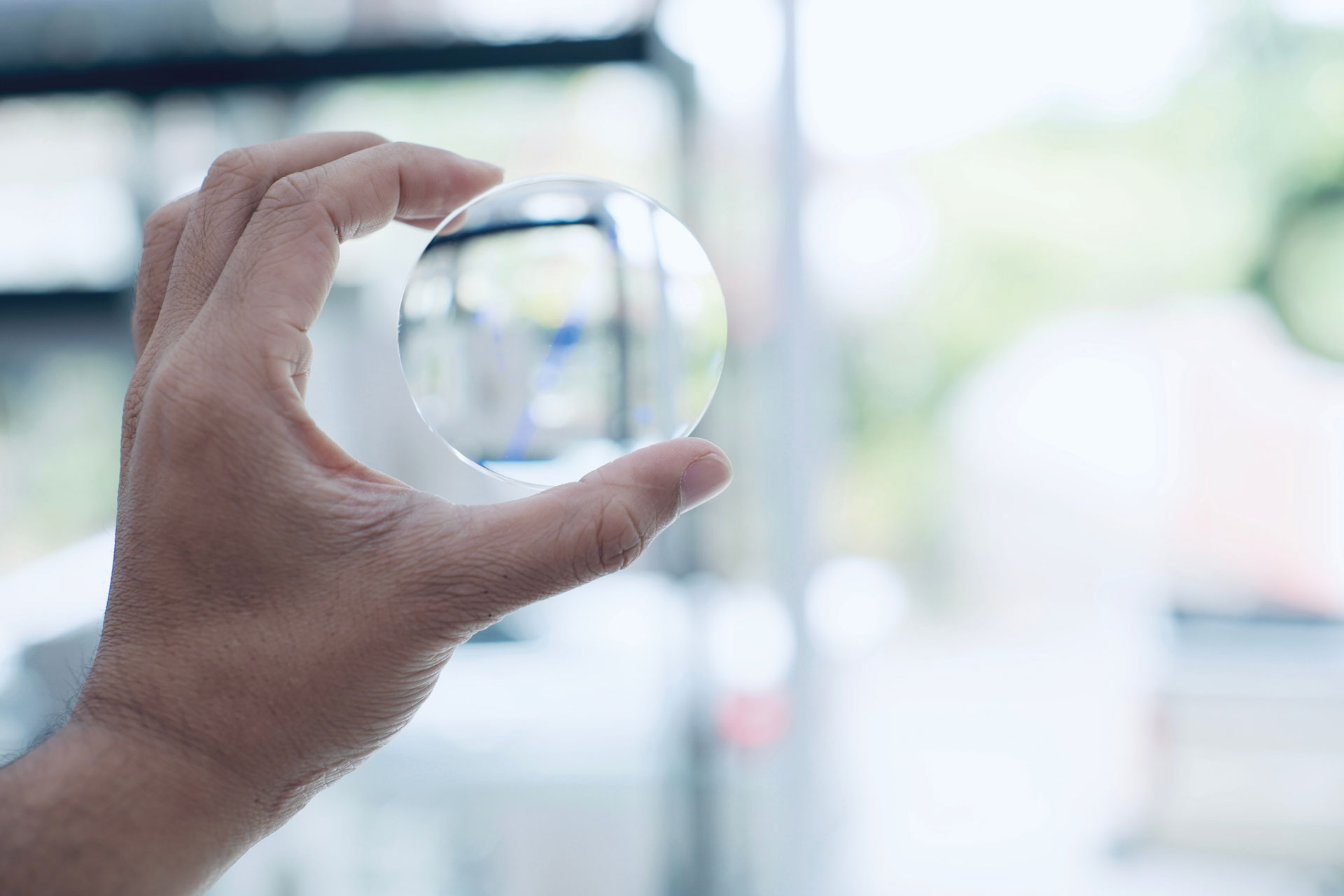
Durch den Einsatz von optischen Freiformflächen können komplexe Linsensysteme vereinfacht und somit kompakter und gewichtsoptimiert realisiert werden. Darüber hinaus ermöglicht der Einsatz optischer Freiformflächen die Realisierung völlig neuer Funktionalitäten. Gleichzeitig ist ihr Herstellungsprozess komplex und dadurch zeitintensiv und teuer. Die Herstellung individueller Freiformen in kleinen Losgrößen kann durch den Einsatz einer CNC-Maschine effizient erfolgen.
