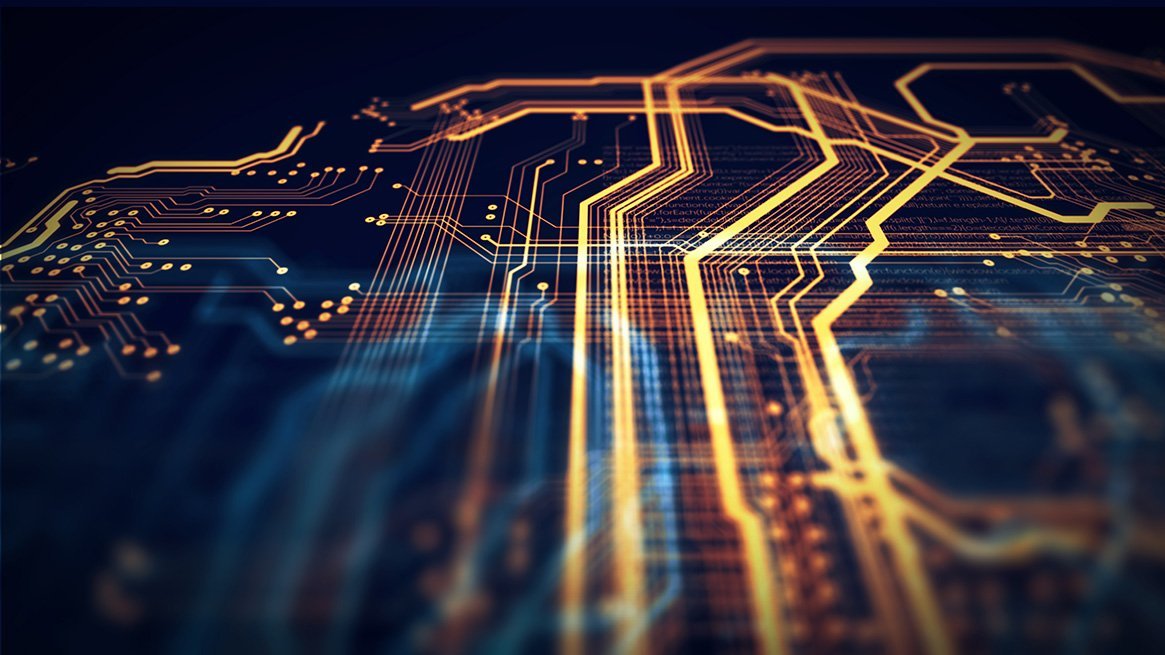
Die Technik der gedruckten Elektronik hat das Pionierstadium hinter sich, erste industrielle Anwendungen laufen bereits. Die möglichen Einsatzgebiete sind vielfältig, aber es fehlte bislang noch an schlüsselfertigen Systemlösungen, die Industriekunden den Einstieg erleichtern.
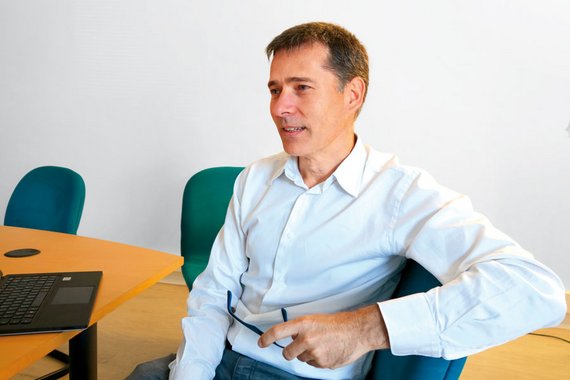
Kelenn Technology, ein französischer Druckerhersteller und Bildverarbeitungsanbieter, hat einen Tintenstrahldrucker für gedruckte Elektronik auf den Markt gebracht. Mit Hilfe von metallischer Nanopartikel-Tinte lassen sich A4-große, flexible Bedruckstoffe wie Papier, Folie oder Textilien mit elektronischen Schaltungen bedrucken – automatisiert und in Auflagen von bis zu 10.000 Bögen pro Tag.
Didier Rousseau, Geschäftsführer und Unternehmensgründer von Kelenn Technology hat mit Polytec über die Entwicklung des KSCAN PE gesprochen.
Womit beschäftigt sich Ihr Unternehmen, Herr Rousseau?
