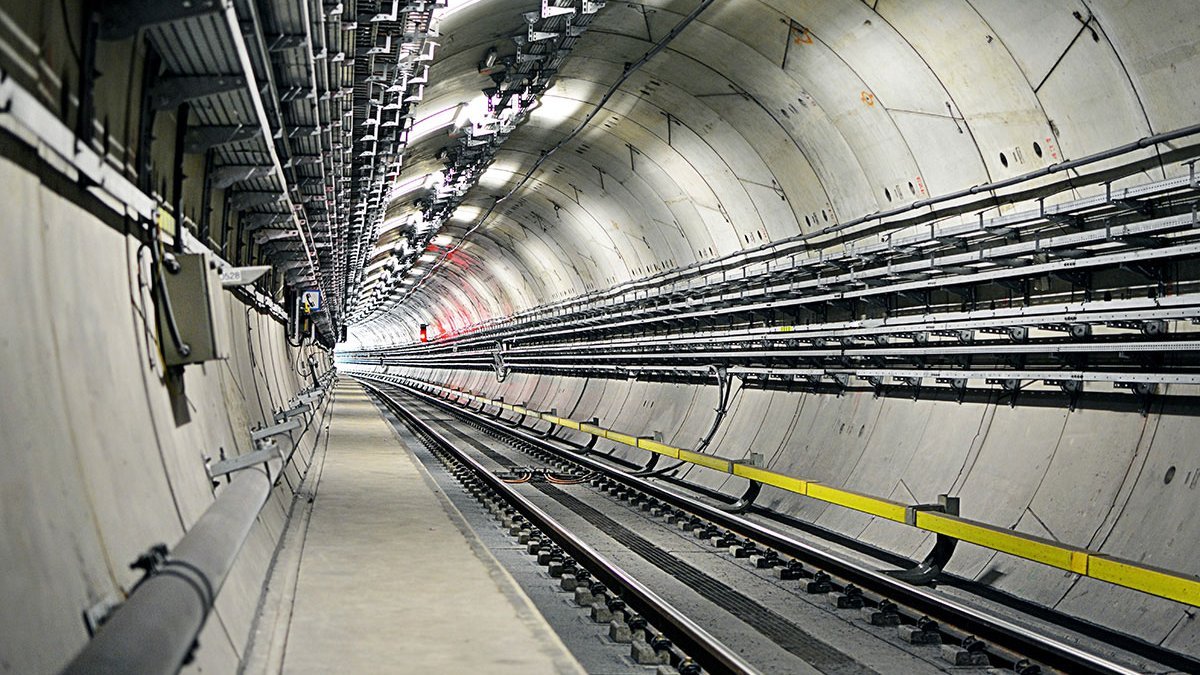
Steine, Blöcke, Stahl, Zement, Beton und Mörtelschlamm und dies alles in Kombination mit großen, schweren, ungelenken und lärmenden Baumaschinen, das klingt nicht gerade nach dem idealen Ort für eine fragile, aus Glas bestehende Faser (Bild 1 und 2). Aber genau da, auf den Baustellen, werden sie gebraucht, die faseroptischen Sensoren. Denn eine Belastungsänderung des Bodens, zum Beispiel durch einen Neubau, führt auch zu einer Volumenänderung. Dabei entstehen Hebungen oder Setzungen, welche auch umliegende Bauwerke beinträchtigen können.
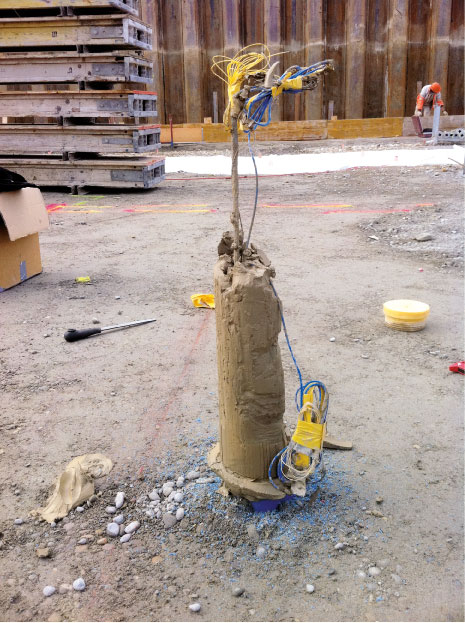
Die Technologie
Für die Baustellenüberwachung gibt es verschiedene bewährte Methoden, die jedoch im Allgemeinen auf punktuelle Informationen limitiert sind. So kann beispielsweise die Verschiebung eines Messpunktes geodätisch ermittelt werden oder es kann die Längenänderung einer Strecke mittels Extensometer erfasst werden. Was darum herum passiert, bleibt im Dunkeln. Die verteilte faseroptische Sensorik bietet hier Methoden, welche es erlauben, Informationen lückenlos über große Distanzen zu messen. Die Firma Marmota Engineering aus der Schweiz ist auf faseroptische Überwachungslösungen für geotechnische Anwendungen spezialisiert und arbeitet mit Hochdruck daran, diese Technologie auf den Baustellen als akzeptierte, vorteilhaftere Alternative zu etablieren.
