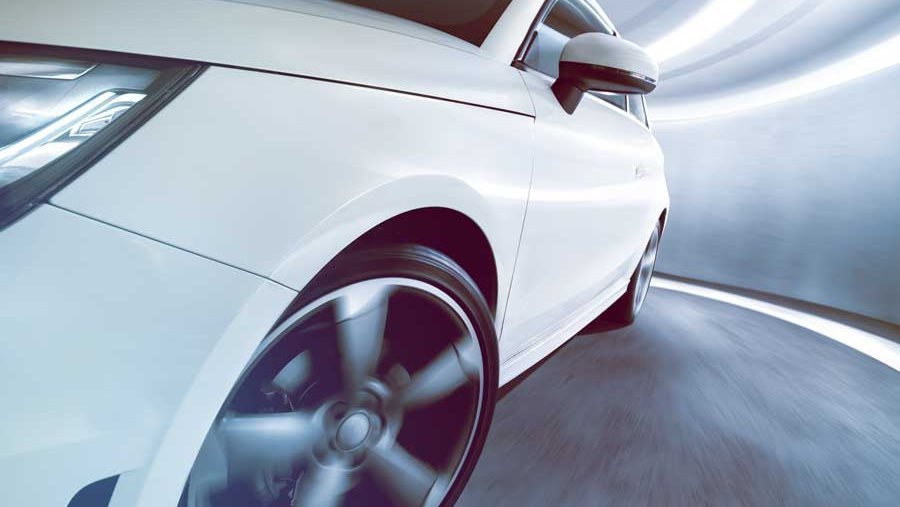
Dynamic 3D operational deflection shapes captured with an Xtra Scanning Vibrometer help reveal the source of rolling tire noise. For a wide range of driving conditions, rolling tires stimulate a significant amount of passenger car noise (NVH) inside and outside of the passenger cabin.
Rolling tire noise must be addressed by engineers for three important reasons:
- Road noise from rotating tires reduces the driving experience and disturbs neighborhoods along the roadway.
- New regulations limiting tire noise are expected in many countries concerned with urban area noise.
- With no internal combustion engine noise, the exceptional quiet of electric cars can be ruined by tire-generated noise.
Consequently, to limit the amount of tire noise, a better understanding of the dynamic mechanism producing the noise is critical and, for that understanding, the precise measurement of the vibration behavior of the rotating tire surface is mandatory.
Classical measurements that use simple microphones to quantify the noise amplitudes inside and outside of a car provide almost no insight into the precise physical origins of the noise. Even accelerometers placed at critical locations can’t give the spatial and frequency resolution needed for accurate characterization.
Basically, classical NVH measurements and methods are not helpful to solve this problem.
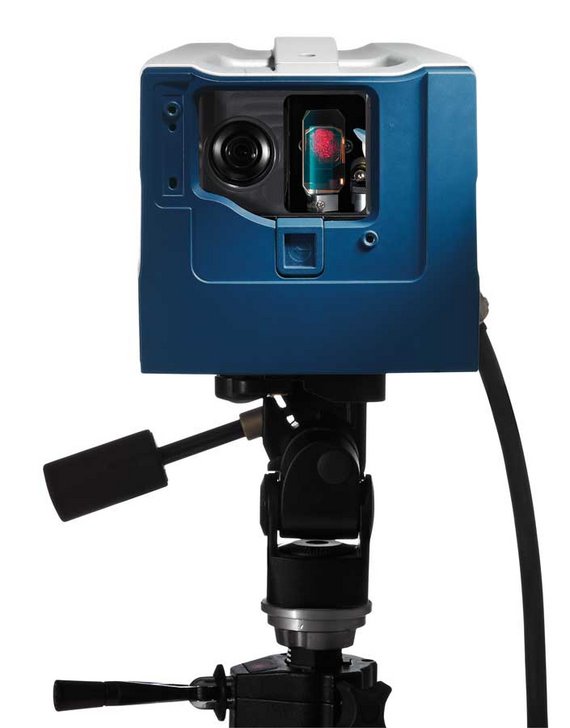
Non-contact 3D scanning vibrometry as measurement solution
For modal testing on tires, the full-field or PSV-3D Scanning Vibrometer is the ideal choice. By choosing the Xtra option for increased optical sensitivity, the measurements can be done directly on black rubber tires rotating with a speed equivalent to an automobile traveling at over 100 km/hr without the need for any surface preparation to enhance the reflectivity.