An der Ernst-Abbe-Hochschule (EAH) Jena arbeitet man an der Optimierung des Herstellungsprozesses mit dem Ziel, anhand von während der Oberflächenbearbeitung aufgezeichneten Schwingungsdaten und einer direkt durchgeführten Auswertung durch künstliche Intelligenz, eine Vorhersage über die Bauteiloberflächengüte zu treffen. Hierzu werden die auf die Prozesskette wirkenden Einflussgrößen identifiziert, quantifiziert und so optimiert, dass ein bestmögliches Fertigungsergebnis erzielt wird.
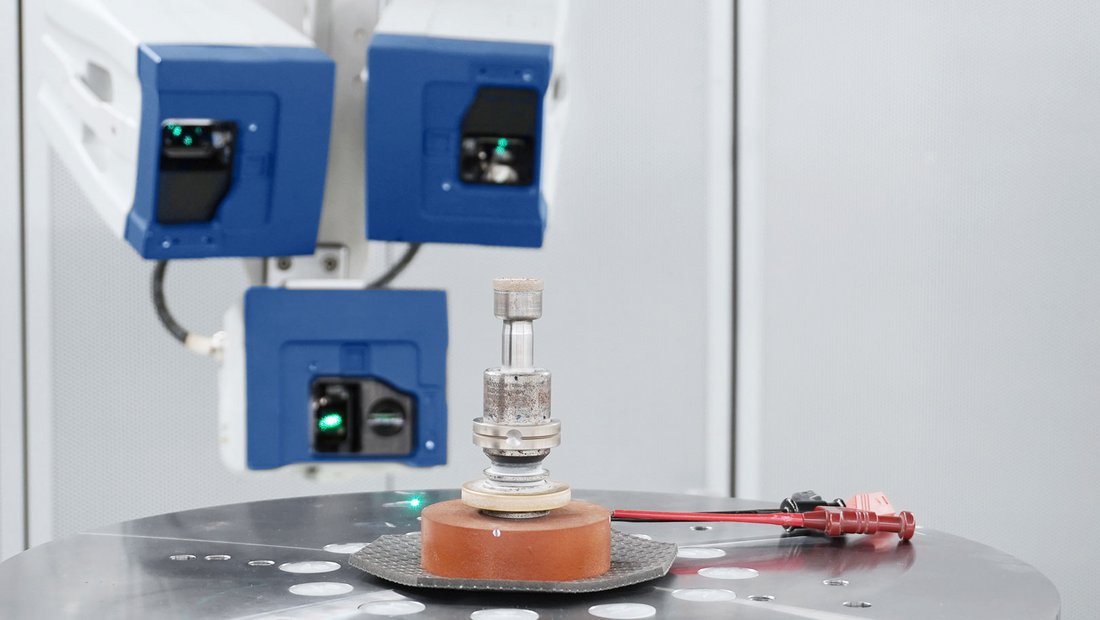
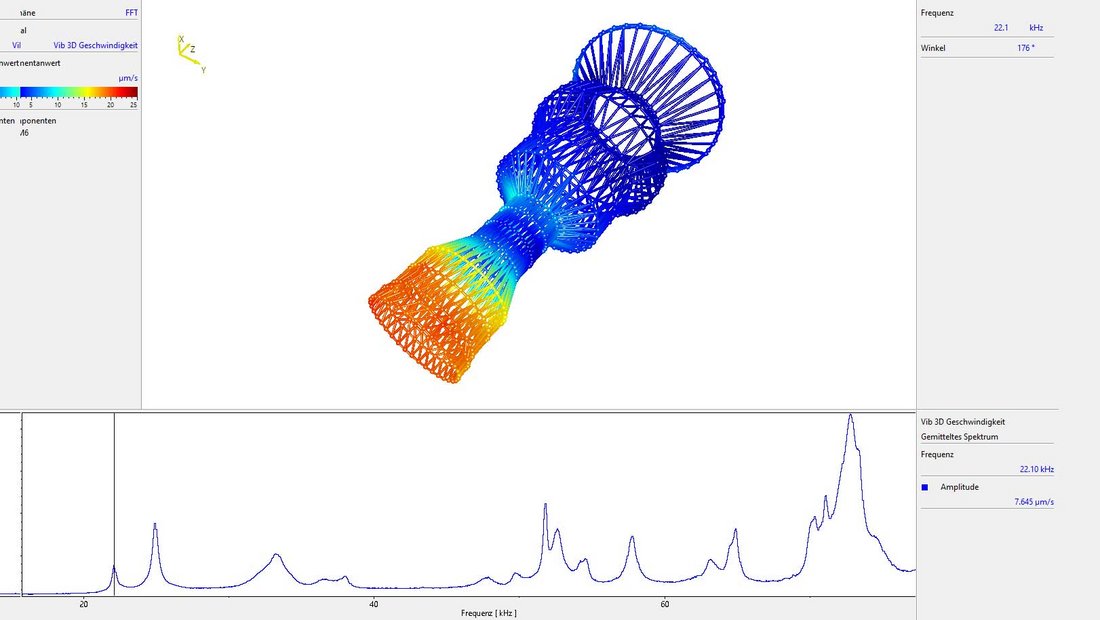
Einfluss Maschinenparameter auf Oberflächengüte
Eine optische Freiformfläche soll nicht nur eine hohe Formtreue besitzen, sondern auch möglichst geringe kurz- und mittelfrequente Oberflächenfehler aufweisen, welche beispielsweise durch Vibrationen während des Herstellungsprozesses entstehen. Der bestmögliche Ausgangszustand für die Politur optischer Bauteile wird durch den Feinstschleifprozess erreicht. Die Prozesskette vom Grobschleifen über das Feinschleifen bis hin zum Feinstschleifen unterliegt jedoch zahlreichen Einflussgrößen, die die Qualität des Endproduktes beeinflussen.
Neben dem eingesetzten Werkzeug und dessen Ausrichtung zur Oberfläche spielen Prozessparameter wie Drehzahl, Vorschub, Zustelltiefe und die verwendete Ultraschallfrequenz, mit der das Werkzeug angeregt wird, eine wichtige Rolle. Nur eine optimale Wahl aller Stellgrößen führt zu einer Oberfläche, die alle Anforderungen an eine hochpräzise Optik erfüllt.
