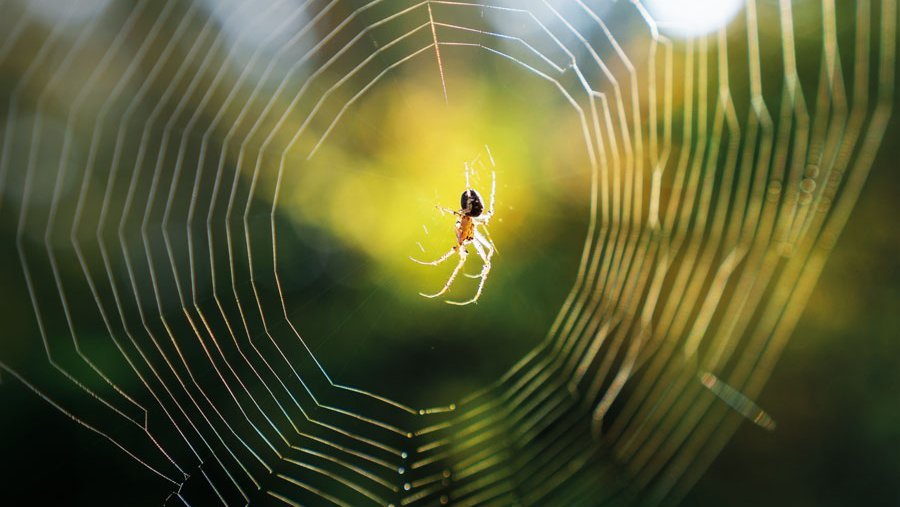
Spider webs are naturally occurring structures with amazing and very distinctive architecture, mechanics and dynamics. A typical web consists of two major types of silk threads, described structurally as radial and spiral, combined with their intersecting junctions on the web. The functional features of the spider web are resistance to wind induced vibration and to the high energy impact of the flying prey. Thus, to predict the vibration damping response of a complete spider web structure, the damping properties of its constituent silk threads were measured through in situ experiments on spider webs formed in the jungle.
In this experiment, a portable laser vibrometer from Polytec was used to measure the damping characteristics of very lightweight spider silk threads. For these structures, non-contact vibration sensors like the new VibroGo from Polytec are essential as the thread structure is unable to bear the load of conventional sensors such as contact accelerometers and strain gauges.
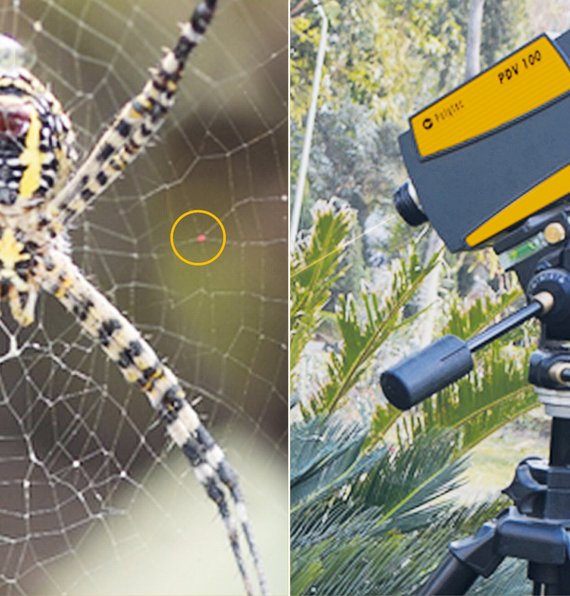
The experiment
The laser vibrometer and accessories were carried through the jungle to the site of the spider web. The experiment was setup as shown in figure 1. The time response of the silk threads was measured by the laser vibrometer after a gentle excitation using the impact of a gentle, manual air breeze, similar to the natural wind. The vibration damping was measured from this time response using the logarithmic decrement method.
