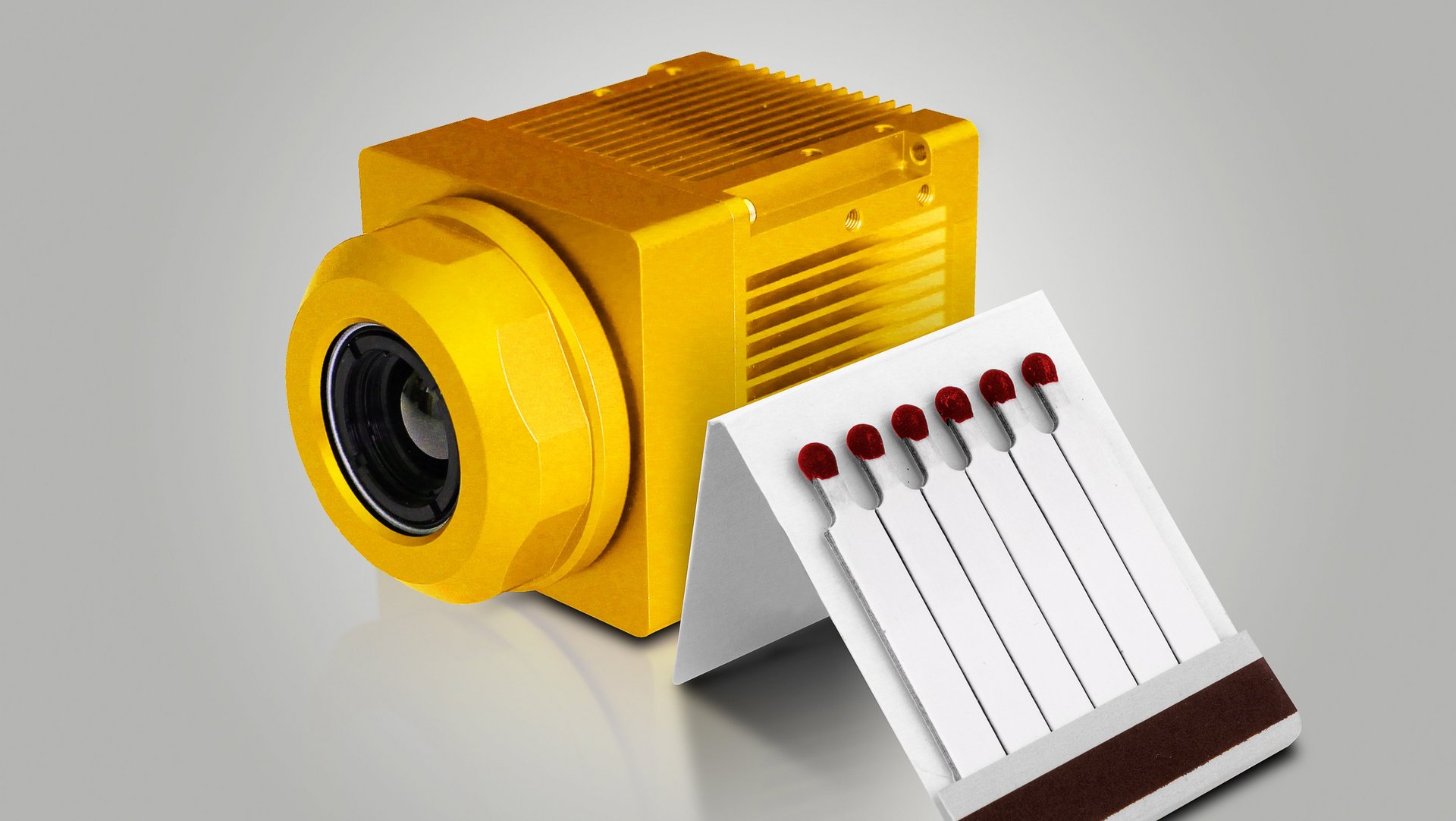
Thermographic methods, whose typical false colour images visualise temperatures, are suitable for many areas. Their possible uses in industry are particularly varied during the monitoring of temperature-dependent processes. In this context, not only are hot rolling, plastic welding or glass hardening typical examples, applications also exist in chemicals, petrochemicals, the energy sector and the automotive industry. Safety concepts can also be easier to implement when it is necessary to detect pockets of embers or other heat spots which could lead to explosions in critical environments, for example. Complete thermographic systems, consisting of smart, ATEX-approved thermal imaging cameras and the matching modular image processing software are now opening up interesting possibilities, as they can be adapted to completely different scenarios.