Polytec uses the so called Xtra technology based on an infrared laser source to facilitate measuring on uncooperative and rotating surfaces, both present with tire testing. The sensor features eye safe (class II) laser safety and a visible alignment laser.
To overcome the adverse optical and mechanical properties of a rotating black tire superior optical sensitivity – the ability to collect and process enough light, the carrier of the vibration information, from the sample – with a high velocity limit is key. The additional challenge comes from the fact that one needs to measure small vibration magnitudes superimposed on very large signals from the rotation. Technically a high DC component needs to be separated from a minute AC component that is responsible for the acoustic emmissions.
The apparent solution is remarkably simple – combine Xtra technology with a specially designed “slow” tracking filter. This combination would meet all the necessary requirements and allow the deflection shapes of tires rotating at high speeds to be measured directly, without surface preparation, thereby giving important insight into the origin of tire noise in an uncomplicated and straight forward way.
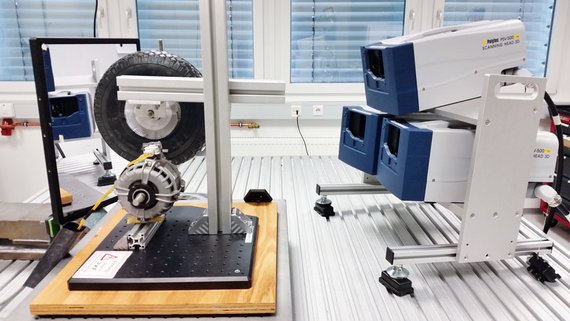
Test setup
A laboratory version of a “roller test bench” was built to verify the proposed solution and the ability of the new PSV-3D Xtra Vibrometer system to improve and simplify the capture of data on a real rolling tire. The rudimentary test fixture consisted of a small 25 cm diameter tire rolling on top of the drive shaft of an electric motor (figure 1).
The PSV-3D Xtra system had its three heads mounted into a common frame and placed on the lab table near the test bench. This common frame simplified the repositioning of the heads when covering different portions of the tire. A large mirror was also used to access different portions of the tire without movement of the common frame.
With this simple measurement set-up, similar results were achieved when compared to those obtained with a real car tire on a commercial roller test bench. In figure 2, the averaged spectrum over all points along the three directions (see the three different colors) is shown. In figure 3, an expanded scale shows the details of the spectrum from 200 Hz to 400 Hz. A comb-like feature is easily distinguished in the spectrum.
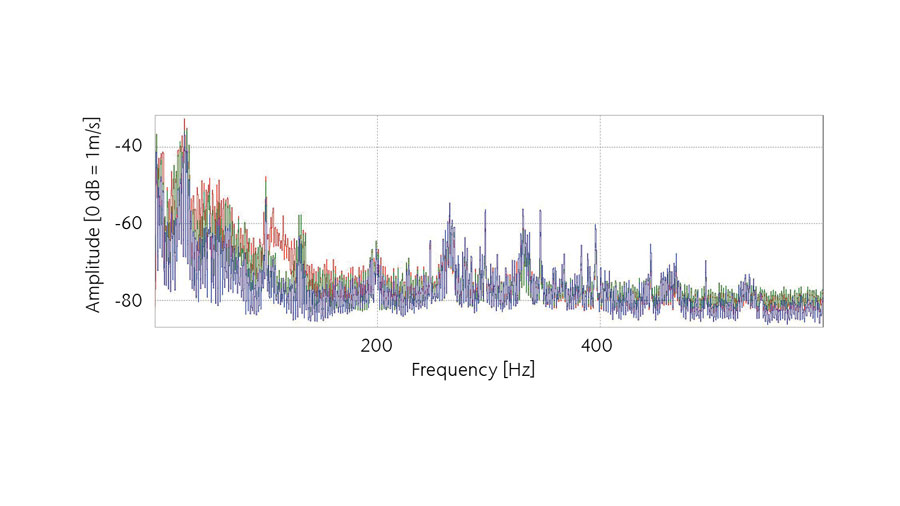