Um die Maschinendynamik der zur Herstellung der Planprobenoberflächen durch ultraschallunterstütztes Schleifen eingesetzten 5-Achs-CNC-Maschine zu untersuchen und die bestmögliche Maschineneinstellung zu identifizieren, ist die Durchführung einer Schwingungsanalyse mittels Laser-Doppler-Vibrometrie sowie die Analyse der Oberflächentextur der bearbeiteten Probe mittels Weißlichtinterferometrie hilfreich.
Frühzeitige Vorhersage der Oberflächengüte mittels KI
Um eine gute Aussage darüber treffen zu können, welche Maschinenparameter das Endergebnis in welcher Weise beeinflussen und dies mit einer möglichst geringen Anzahl an produzierten Prüfmustern, ist eine Unterstützung durch künstliche Intelligenz (KI) sinnvoll. In unserem Fall wird hier KI von der Firma Batix Software GmbH eingesetzt, die ein Modell entwickelt hat, um die Oberflächengüte bzw. den resultierenden Rauheitswert der Oberfläche auf Basis von Maschinenparametern vorherzusagen.
In einem ersten Schritt erstellt die KI aus den verschiedenen zur Verfügung stehenden Vibrometerdaten und Oberflächenkenngrößen einen Prüfplan, um die beeinflussenden Maschinenparameter durch die KI zu identifizieren. Anschließend ist zu prüfen, wie gut die Schwingungsanalysedaten mit den Oberflächenparametern der Weißlichtinterferometrie tatsächlich korrelieren.