In the short-wave infra-red range (SWIR), many things can be seen that are not visible to the human eye. The examples range from the detection of pressure marks on fruit, to the inspection of grain, through to manufacturing defects on silicon wafers or solar cells. Polytec (see company info box) has been an experienced distributor of area and line scan cameras, line arrays, smart cams, video cameras and display devices for the short to long wavelength in infra-red for some time, including state-of-the-art InGaAs and micro-bolometer cameras. A practically-oriented thermography application needs much more than just a camera, however. The company, which is based in Waldbronn, Germany, therefore offers intelligent camera systems as a complete solution, including software and engineering, and supports the user with its know-how during the commissioning on site.
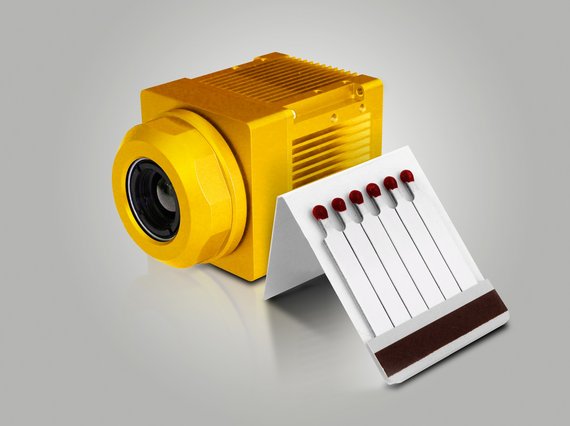
Intelligent camera plus adaptive software
As the “heart” of its complete thermographic solution, the Waldbronn company has chosen a thermographic camera from the German manufacturer AT - Automation Technology GmbH which was developed as an intelligent system especially for industrial use (image 1). It combines a radiometric calibrated thermal image sensor, a powerful processor, as well as several industrial interfaces in a compact, rugged IP67 enclosure. In cooperation with Polytec, a system solution has been developed that complies with the ATEX guidelines and is able to communicate directly with the process control system. It is configured to issue alarms at certain thresholds, for example, or to automatically switch between multiple inspection tasks as required.
For more extensive analyses of the camera signals, complex image processing options and a clear, detailed display, Polytec has also developed a powerful form of software in cooperation with the software experts at kernel concepts GmbH, which also impresses due to its modular structure. This means that the user only “sees” what they need for their application. This means simpler tasks can be realised as well as high-performance thermographic solutions for process monitoring and quality assurance through to Industry 4.0, as well as Deep Learning in temperature measurement technology. An example from the area of paper production shows how effectively the thermographic complete package can be integrated, including into existing systems structures.
Temperature monitoring to detect pockets of embers
An international company from the paper and forestry industry, makes toilet paper, household towels and industrial rolls at a manufacturing plant in Germany. The energy supply is provided by the company’s own coal-fired power plant. When transporting the coal to the power plant, the requirements of ex-zone 22 apply, as the dust present in the air could explode as a result of possible pockets of embers in the coal. Today, such embers can be detected reliably around the clock using intelligent thermal imaging cameras (image 2a and b).
