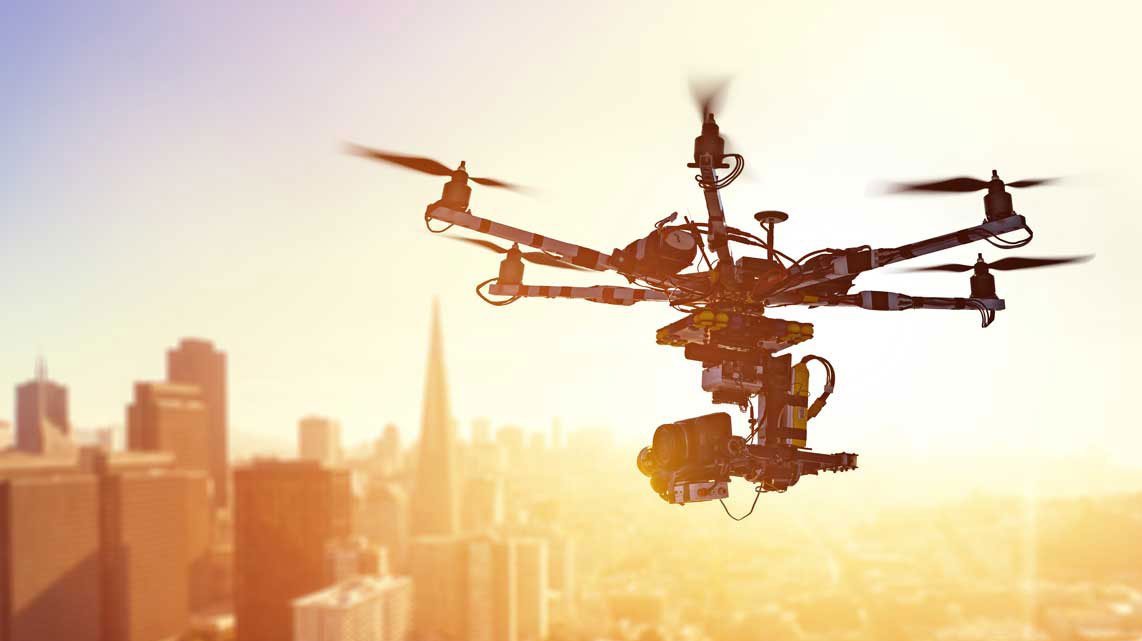
How manufacturers ensure reliability and quiet operation
The growth of the drone market is multi-faceted: growing concerns about national and border security drive the need for advanced aerial surveillance, package delivery services experience an increased demand for drone operations accelerated by the pandemic, hazardous environments in mining and construction open the eyes of many commercial enterprises to employ drones for mapping and inspection. Furthermore, the benefits of using drones is being discovered for new applications all the time as e.g. in real estate, in insurance claim situations, in the film industry, etc. The establishment of a proper regulatory framework by the FAA in the US has been crucial in pushing the commercial drone market in the US. Experts and market analysts are expecting drones to become a multibillion-dollar industry in the years to come.
Demands for the drone technology of tomorrow
The technological gap between military drones and recreational drones is being filled by commercial drones. Commercial drones need to meet strict requirements for reliability, safety and low noise emissions while presenting a cost-effective solution at the same time. Additionally, the following trends are emerging:
- Autonomous flying and longer flight times with no or minimal remote pilot control requiring advanced sensors and smart features
- Higher quality imaging making image stabilization mission-critical
- Compliance with noise regulations esp. since the high-pitch motor sound is unpleasant to the public
In all trends for more performance the importance of safety is always top priority. For the drone manufacturer, development cycles need to be efficient to meet price requirements and fast time-to-market demands.
Polytec helps designers to ensure reliable designs and quiet operation
Drone designers rely on accurate simulation models for optimizing the performance and reliability. Polytec’s non-contact vibration test equipment provides fast and accurate modal validation results allowing the design engineer to minimize the number of protype iterations while meeting industry standards and exceeding customer’s expectations. The motivations for controlling the level of in-flight vibrations are:
- Meeting regulatory requirements for acoustic noise emissions
- Ensuring consistent image quality of the on-board camera
- Increasing durability to avoid liability issues from damage and injuries
Vibrometers make modal testing possible on the entire drone structure as well as on a component level, no matter how small. More so, it is key to understanding the dynamic interaction between the individual components with each other. Wind and air turbulences are external excitation forces and influence the vibration forces exerted by the propellers and motors. If uncontrolled, critical resonances can easily be excited leading to excessive vibration levels, fatigue, and breakage.