Für die Überwachung von langen, eindimensionalen Bauwerken wie Pipelines gibt es schon seit einiger Zeit verteilte Sensoriklösungen, die auf jedem Meterabschnitt eines bis zu 30 Kilometer langen Kabels die Dehnungen aufzeichnen können. Mit Rayleigh-Sensorik-Systemen des US-amerikanischen Herstellers Luna stehen potente Werkzeuge für Anwendungen zur Verfügung, die eine viel höhere räumliche Auflösung erfordern. So kann mit solchen Systemen über eine Strecke von 70 Metern mit einer räumlichen Auflösung im Millimeterbereich eine Dehnung bestimmt werden. Damit können entlang eines einzelnen Kabels Tausende von „individuellen Dehnmessabschnitten“ definiert werden. Und das mit einer hohen Genauigkeit im Microstrain-Bereich (Längenänderung in Mikrometer pro Meter).
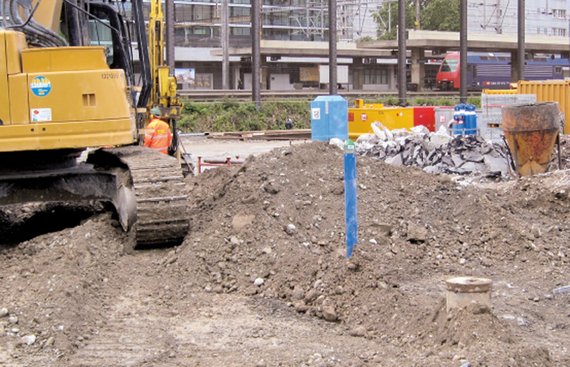
Bohrlochsensoren in Rutschhängen und Baugruben
Wird ein verteilter faseroptischer Sensor in einem Bohrloch platziert, können Dehnungen über die Tiefe exakt verfolgt werden. Die erhaltene Information führt dazu, dass kritische Setzungen aufgrund einer Zusatzbelastung durch den Bau oder Bewegungen eines Hangkriechens in einem beliebigen Winkel zur Bohrlochachse rasch erkannt werden können.
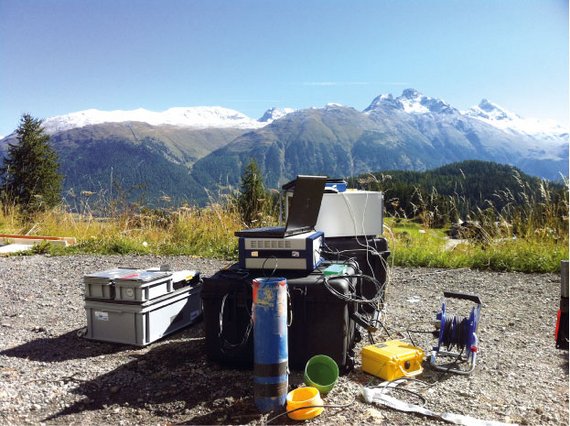
Vor allem bei Kriechhängen kann die Scherfläche, also die räumliche Begrenzung der Rutschung in der Tiefe, von sehr geringer Mächtigkeit sein und so eine hochauflösende Messung erfordern, damit die Scherfläche rasch lokalisiert werden kann. Für Bohrungen bis 70 Meter Tiefe ist die Rayleigh-Sensorik bestens geeignet, kann hiermit doch die Dehnung auf jedem Zentimeterabschnitt erfasst werden. Verschiedene Bohrloch-Projekte wurden in den letzten Jahren durchgeführt und ausgewertet, darunter mehrere in den Schweizer Alpen (Bild 3). Dabei hat sich gezeigt, dass mit dem Rayleigh-System die Scherfläche innerhalb von kurzer Zeit detektiert und lokalisiert werden kann. Und dies mit geringerem Installations- und Messaufwand als mit herkömmlichen Inklinometern, welche auf dem Prinzip der Neigungsmessung im Bohrloch basieren.
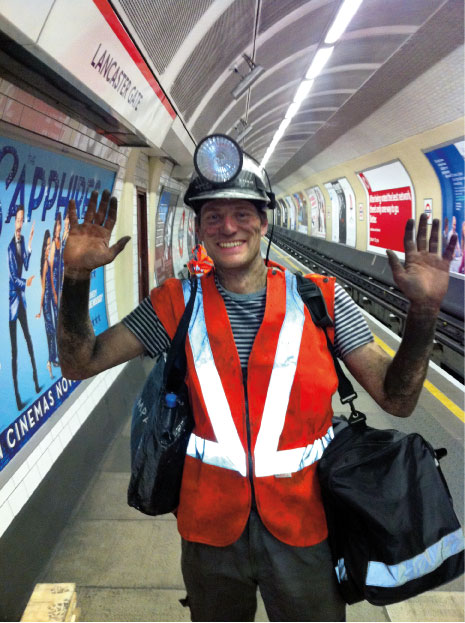
Infrastrukturüberwachung
Ein Beispiel aus der Infrastrukturüberwachung vermag vielleicht noch anschaulicher die Stärken der verteilten Sensorik hervorzuheben. So wurde im Rahmen des Jahrhundertprojekts Crossrail, bei welchem zwei neue Eisenbahntunnel die gesamte britische Hauptstadt London unterqueren, ein besonders gefährdeter Abschnitt eines bestehenden Underground-Tunnels instrumentiert. Denn die Neubautunnel im bereits stark durchlöcherten städtischen Untergrund führen zum Teil nur wenige Meter an bestehenden, bis zu hundertjährigen Tunnels vorbei.