Kelenn wurde 2005 gegründet. Am Hauptsitz in Paris beschäftigen wir 23 Mitarbeiter und es gibt derzeit zwei Niederlassungen in den USA und in Indien. Wir stellen Bildverarbeitungssysteme, Drucker für industrielle Anwendungen und entsprechende Software her.
Unsere Tintenstrahldrucker liefern wir hauptsächlich an Kunden, die sie im postalischen Bereich für Adressierung, Frankierung, Transaktionen, Direktmailings, aber auch in der Dokumentensicherheit, in der Verpackungsindustrie, für Folienanwendungen oder im Bereich der gedruckten Elektronik einsetzen. Unsere industriellen Bildverarbeitungssysteme übernehmen Aufgaben wie Identifikation, Objektverfolgung, Kontrolle, Vermessung und Sortierung in großen und schnellen Produktionsprozessen.
Kelenn verfolgt das Ziel, einerseits die Produktionskosten des Kunden zu senken und andererseits Mehrwert durch eine 100%-Qualitätskontrolle zu schaffen.
Worum ging es bei der Entwicklung des neuen KSCAN PE?
Im Markt für gedruckte Elektronik finden sich verschiedene Technologien, um leitfähige Tinten auf verschiedene Substrate zu drucken. Eine davon ist die Tintenstrahltechnologie, deren Vorteil ganz klar in der großen Präzision der Druckergebnisse liegt. Allerdings ist der Prozess mit vielen Schwierigkeiten behaftet, wie zum Beispiel der Wiederholbarkeit und Dauerhaftigkeit der Ergebnisse. Wir wollten ein All-in-one-Drucksystem für industrielle Produktionsumgebungen schaffen, das den Tintenstrahldruck leitfähiger Tinten mit dem Sinterprozess verbindet. Dieser ist notwendig, um dauerstabile, leitfähige Verbindungen zu schaffen. Das System sollte unterschiedliche Substrate in Einzelbögen von maximal A4-Größe in raschem Durchsatz verarbeiten.
Und beim Sintern kam Polytec ins Spiel?
Polytec war der ideale Entwicklungspartner für das Projekt, weil das Unternehmen viel Know-how über den photonischen Sinterprozess einbringen konnte und seit Jahren den amerikanischen Hersteller von UV-Blitzsystemen, die Xenon Corporation, in Europa vertritt.
Gab es denn Alternativen zu den Xenon-Sintersystemen?
Nicht wirklich. Xenon war insofern ohne Alternative, als dass wir eine industriefähige Lösung anstrebten, die mit hohen Taktraten bzw. hohen Auflagen zurechtkommen sollte. Andere Technologien wie das thermische Sintern in Sinteröfen kamen nicht in Frage, weil der Sinterprozess dort wesentlich länger dauert. Außerdem ist er mit einem hohen Temperatureintrag ins Substrat verbunden, was wiederum wärmeempfindliche Substrate wie z.B. Folien ausschließt.
Beim photonischen Sintern hört man immer wieder von Problemen, gleichförmige Sinterergebnisse über größere Flächen zu erzielen, Stichwort „Stitching“. Und eine A4-große Fläche ist ja nicht eben trivial, wie war das bei Ihnen?
Wir sintern die Fläche mit einer U-förmigen Blitzlampe und mehreren Pulsen. Mit Stitching, also Überlappungen oder Unterbelichtungen an den Rändern des Wirkbereichs, haben wir keinerlei Probleme.
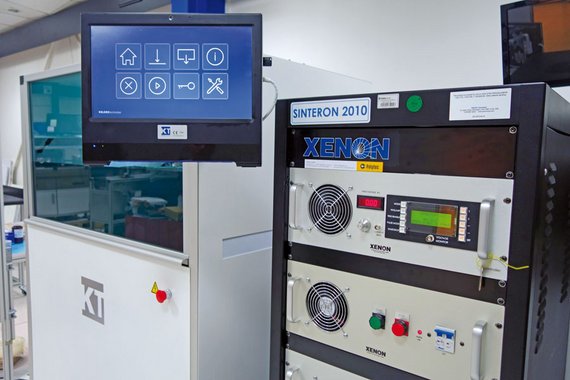
Wie gestaltete sich die Unterstützung durch Polytec während des Projekts?
Polytec hat uns in der Entwicklung sehr unterstützt. Einerseits durch das schon erwähnte tiefgreifende Know-how des Sinterprozesses. Andererseits konnten wir über mehrere Monate Xenon-Systeme testen, um die Machbarkeit zu belegen und die Integration zu gewährleisten. In dieser Zeit hat uns Polytec oft mit wertvollem Feedback und Vor-Ort-Beratung geholfen, den Sinterprozess auf die anderen Prozessschritte abzustimmen und produktionstauglich zu machen.