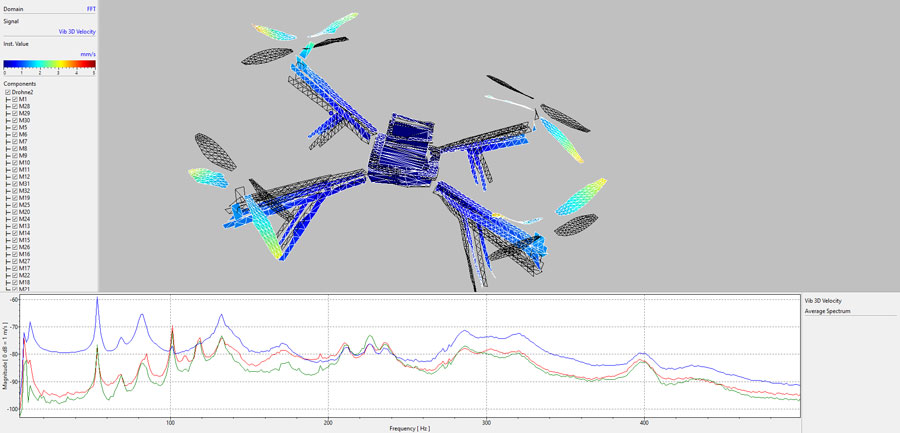
Figure 1 shows an example operational deflection shape taken on a drone body and stationary rotors at 53Hz. The movement of the structure is highlighted in color in contrast to its resting position indicated by the black hashed areas. The vibration data has been captured with a 3D scanning system. Using a robot-based system scans were taken from different sides and angles in an automated process with short measurement times. The graphs below the deflection shape are the average spectra in X, Y and Z direction of all the measurement points. As with all complex structures, there are always multiple resonance frequencies to consider.
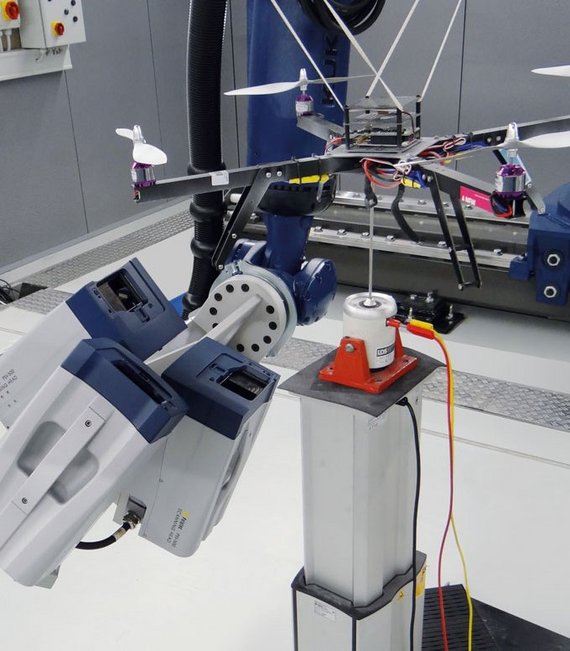
Modal tests like the one described above are used to update finite element simulation models with a given geometry mesh. The non-contact measurement approach makes high density measurement grids possible without any mass loading of the structure. Figure 2 shows the test setup. The drone is suspended on a set of rubber bands ensuring a free-free condition for the modal test. The shaker underneath excites the drone body with a controlled broadband vibration pattern. The 3D scanning vibrometer is mounted on a 6-axis robot allowing visual access from all sides under different angles. Three laser beams are scanning the drone surface synchronously capturing the vibration response at each measurement location on the grid from three separate angles. The vibration amplitudes are then internally transformed into orthogonal vibration vectors of the drone’s geometric coordinate system.
The dynamic behavior of propellers changes during rotation especially at high rpms as the centrifugal forces pull on the propeller blades. This is very difficult to simulate and real operational data is very beneficial. Therefore, operational deflection shapes of rotating structures, like fans and propellers, are typically captured by means of Polytec’s Derotator. The Derotator is an add-on to the scanning vibrometer that spins the laser beam synchronously to the propeller’s rotation by means of a rotating prism as can be seen in Figure 3. In the software a still-image is visible as the Derotator removes the rotating motion from the image. Upon axial alignment of the propeller and the prism the measurement process is equivalent to a test on a stationary object.
