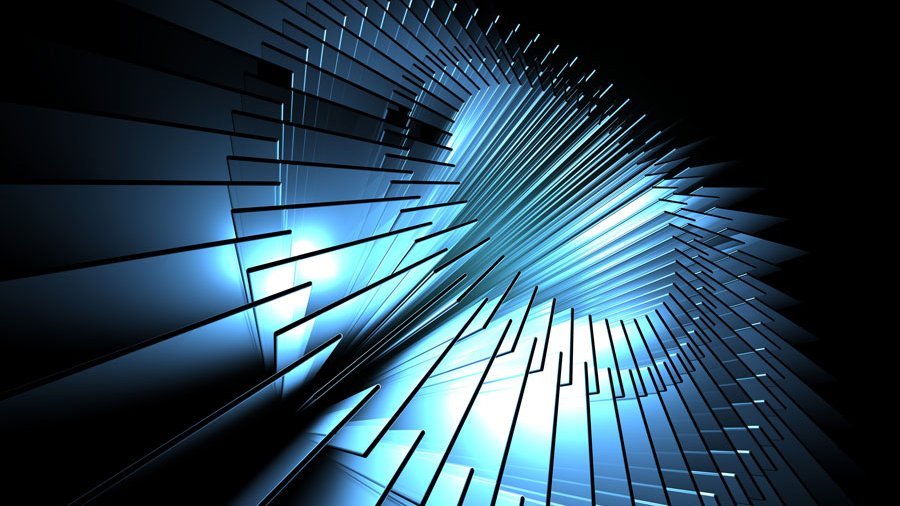
Fuel consumption of aircrafts is a hot topic in the current discussion about global climate change. An important factor is the design of the aircraft engine itself. In order to reduce weight and build more economic engines, the use of blade integrated disks (blisks) is getting more widespread. These components are milled from one single piece instead of being assembled like conventional parts.
Need for vibration tests and model correlation
Blisks reduce weight and complexity, but bring technical challenges. As they are made from one single piece, they show extremely low damping, leading to very sharp, pronounced vibration resonances. An ideal blisk is symmetric, meaning that all sectors have the same geometry and material properties. In such a case, the vibration modes show a symmetrical behavior as well, the vibration energy is distributed equally among all sectors.
Very small imperfections in the manufacturing process lead to mistuning of the resonances. If mistuning appears, the vibration energy might be concentrated in one or a few blades, leading to high vibration amplitudes. During operation, this could lead to higher stress and ultimately to an earlier failure of the component (high cycle fatigue).
To predict the real stresses under operation, detailed Finite Elements (FE) modelling is needed. As a first step, a FE model for a symmetric part needs to be validated by test. As a second step, it will then be adapted to account for the observed mistuning. Detailed FE correlation is therefore a crucial step and needs to be performed very accurately.
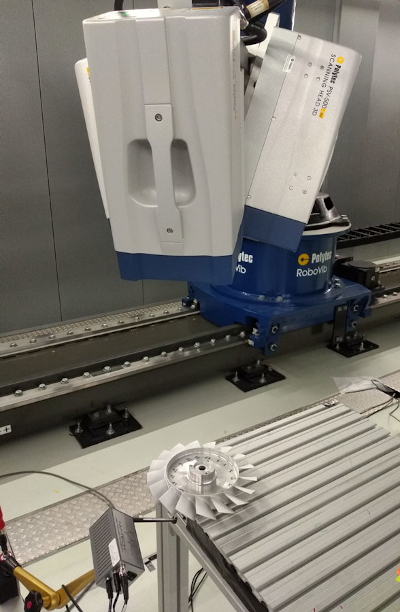
3D laser Doppler vibrometry for model correlation
Laser Doppler vibrometers measure the vibration behavior reliably in a non-contact manner over the entire needed frequency range. No mass loading or increased damping as for conventional contact sensors like accelerometers appears. This is a mandatory condition for an accurate and detailed model correlation. 3D Scanning Laser Doppler Vibrometers (3D SLDVs) furthermore yield the complete 3D deflection shapes for all frequencies in a simple and accurate way, leading to a full dataset that can easily be used for correlation with FE models.
A compressor blisk of 240 mm diameter, provided by the ITSM from the University of Stuttgart is studied. It is manufactured out of stainless steel and has been milled with high precision at a company specialized in the manufacturing of these parts. A high-resolution geometry scan showed only very slight geometrical deviations, in the order of 50 µm.
The blisk has been placed on three small rubber pads, to decouple the part from the environment, while minimizing the influence from the support. Broadband excitation up to 20 kHz is performed by a SAM 1 Scalable Automated Modal Hammer. The 3D SLDV, type PSV-500-3D Xtra, is using an infrared light source of 3 mW power, removing the need for elaborate surface preparation and still being eye-safe.