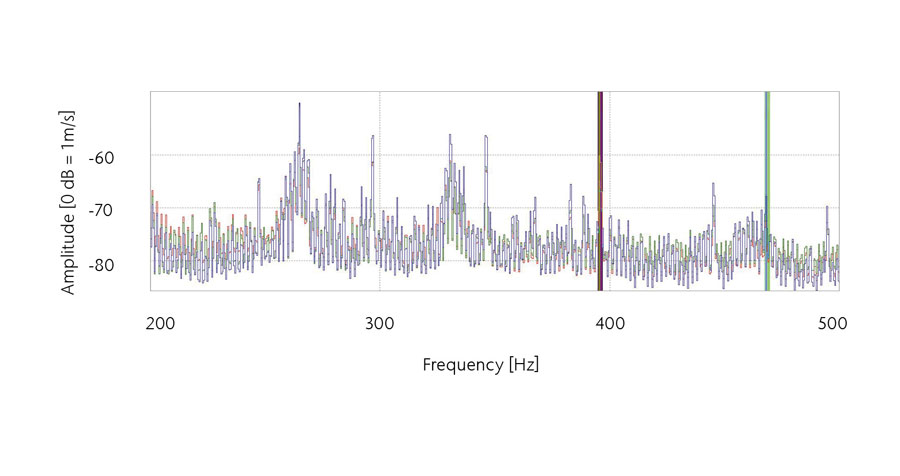
This feature is also observed in real roller test bench studies using the Xtra Scanning Vibrometers. The peaks in this comb feature occur at multiples of the rotation speed of the tire. For tires with a tread pattern, this can be explained by the periodic contact of the treads (and the air pockets in-between) with the road surface.
Clearly, this measurement setup permits the observation of the effect of tread design on the structural resonances of the tire at different speeds and under different loading conditions.
Simplified capturing of deflection shapes
With the Xtra Sensor Heads, a much larger area of the rolling surface can be measured in a single scan. When the first surface scan is completed, the heads are repositioned to capture a second rolling surface. The second position is known relative to the first position by using reference points with known position coordinates detected by a built-in distance sensor. In this way, the results of each surface measurement can be stitched together, leading to one unified deflection shape and one animation of that the shape.
By extending this technique, the tire and it’s side wall can be covered quickly, taking advantage of fewer scans that cover larger surface areas and are subsequently stitched together. The Xtra option permits an excellent signal-to-noise ratio (SNR) despite the fast rotating black tire surface and the larger scan areas.
Some typical deflection shapes are shown in figure 4 at 396 Hz and 468 Hz. A typical pattern of several maxima on the deflection shape is seen in the figure. As one would expect, very similar results are obtained in commercial tire test stands.
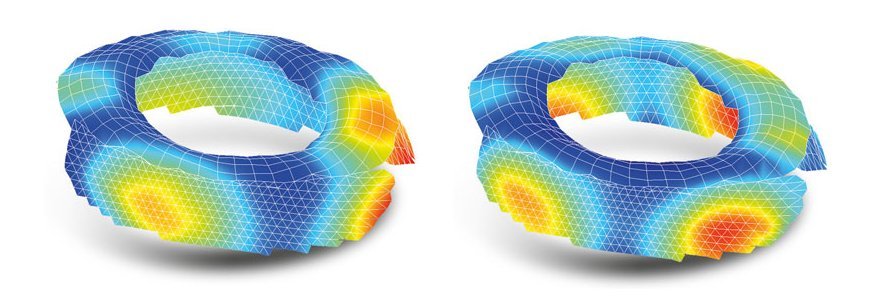
In conclusion, a PSV-3D Scanning Vibrometer utilizing Xtra infrared sensing technology has accurately captured the spectral patterns and deflection shapes of the tire’s fast-moving rolling surfaces, yielding important information on the vibration behavior of the tire surface which is at the origin of the emitted noise. These analytical results combined with numerical simulations of tires will allow the refinement of FE models and the control and minimization of rolling tire noise through the design of better tires.
Images courtesy: Images courtesy of the authors unless otherwise specified. Cover image: ©lassedesignen/ fotolia.com