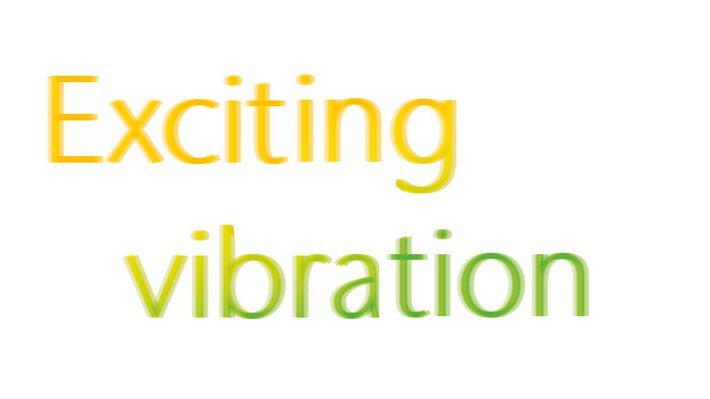
The excitation of a multi-cantilever MEMS structure by molecular Brownian motion is investigated by ultra-high resolution optical vibrometry. This novel approach to testing enables applications such as the calibration of AFM tips.
MEMS devices, designed as sensors or actuators, are essential components in today’s consumer electronics, automobiles, aircraft, and medical devices and instruments. The measurement and characterization of in-situ ambient excitation of a MEMS device is critical to developing a functional prototype as well as to releasing a production device with proper calibration and quality control.
In the first phase of the development process, calculations from digital models are used to optimize the MEMS performance and to minimize parasitic or offset effects. In the second phase, these optimizations are verified and the general specifications of the MEMS device are measured on prototype samples. In this article, a MEMS multi-cantilever structure is characterized using a Polytec MSA Micro System Analyzer (figure 1). The resulting measurements characterize both the mechanical vibration properties as well as the surface topography of the device.
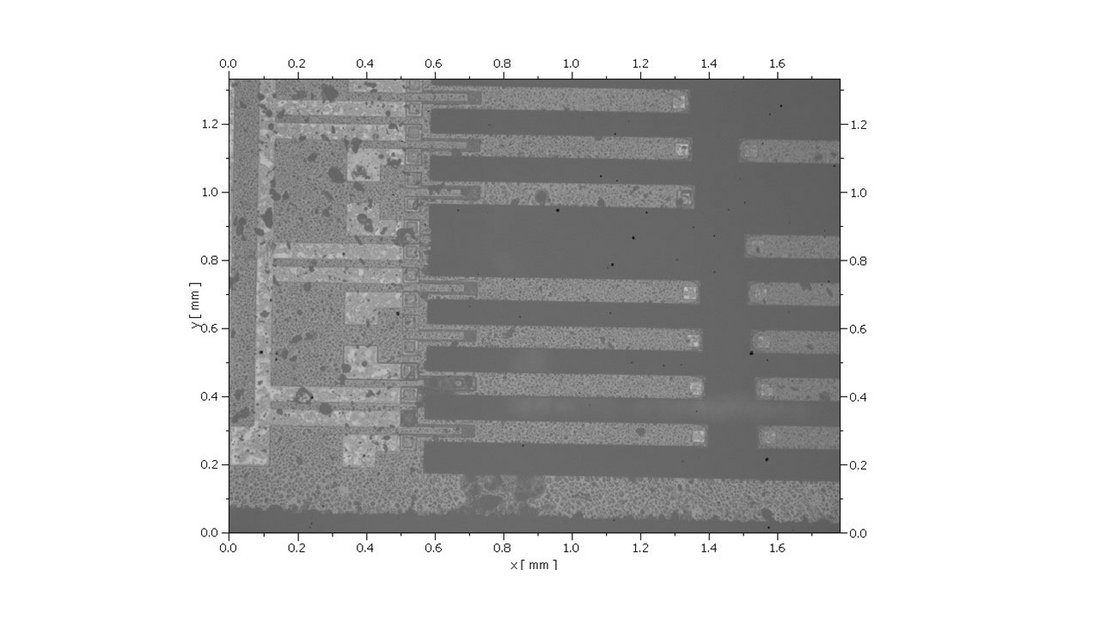
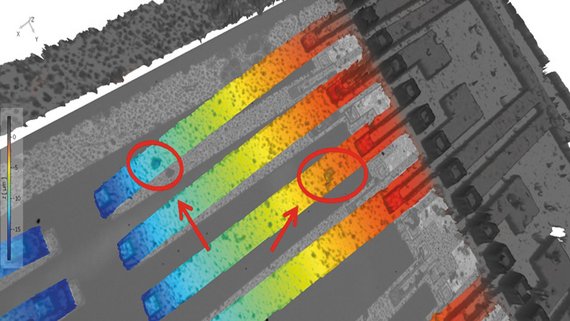
The Micro System Analyzer combines three measuring techniques into one instrument: laser Doppler vibrometry for out-of-plane vibration measurement, stroboscopic video microscopy for in-plane analysis and white-light interferometry for surface topography measurement (figure 2).
Measurement of ambient-excited vibrations
The vibrational testing was performed in two phases: first, a measurement with an active excitation by a piezo actuator that is glued to the MEMS mount; second, a measurement with only ambient excitation.
For the active excitation, the signal of the built-in generator is applied to the piezo actuator and is also used as phase reference. For the ambient excitation, a second fiber optic vibrometer is used as a phase reference by coupling into the optical path and reflecting from the cantilever base.
