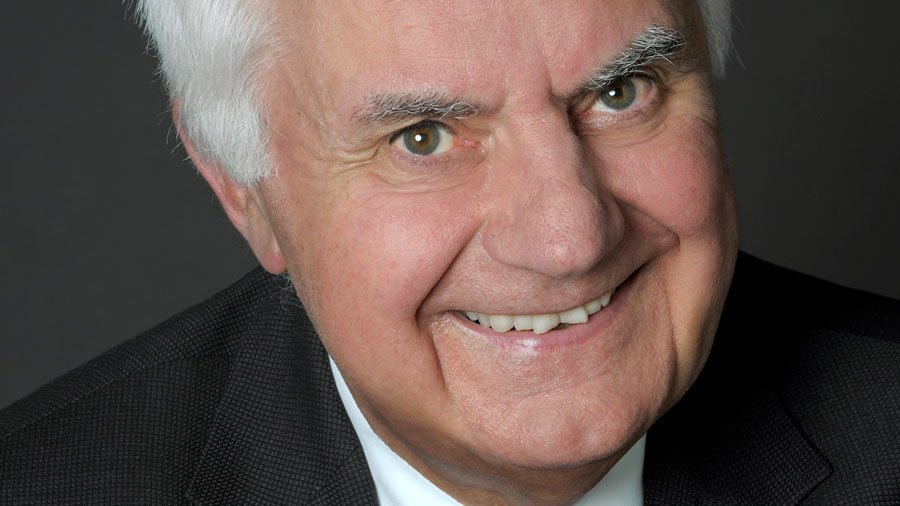
We talked with Prof. Dr. Albert Weckenmann of the University of Erlangen-Nuremberg, Germany, about the limitations of tactile surface measurement technology and the opportunities of non-contact methods.
Polytec is headquartered in Waldbronn and you were also born in Waldbronn. Can we say that Waldbronn is famous for its experts in metrology?
That’s a nice question for an introduction. Well, we are both working on making Waldbronn known as a nucleus for metrology. Waldbronn became known as the cradle of high-quality metrology with the establishment of Polytec. When I made my decision to dedicate myself intensively to metrology, I still had to "emigrate" in order to meet like-minded people and to find the right technical-scientific environment.
Today, Polytec is a kind of incubator for young professionals as well as a flourishing company. This shows our young researchers how successful you can be with metrology, and at the same time, how interesting optical measurement technology is.
So it can surely be said that Waldbronn's atmosphere offers a globally successful climate that at least favors metrology and offers great perspectives to interested people. Today it is no longer necessary to "emigrate" in order to make a fortune in metrology.
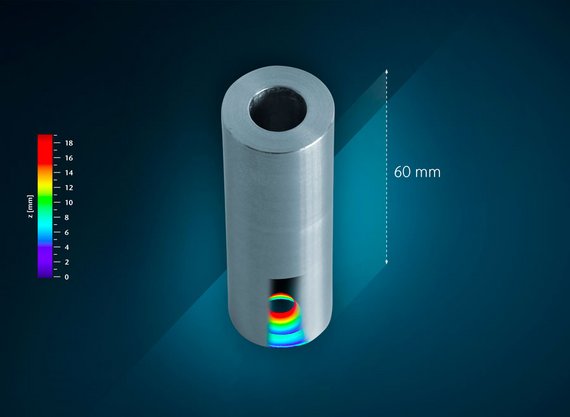
In manufacturing industry, most of the surfaces are still characterized by tactile measurement techniques even though optical methods provide many advantages. Why do you think manufacturing metrology is still dominated by tactile methods and what should be done to get a higher acceptance of optical methods?
There are historical reasons. Surface parameters were defined for the first time in the middle of the last century when the expert community put its faith in tactile methods. Other methods were simply not available. At that time there were neither optoelectronics nor computers. Only tactile measurement parameters could be defined for specifying workpiece surfaces, established in standards and noted on technical drawings along with which measurement instruments were available at that time.
Technologies have since advanced in terms of surface requirements, manufacturing procedures and measurement techniques. When well defined, established and standardized parameters are changed, the entire chain – from standardization via design, manufacturing, quality assurance up to the measurement techniques and the interpretation of the results – must keep pace with the development.
Almost all of the people involved in specifying, manufacturing and quality assurance, such as operators, technicians and engineers, must be retrained, and the question arises whether the "old" technical drawings are still valid. So there are some very good reasons why people involved with production measurement technology have very conservative attitudes.
Optical methods are therefore being introduced very tentatively into surface measurement technology. The acceptance can be accelerated only moderately through measures that are aimed at conviction and acceptance. This in turn means investment in trade fairs, printed material, measurement examples, discussions, training courses and so on.
As an expert in the field of metrology, which advantages of optical surface measurement techniques provide the most benefits to the end-users?
The benefits range from the fast, two-dimensional application to the capture of a three-dimensional topography with an extremely high density of points. Also, the evaluation procedure should be appropriate to product functionality. Unfortunately this is missing in most cases.