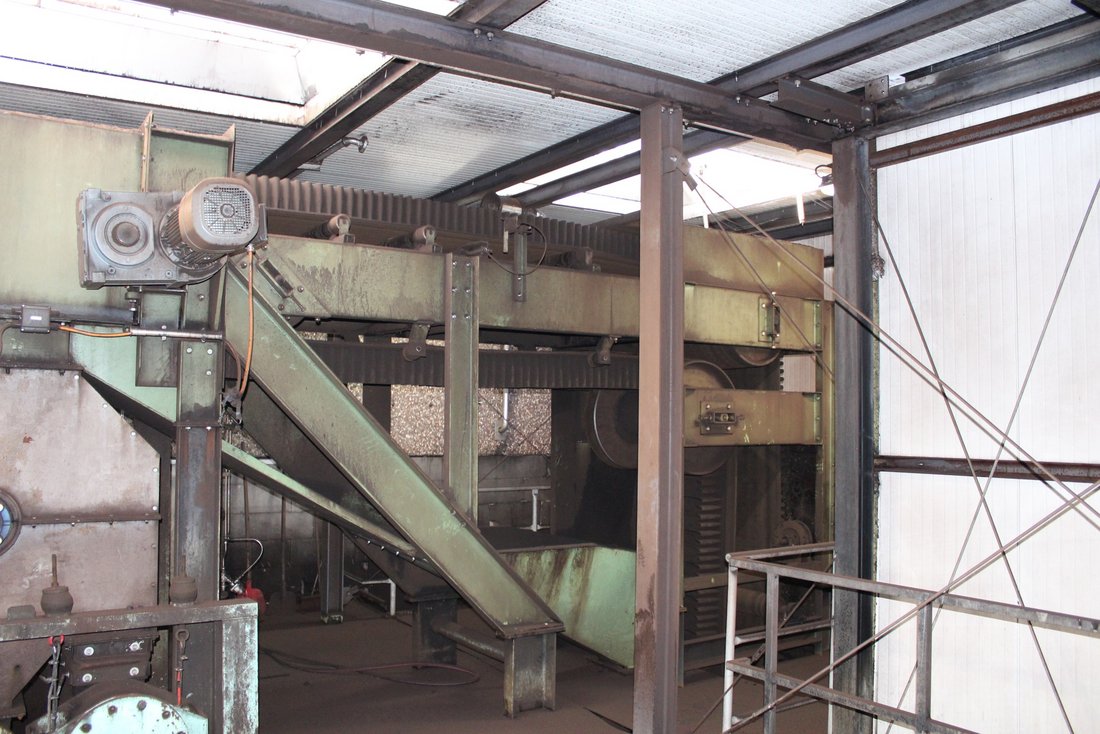
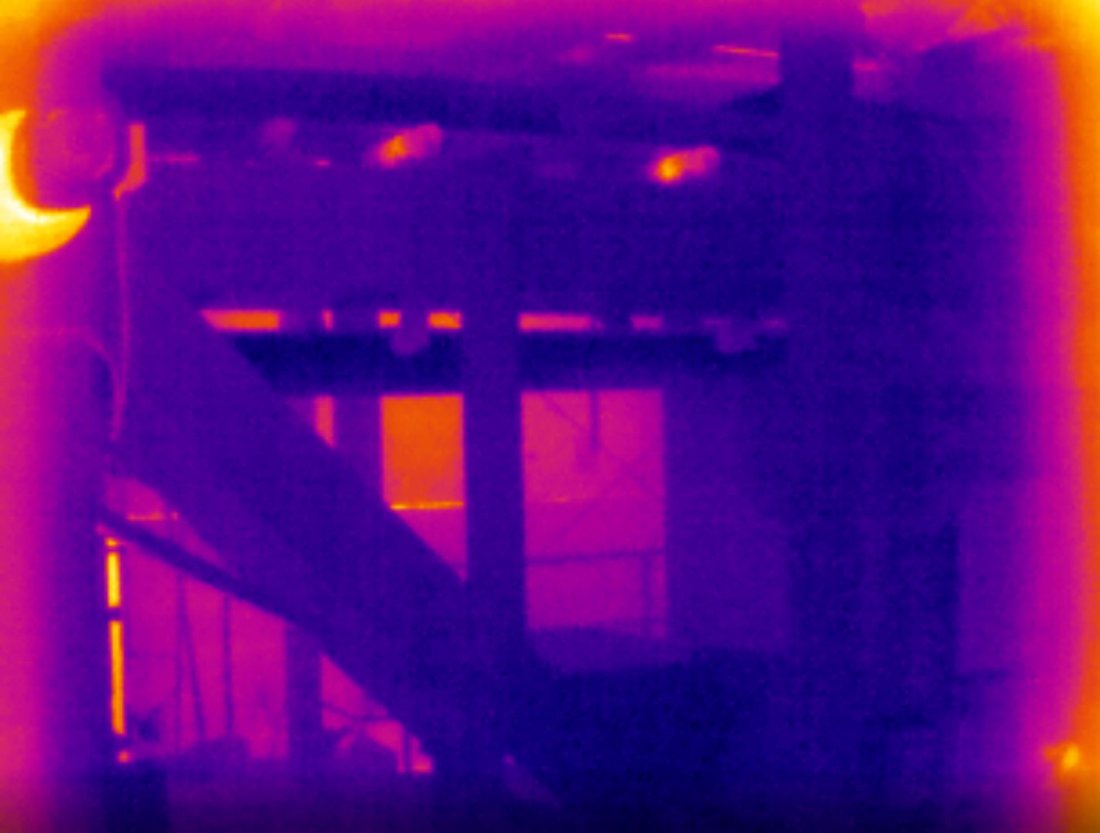
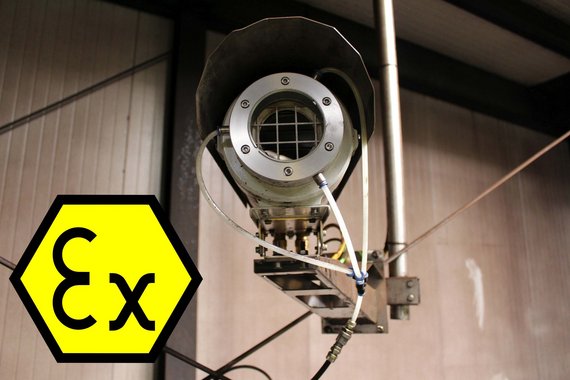
For this purpose, a total of four cameras are installed on the conveyor lines (image 3). These are housed in an explosion-proof enclosure due to the harsh environmental conditions and potentially explosive atmosphere; an integrated air purge also keeps the optics dust-free under adverse conditions. If the temperature in the flow increases, the cameras issue a warning message. Threshold values for the initial alarm and main alarm are stored in the systems and the cameras are connected to an embedded PC via a network, which makes the data available to the control room via MODBUS.
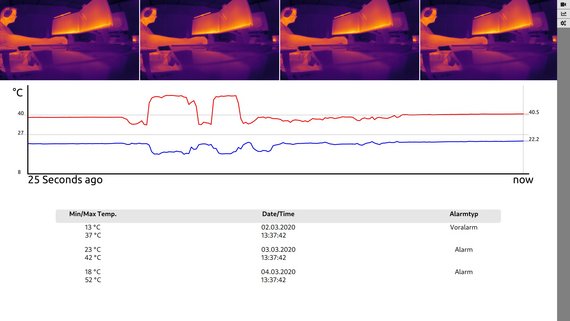
Here, all the live images from the cameras, including trend displays, can be seen on a monitor (image 4). Initial alarms, alarms and the operating data temporarily stored in the ring buffers of the cameras are archived in a data manager. If required, this data can be retrieved and displayed together with the images. For “fail-safe” operation in the safety-relevant monitoring system, the cameras also provide the corresponding signals and evaluations: an alternating signal as a heartbeat, the operating status and the humidity and temperature monitoring of the enclosure.
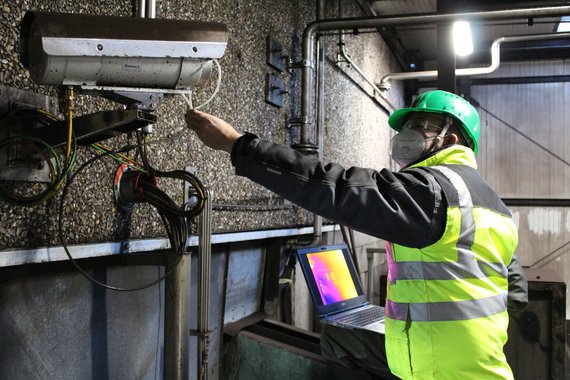
Technical support for the smooth commissioning
The commissioning of the system proceeded smoothly thanks to the good preparation (image 5). The mechanical installation and wiring to the control room were carried out by the plant operator together with a subcontractor. During this task and in the final set-up, the installation team were able to rely on the support of Polytec. In addition, the Waldbronn company took responsibility for all the adjustments during the start-up of the system, such as the definition of the monitoring range, the temperature thresholds and during the testing and simulation of the alarm management. The employees at the coal-fired power plant have been trained accordingly so that they can resolve any difficulties which can arise during the operations. However, Polytec is still available if required. Remote maintenance via remote software has also been planned in consultation with the user’s IT department.
There are many similar applications for the thermographic monitoring process with the intelligent thermal imaging cameras. All generally-flammable substances that are not stored inertly can form pockets of embers similar to coal, for instance. A typical example here is wood pellets or wood chips. However, the temperature of reactors in the process industry or other temperature-relevant processes can be monitored just as efficiently, in plastics processing, the steel industry or the automotive sector, for example. Monitoring temperatures using smart ATEX-approved complete solutions also makes sense in temperature-critical processes in battery production or the oil, gas and petrochemical industries.
Images courtesy: Images courtesy of Polytec GmbH unless otherwise specified.