Measurement data
The active excitation leads to an operational deflection shape (ODS) and a corresponding average spectrum over all grid points (figure 3). To compare the amplitudes and deflection shapes of the active and ambient excitations, one of the most prominent resonance peaks from the active frequency spectrum was arbitrarily picked. Due to the use of a phase reference, the motion of all individual grid points can be animated with relative phases. Then the point with the highest amplitude was selected and its single-point spectrum examined.
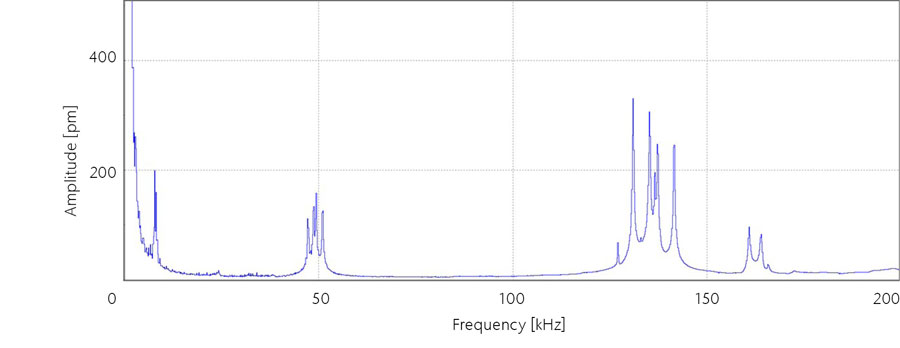
Subsequently, the same frequency was selected in the spectrum for the ambient excited case. In the same manner as for the active excitation, the point with the highest amplitude is chosen and its spectrum is displayed. For each of the four individual cantilevers, a frequency was picked, then an ODS was displayed for an active as well as an ambient excited cantilever and compared to each other. In each case, the frequencies associated with the second bending mode were picked.
In figure 4, the deflection shape of one self-excited cantilever at 130.9 kHz is shown. The passive excitation is due to the statistical Brownian motion inherent in the environment.
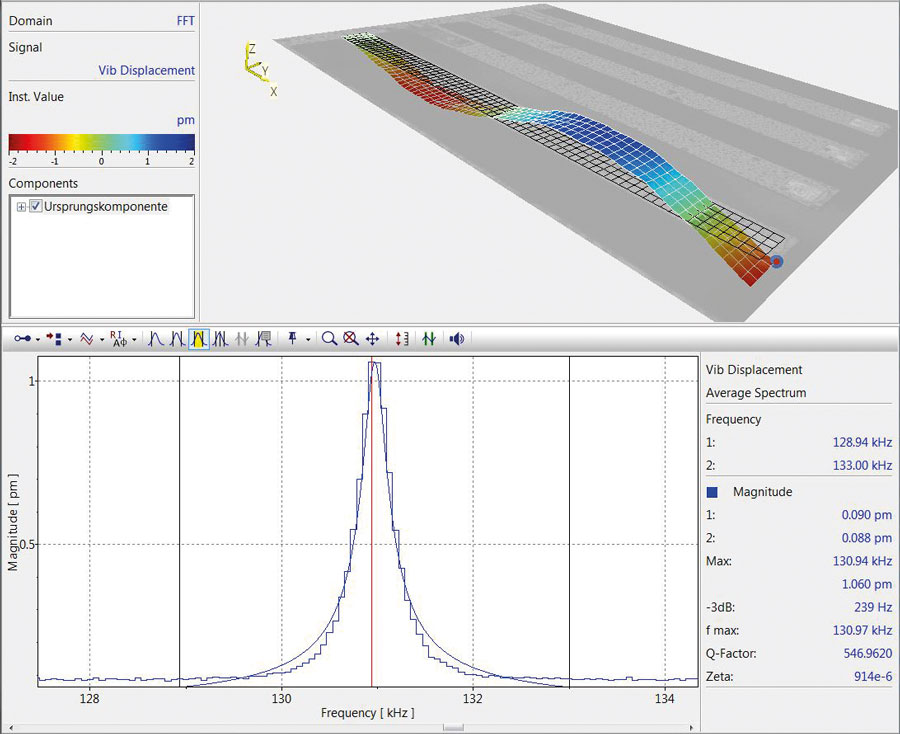
In table 1, a comparison of the active versus ambient excitation is shown. For the case of the ambient excitation, the amplitudes of the examined resonance frequencies were approximately three orders of magnitude lower. Nonetheless, the signal quality was still sufficient enough to effectively determine the amplitudes and deflection shapes (without active excitation).

Interpretation and outlook
The non-contact optical measurement of the ambient excited vibrational behavior of a MEMS cantilever structure was demonstrated under in-situ environmental (room) conditions. The capability of a laser Doppler vibrometer to precisely measure even the smallest vibrations of microscopic cantilevers, excited only by ambient Brownian motion, was demonstrated. This impressive result may enable many interesting applications such as new calibration techniques for AFM tips.
This ambient excitation method combined with laser Doppler vibrometry can be used to calibrate AFM cantilevers without handling or touching the tip to a surface. Both flexural and torsional spring constants can be measured accurately with this method. Compared to conventional AFM spring constant calibration methods, which are typically done inside the instrument, this approach avoids the risks of damaging the tip.
The high sensitivity, accuracy and non-contact nature of laser Doppler vibrometry makes it the preferred method for microscope-based vibration analysis in laboratories and for production applications such as the calibration of delicate, low mass structures and devices.
Images courtesy: Images courtesy of the authors unless otherwise specified.