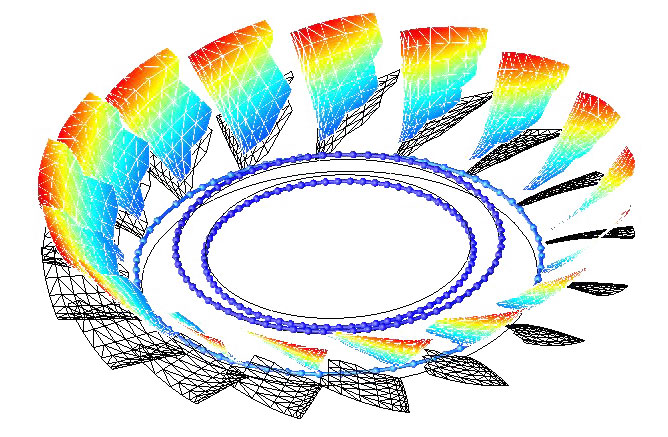
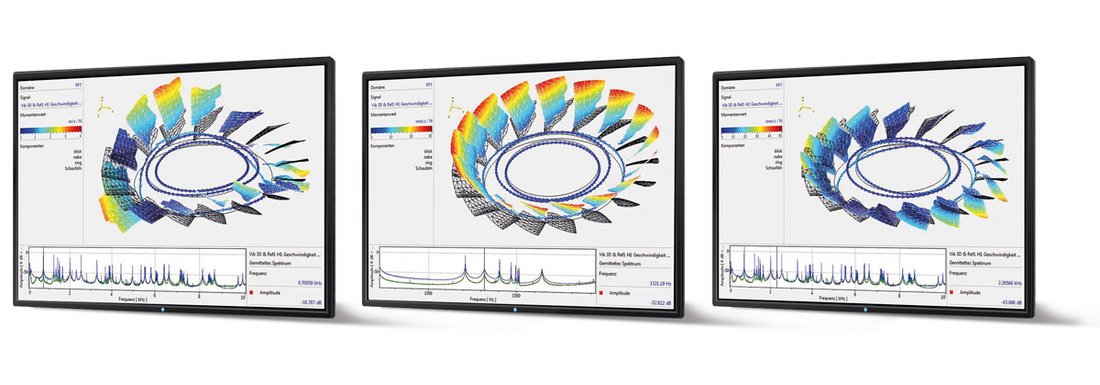
Results
Figure 3 shows the measured transfer function (FRF) spectrum, averaged over all scan points, figure 2 some example deflection shapes. Figure 4 exemplifies a frequency split of the double modes, characteristic for cyclic-symmetric structures, giving the first hint at a very slightmistuning of the blisk, an important parameter.
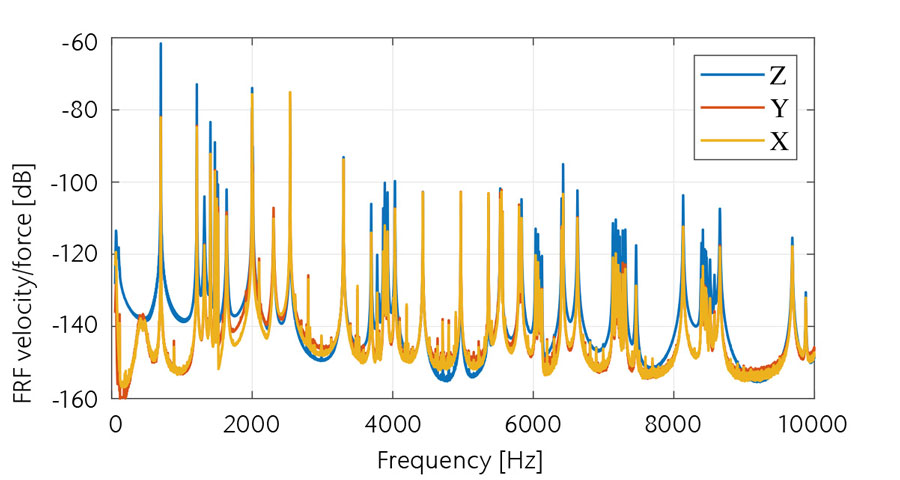
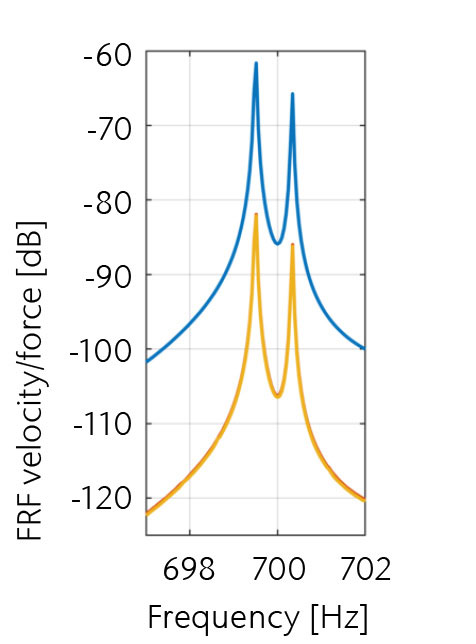
For further analysis and comparison with FE, the dataset is exported as a universal file and modal extraction is performed, using the modal analysis software package PolyWave. The modes of the first mode family so-obtained are then compared to the modes from FE simulation for a purely symmetrical structure.
