural wave in the display. The response of the system to this excitation is measured to obtain vibrational maps as shown in Figure 3.
The vibrational map of Figure 3 corresponds to a display with good acoustic properties, where haptic technology can be implemented in optimal conditions. To define if the system behaviour is suitable for wave propagation, the acoustic properties of the display are estimated at different temperatures.
One of the main parameters to be considered is the damping of the display. The damping is described by the attenuation coefficient. To estimate this attenuation coefficient, an impulse is generated by a piezoelectric element in the surface of the display, and the achieved displacement is measured with the laser vibrometer throughout the surface of the sample.
The attenuation coefficient describes the reduction of the vibrational amplitude as a function of the distance. The higher its value, the higher the losses of vibration amplitude with the distance to the source.
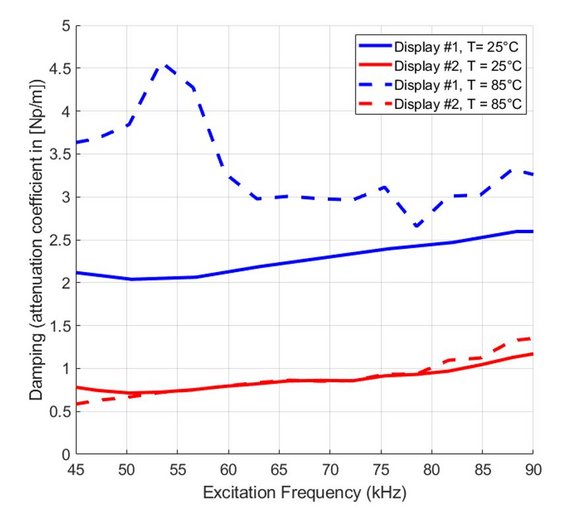
Figure 4 shows an example of two different types of displays characterized at room temperature and 85°C. Display n° 1 (blue curves) shows a higher damping than display n°2 (red curves) already at room temperature and an increase to even higher values at higher temperatures (see dashed blue curve).
Furthermore, the damping depends on the excitation frequency. Maximum damping was measured between 50 - 60 kHz at 85°C. On the other hand, display n°2 shows a lower damping at room temperature and its value is constant with temperature and varies only slightly with excitation frequency.
Given the characteristics of the two systems, display n°2 presents an optimal performance for haptic compatibility in an automotive application.
Scanning laser vibrometry presents an efficient method for the characterization of the acoustic and especially damping parameters of haptic displays over temperature and frequency. This is crucial for the development of displays that show excellent performance over the entire large temperature range as demanded by automotive specifications.
References
1. Wiertlewski, M., Fenton Friesen, R. & Colgate, J. E. Partial squeeze film levitation modulates fingertip friction. Proc. Natl. Acad. Sci. U. S. A. 113, 9210–9215 (2016).
2. Vezzoli, E. et al. Friction Reduction Through Ultrasonic Vibration : Part 1 : Modelling Intermittent Contact. 1412, 1–13 (2017).
Images courtesy: Images courtesy of the authors unless otherwise specified. Cover image: metamorworks/shutterstock.com & Vector Tradition/shutterstock.com