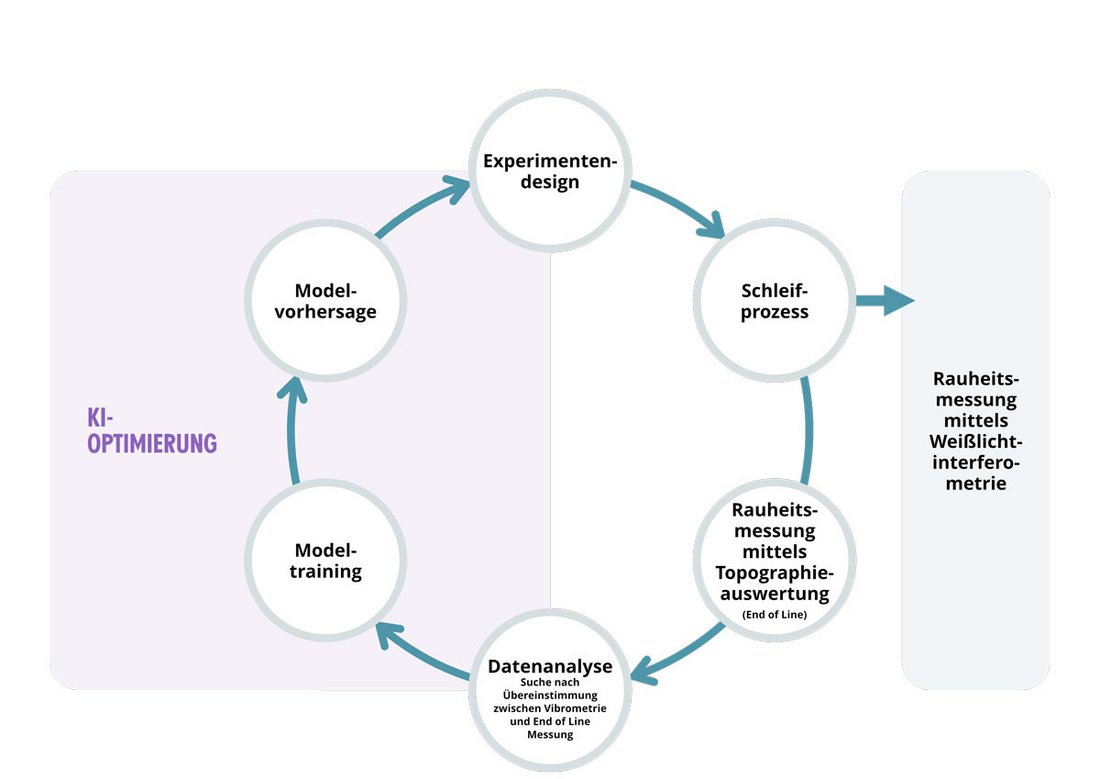
Der Einfluss von Schwingungen auf die Oberflächenqualität
Die Schwingungsanalyse ist sowohl im Stillstand als auch im Betrieb der Maschine sinnvoll. Im Stillstand der Maschine werden durch Anregung verschiedener Maschinenkomponenten mit einem Modalhammer die Eigenresonanzen der Maschinenkomponenten ermittelt, um im Betrieb zu vermeiden, dass ungünstig gewählte Werkzeugdrehzahlen und Ultraschallfrequenzen die Eigenresonanzfrequenzen dieser Komponenten anregen und zu unerwünschten Schwingungen während des Fertigungsprozesses führen und damit die Oberflächenqualität des fertigen Produktes negativ beeinflussen.
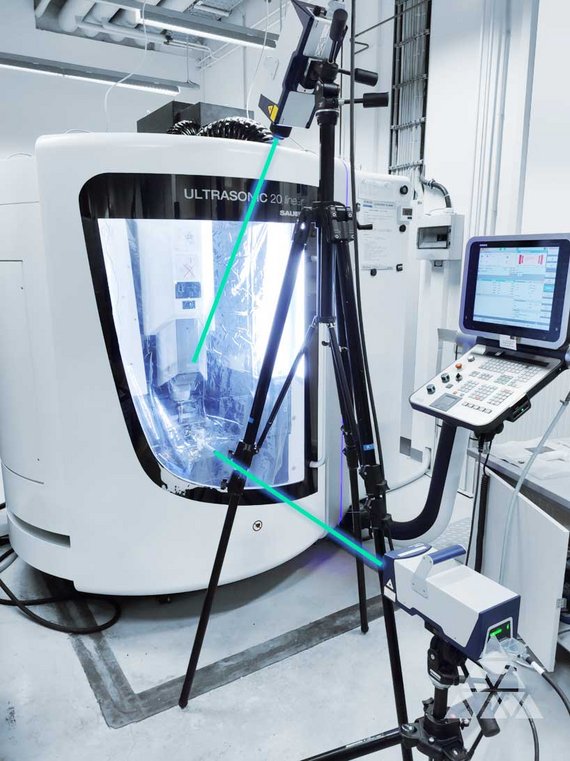
Im Maschinenbetrieb sind Schwingungsanalysen direkt während der Werkstückbearbeitung möglich. Mit berührungslos messenden Vibrometern kann auch das rotierende Werkzeug während des Betriebs von Maschinenkomponenten vermessen werden. Auch Messungen am zu bearbeitenden Werkstück im Betrieb sind rückwirkungsfrei möglich. Durch solche Betriebsschwingungsanalysen werden Effekte sichtbar, die im Maschinenstillstand unerkannt bleiben.