Table 1 shows the frequencies from test and simulation, their differences and the damping ratio, obtained from the test. Data is shown for the first mode family, where all individual blades show the same first-bending-type deflection shape. The frequencies are in excellent agreement, indicating that the mistuning is small. Nevertheless, the slight split in the frequencies of the double modes (0.6 - 3 Hz, for center frequencies of about 1 - 2 kHz) shows that it is present.
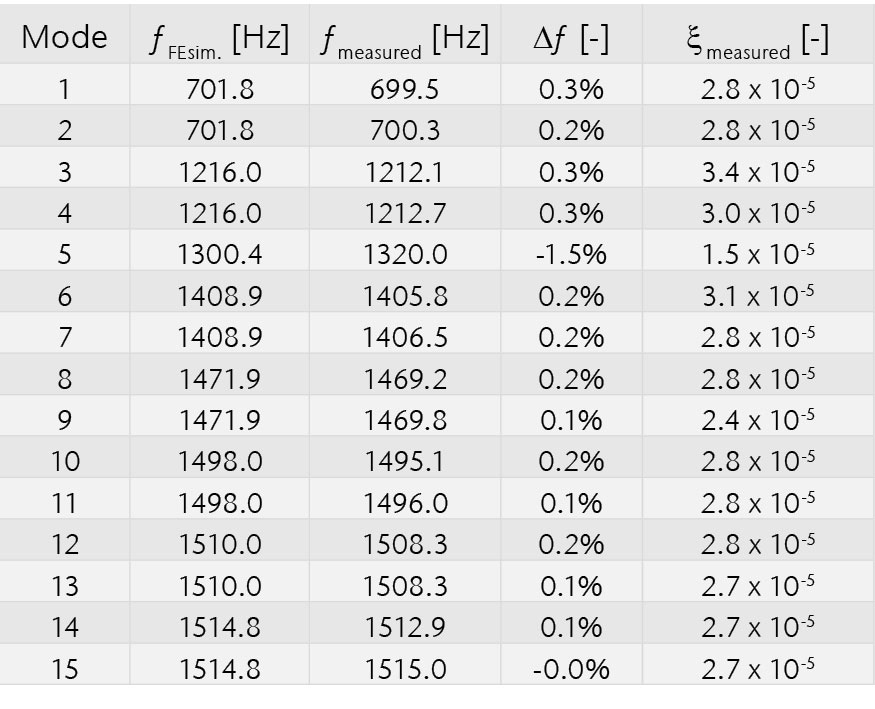
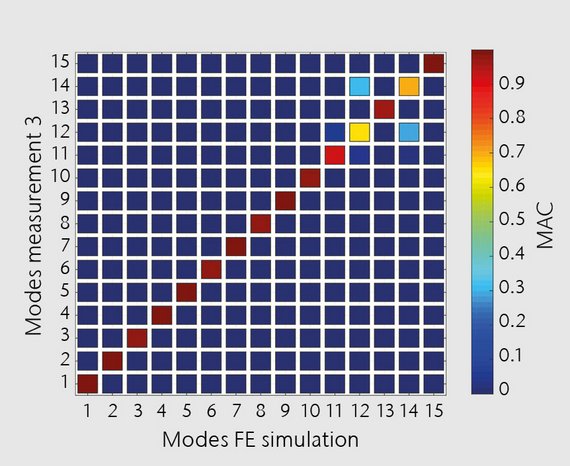
This is consolidated by comparing the mode shapes extracted from test with those from FE with a MAC analysis shown in figure 5.
As usual, MAC values close to 1 indicate high similarity of the mode shapes, smaller values indicate deviations in mode shape. While the lower order modes show excellent correlation, some of the higher order modes show lower MAC values.
A more detailed study (see references below) shows that these deviations in mode shapes can very well be explained by slight geometrical mistuning effects, which break the symmetry of the mode shapes by localizing the vibration amplitudes to a few blades more than to the others.
Conclusion and outlook
3D laser Doppler scanning vibrometry is an excellent method for acquiring high fidelity data from challenging objects like blisks. Modal extraction of the data using PolyWave enables a detailed correlation with FE modes. The results from simulation and test in general turn out to be very congruent, all relevant modes from simulation can clearly be detected and the agreement in terms of frequency is very good.
A detailed analysis of the data shows slight mistuning effects in the manufactured blisk, which was not captured by the FE model for the idealized of the CAD model. These mistuning effects can be detected by frequency splits of double modes and also by differences in the mode shapes of higher order modes, indicating localization effects of the vibration energy.
The results allow for an FE model update, that takes into account mistuning, which is mandatory for predicting the high cycle fatigue under real operating conditions. So far, the analysis has been limited to the modes of the first mode family of the blisk, but as data has been acquired up to 10 kHz, also higher mode families can be studied at the same level of detail.
References
Patric Buchwald et al.: Paper presented at the APVC conference in Sydney, Australia, Nov. 2019.
Images courtesy: Images courtesy of the authors unless otherwise specified. Cover image: ©jpa1999/iStock.com