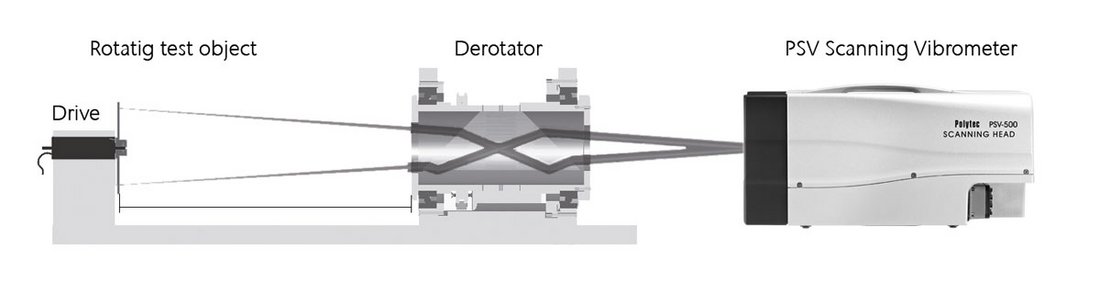
Figure 4 shows an example deflection shape of a rotating propeller. The image is blurry for any surrounding objects due to the rotation, however, it is well defined for the rotating object.
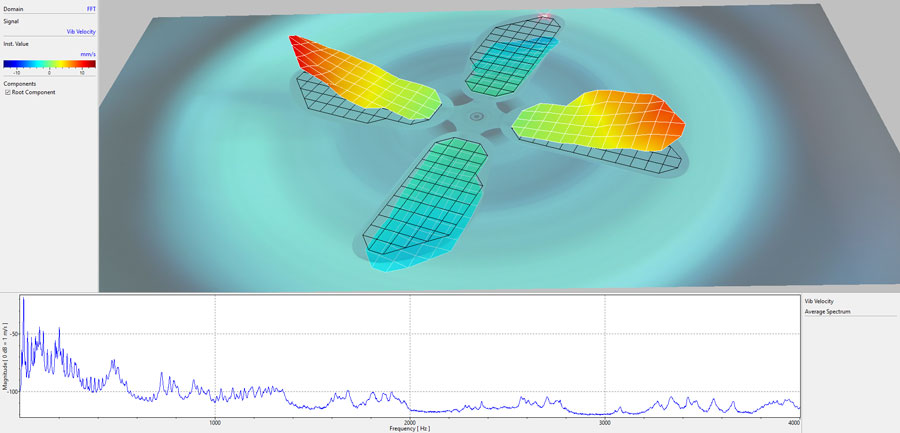
Polytec’s enabling technology
Polytec vibrometers are based on a point-and-shoot approach using a laser beam. The interferometer inside the head captures the reflected light and analyzes the Doppler shift, which is directly proportional to the object’s vibration. One very important benefit of the non-contact technology is that no mass-loading is distorting the result. The laser beam can be repositioned easily either by manipulating the vibrometer head or by means of steering mirrors. 100s of points can be measured with little effort as the software allows the user to draw or import a pre-defined grid of measurement points. Laser Doppler vibrometers are highly accurate as the laser source is stable in wavelength and are used in calibration labs for primary and secondary calibration of contact transducers such as accelerometers. The latest vibrometer technology, called QTec, assures clean, high resolution time traces without the need of any surface treatment or excessive averaging.
Conclusion
With the drone industry embarking on a growing trend of new proportions, Polytec offers the necessary tools for the design and test engineers to meet the ever-growing demands for performance, reliability, and safety. The buzz about drones is increasing while sound levels are being kept in check for the comfort of the public.
Polytec’s technical experts are here for you to consult on your measurement challenges. Testing services, rentals and flexible leasing options are available. Vibrometers come in different flavors to accommodate a variety of test setups: from very large structures down to microstructures, at one single location and across high-density scan grids, in 1D and 3D, linear as well as rotational dynamics, stand-alone and integrated in a fully automated robot system.
Images courtesy of Polytec GmbH unless otherwise specified. Cover image: ©Alex Yuzhakov/shutterstock.com