Today, industry has the most experience with tactile techniques and if a new approach like optical is introduced, users always want to compare the results. It is however not always possible to compare them directly. What can you say about the conditions required to compare results from two different measurement techniques?
It is better not try to compare results with one another. The comparison is misleading in all aspects. By the way, what can be done with the measurement result? If you want to determine the expected functionality, then many of the standardized parameters such as Ra, Rq, Rz and others are hardly of any use for it.
Nobody can and should aim to replace tactile measurement technology. In areas where this technology is established, it will continue to be applied. It makes more sense to use the many fold advantages of the optical data acquisition for new applications and to extend the computerized evaluation in such a way that the degree of the expected functionality can be predicted.
There are different optical methods for characterizing surfaces. Each one has its advantages and limitations. The end-user wants to see results, or in other words his or her aim is to characterize the product or process based on the measurement results. From this point of view, how would you define a measurement result that satisfies the end-user?
Surface measurements are carried out with two main goals. One is to predict the functionality, in other words: how well it fulfills the functional requirement; the other is to correct the production process. When the measurement provides the expected and required information with the necessary precision, under the prevailing ambient conditions and within the time frame which is necessary for the process management, then the end-user is satisfied.
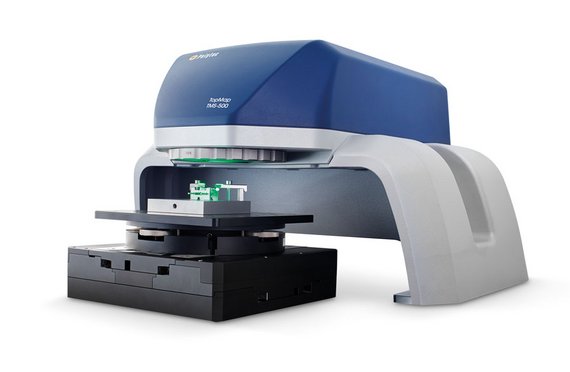
Polytec’s optical surface measurement instruments work with on the principle of white light interferometry. However, different from other manufacturers, large measurement fields (up to 30 x 40 mm) can be acquired with fine vertical resolution. This high level of information is available very quickly, especially for applications where function-oriented surface characterization is required. As a pioneer in the field of function-oriented characterization of technical surfaces, which other aspects are also beneficial for the end-user?
The user has to choose the most suitable method for his measurement task.
Many parameters have to be taken into account: What area of the workpiece should be measured and what is the material, the function of the surface, the manufacturing process, the parameters of the manufacturing process, the envisioned topography, ambient conditions, integration into networks, connection with Industry 4.0 structures and many more.
In every case, the user should consider before the measurement, whether there is any need to measure at all and how the measuring effort can be minimized. There is only a need to measure what will be processed further, required for documentation or necessary in the event that there are complaints or liability claims. Costs can be saved if nothing will be done with the measurement results!
Although the level of available information about products in micro- and nanometer dimensions is increasing (thanks to optical methods), industry is still trying to solve problems with macro-dimensional methods. You are an expert for GPS (geometrical product specifications) so what can you say about the future of GPS for this new field?
The GPS tolerancing system will definitely be required in the future; after all, we do not only have micro-nano parts!
For micro- and nanotechnology (e.g. structured surfaces with a resolution in the nanometer range), constructive, creative solutions have to be invented - in particular a specification system compatible with GPS or a new tolerancing system. A simple reduction or miniaturization of the processes and parameters would not be enough – considering the laws of the physics – because the aspects of physical principles require other measures.
Rotational movements, for example, which are mainly used in the macro area are no longer applicable in the nano area. Elastic torsional and bending movements are being increasingly used; this forces us to develop new ways of thinking for the realization of functional requirements and the design of components.
How would you characterize the future of optical surface measurement instruments?
The application of optical surface measurement instruments will increase steadily but slowly.
Optical measurement technology will not displace tactile surface measurement technology, but complement it.
Measurement principles and the measurement techniques based on them have been developed to become efficient measurement instruments which comply with requirements and constitute a solid basis for further developments and adaptions to the respective purposes.
Optical measurement technology will be used at an increasing rate for micro and nano technologies among other things. After the development of instruments, which have already achieved a high level, now the focus must be evaluation. After a function-oriented specification of the parameters, something new must be created for verifying the manufactured components in order to evaluate them.
In future, nobody will be interested in contemplating "data graveyards". Existing knowledge about product functionality should be used in a way that the degree of product reliability can be inferred from the measurement result.
And last but not least: The metrology must also be suitable for Industry 4.0 and AMP 2. This is a challenge for all companies, but especially for those branches that are oriented towards quality assurance.
I wish Polytec the best of luck and always the right ideas to meet these challenges. The surroundings of Waldbronn with the KIT in Karlsruhe and the University of Stuttgart a little bit further afield, with their committed and ambitious institutions as well as numerous manufacturing companies in the region, are an excellent environment to meet the challenges of the future.
Prof. Dr. Weckenmann, we thank you for this interview and wish you the very best for your future.
Images courtesy: Images courtesy of the authors and Polytec unless otherwise specified.