Konnte die Entwicklung des Systems denn planmäßig abgeschlossen werden?
Nicht ganz (lacht). Der Druck der metallischen Nanopartikel-Tinten in Verbindung mit dem Sinterprozess ist ein sehr komplexes Verfahren, das uns über ein Jahr Entwicklungszeit gekostet hat. Wir standen Phänomenen gegenüber, die uns völlig neu waren und mussten die Tintenzusammensetzung unzählige Male verändern, die wiederum direkt den Druck- und den Sinterprozess beeinflusst. Es war ein sehr zeitaufwändiger, harter Job.
Worin liegt der wesentliche Vorteil des KSCAN PE?
Eigentlich muss man sogar von 5 Vorteilen sprechen: Zum einen erreichen wir dank des photonischen Sinterprozesses eine herausragende Produktionsgeschwindigkeit von 10.000 Bögen pro Tag. Dann können wir unterschiedlich flexible und wärmeempfindliche Substrate wie Papiere, Folien, Textilien usw. bedrucken. Der dritte Vorteil besteht darin, dass wir in gewisser Weise auch 3D drucken können, also erhabene Strukturen auf dem Substrat. Viertens ermöglicht die Genauigkeit der Tintenstrahltechnik minimale Schichtdicken von 200 Nanometern bei gleichbleibender Leitfähigkeit von 100 Millisohm pro Quadratzentimeter. Damit ist die Technik deutlich effizienter als beispielsweise der Siebdruck. Und das schlägt sich unmittelbar in geringeren Kosten für die silberhaltigen Tinten nieder.
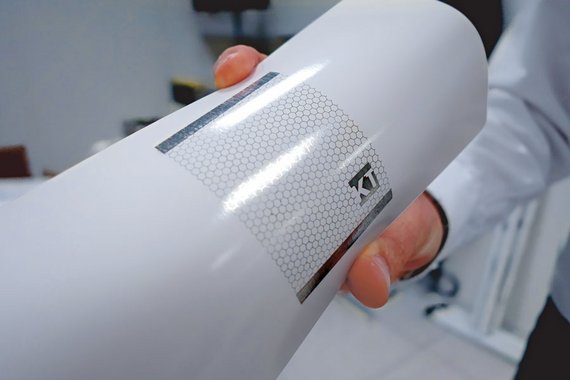
Last but not least muss natürlich erwähnt werden, dass Kelenn als erstes Unternehmen ein schlüsselfertiges All-in-one-System liefert.
Und für welche Märkte ist das System interessant?
Da kommen sehr viele Anwendungen in Betracht, allein durch die zahlreichen möglichen Bedruckstoffe. Eine Hauptanwendung ist derzeit der Druck von RFID-Antennen zum Objekttracking. Aber auch OLEDs, Batterien oder organische Photovoltaikschaltungen können gedruckt werden. Den Hauptmarkt sehen wir derzeit in der Medizin- und Gesundheitsbranche, wo RFIDs dank der geringen Größe und Flexibilität vielfältige Anwendungen finden.
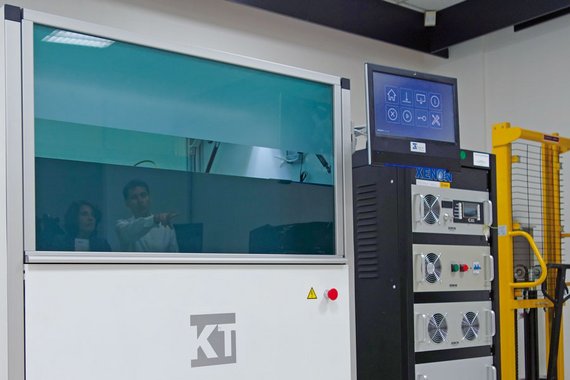
Und welches Fazit würden Sie aus heutiger Sicht ziehen?
Ohne Polytec hätten wir diese innovative Lösung nicht auf die Beine stellen können. Wir wollen den eingeschlagenen Weg zusammen fortsetzen und das System weiterentwickeln, um noch viele weitere Anwendungsmöglichkeiten zu finden und umzusetzen.
Bildnachweise: Soweit nachfolgend nicht anders aufgeführt bei der Polytec GmbH. Titelbild: spainter_vfx/shutterstock.com