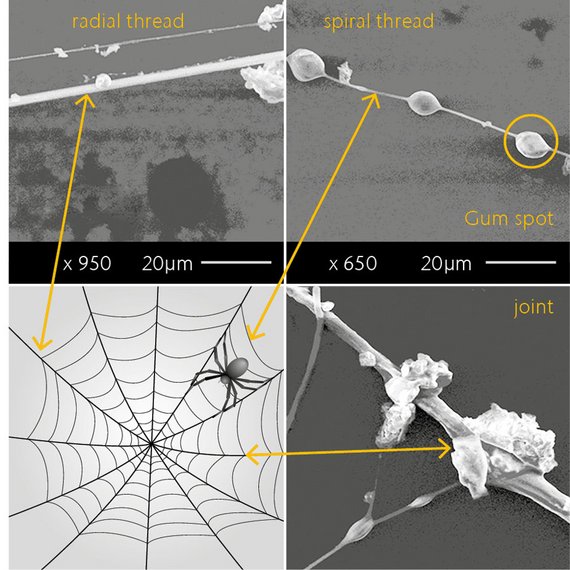
(Copyright 2017, with permission from Elsevier)
Results
The advantage of in situ experimentation is that the spider silk threads exist with a naturally occurring tension common to the environment; in addition, the web is supported from naturally occurring web anchorage which plays a major role in the structural integrity and prey capture performance of the web. The components that constitute the spider web and their corresponding scanning electron micrographs are exhibited in figure 2.
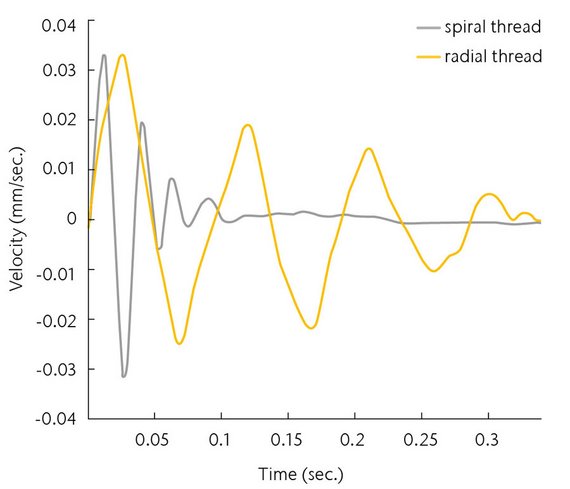
The laser beam was focused onto different locations of the web to sample both spiral and radial silk threads (see figure 1). After stimulation, the time response of both threads is acquired by the vibrometer and plotted in figure 3. When analyzed, the spiral thread’s temporal response has a significantly faster decay (shorter decay time) as compared to the radial thread.
Calculated from the measured time response at several different locations on the web, the average natural frequency and damping ratio (ζ) of both silk threads is tabulated in table 1. The spiral thread has a higher damping ratio and natural frequency. In this experiment, a low frequency excitation was applied to both radial and spiral threads through the impact of a gentle, manual air breeze. At low frequency excitation, only structural damping is taken into account, removing the effect of external damping (aerodynamic damping) and the effect of support related energy loses.

The radial threads are the vital structural component of the web since they keep the web intact under windy and stormy conditions as well as during prey impact. The radial threads also play the prime role in dissipating the imparted kinetic energy into the web.
The spiral threads, which have the high damping ratio and flexibility, instantly react to the imparted energy by spreading it into the radial threads. In this fashion, spider webs can survive and function in nature under changing environments.
Conclusions and outlook
In this study, the vibration damping of a spider web has been investigated utilizing a laser vibrometer, providing insight into a natural phenomenon that provides for the survival of the web in the jungle. The in situ vibration damping measurement reveals that the spiral silk threads have high vibration damping properties which instantaneously distribute the induced excitation into the radial silk threads.
The radial silk threads are the major building blocks of the spider web, preserving its structural integrity and preventing its failure by dissipating the imparted energy.
Images courtesy: Images courtesy of the authors unless otherwise specified. Cover image: ©wlad074/fotolia.com