So führt die in der CNC-Maschine eingebaute Temperaturkompensation bspw. dazu, dass sich im Abstand von einer Sekunde Stufen in der Größenordnung von 1 µm auf der Oberfläche bilden. Der Abstand zweier Stufen ist durch die periodische Wiederholung der Temperaturkompensation an die Vorschubgeschwindigkeit des Werkzeugs gekoppelt. Daraus ergibt sich, wie vom KI Modell vorhergesagt, die wichtige Erkenntnis, dass die Temperaturkompensation der CNC-Maschine auch nachteilig sein kann und unter Umständen besser ausgeschaltet bleibt.
Anhand von Detailaufnahmen der Oberflächenstruktur konnte ein direkter Zusammenhang zwischen dem Abstand bzw. der Ortsfrequenz von Bearbeitungsspuren auf der resultierenden Werkstückoberfläche und den Schleifprozessparametern Drehzahl und Vorschub hergestellt werden.
Vorhersage der Oberflächengüte mittels Vibrometrie und KI
Die Zusammenführung der end-of-line Oberflächenmessung und der in-line Schwingungsmessdaten in einer gemeinsamen Frequenzdarstellung zeigt eine hohe Korrelation zwischen Maschinendynamik und resultierenden Oberflächenstrukturen.
Durch die Korrelation der optischen Schwingungsmessung mit der optischen Oberflächenmessung in Kombination mit einer KI konnte ein Verständnis für die Einflussgrößen der Schleifprozessparameter auf die resultierende Oberflächenqualität erarbeitet werden.
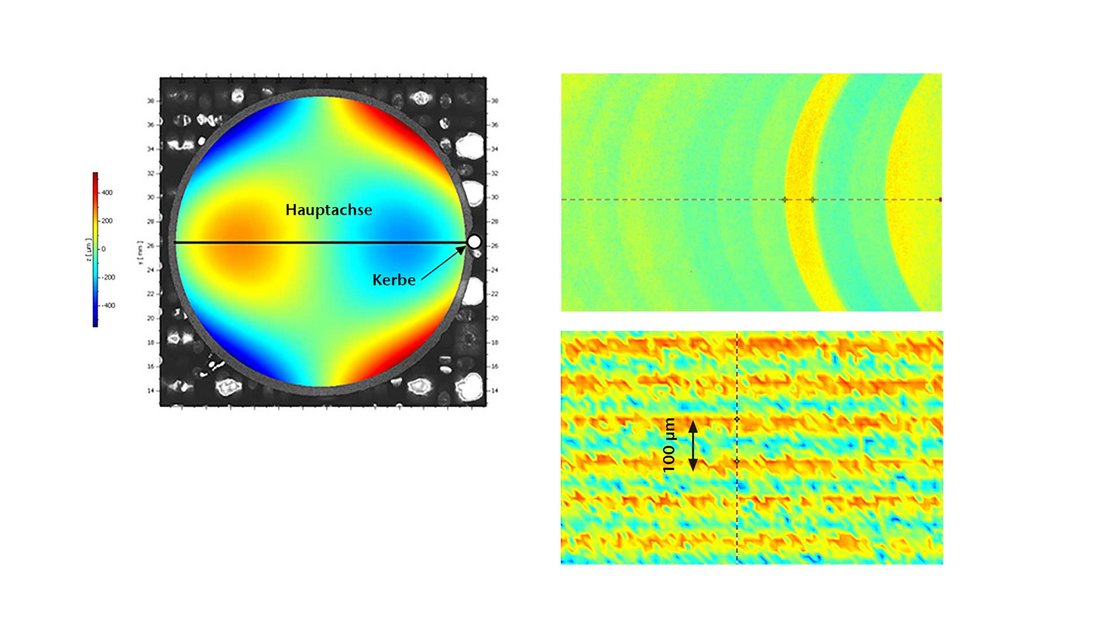
Bildnachweise: Soweit nachfolgend nicht anders aufgeführt bei den Autoren. Titelbild: KOMTHONG-APEC/shutterstock.com