Diese sind nach wie vor in Betrieb, weshalb die bestehenden Bauwerke während des Bohrens der neuen Tunnel minutiös überwacht werden müssen. Neben den quantitativen Deformationen war in diesem Projekt auch die Art der Verformung von großem Interesse. Wird die Last durch Deformation in den Gelenken zwischen den einzelnen Gusseisen-Elementen der Tunnelstruktur abgetragen oder durch Verformung der Elemente selbst (Bild 6). Pro Laufmeter Tunnel hätten zur Beantwortung dieser Fragestellung vier Dehnungssensoren installiert werden müssen, was 280 Einzelsensoren über 70 Meter entspricht, oder eben ein einziger verteilter Rayleigh-Dehnungssensor.
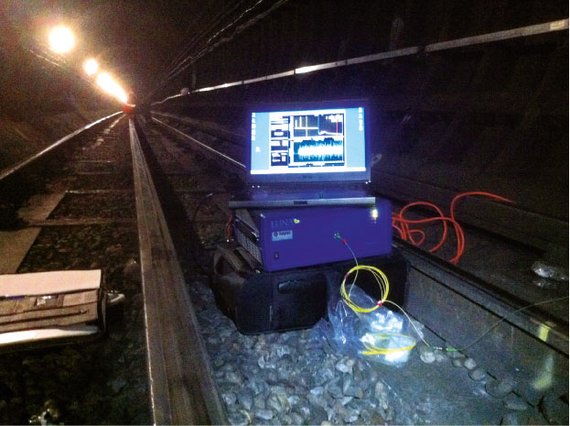
Es ist erkennbar, dass sowohl die Installation eines einzigen Sensorkabels als auch die anschließende Messung einen viel geringeren Aufwand bedeutete, als die Installation von hunderten Einzelsensoren und deren einzelne Auswertung. Vor allem wenn noch in Betracht gezogen wird, dass die Installation nur in den Nachtstunden zwischen 1 Uhr und 5 Uhr erfolgen konnte. Trotz allem, die Instrumentierung war auch so noch genügend anstrengend: Die Wärme und der seit Jahrzehnten abgelagerte Schmutz hat dem Team alles abverlangt (Bild 4).
Ende 2012 war es dann soweit und die Tunnelbohrmaschine hat den instrumentierten Abschnitt unterquert. Während zwei Wochen wurden in Zusammenarbeit mit der ETH Zürich und dem Imperial College London, welche noch weitere Instrumentationen vor Ort betrieben, die Sensoren kontinuierlich gemessen (Bild 5).
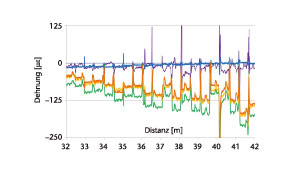
Fazit und Ausblick
Die oben gezeigten Beispiele sowie weitere kommerzielle Anwendungen während der letzten Jahre haben gezeigt, dass die Rayleigh-Messtechnik im Vergleich zu konventionellen Methoden einige Vorteile aufweist. Dies gibt dem Bauherrn und dem Infrastrukturbetreiber die Möglichkeit, schneller und spezifischer Maßnahmen zu ergreifen, bevor Schäden entstehen. Oder aber, es können Kosten eingespart werden, indem gemessen anstatt überdimensioniert wird.
Die Grenzen der Anwendung sind momentan vor allem instrumentationstechnischer Natur: So muss die Sensorauswahl und die Befestigungstechnik der Problemstellung angepasst werden und es muss garantiert werden können, dass die Sensoren während der ganzen Überwachungszeit funktionsfähig bleiben. Dazu gehört auch der Einbezug der Maximaldehnung, welche die Sensoren erfahren dürfen, bevor die Faser bricht.
Generell hat sich die Technologie bereits in mehreren Projekten bewährt. Nun geht es hauptsächlich darum, diese neuen Messmöglichkeiten einem breiteren Publikum schmackhaft zu machen. Denn nur wenn die Projektingenieure von diesen Überwachungsmethoden Kenntnis haben, können sie diese auch in ihr Projekt miteinbeziehen. Dafür können sie ruhiger schlafen mit der Gewissheit, dass verteilt – das heißt lückenlos – alle Gefahrenstellen überwacht werden.
Dank
Das Crossrail-Projekt und vor allem die Forschung auf dem Gebiet wurde in Zusammenarbeit mit dem Institut für Geotechnik der ETH Zürich und dem Imperial College London ausgeführt.
Bildnachweise: Soweit nachfolgend nicht anders aufgeführt bei Marmota Engineering AG, Schweiz. Titelbild: Martyn Jandula/shutterstock.com