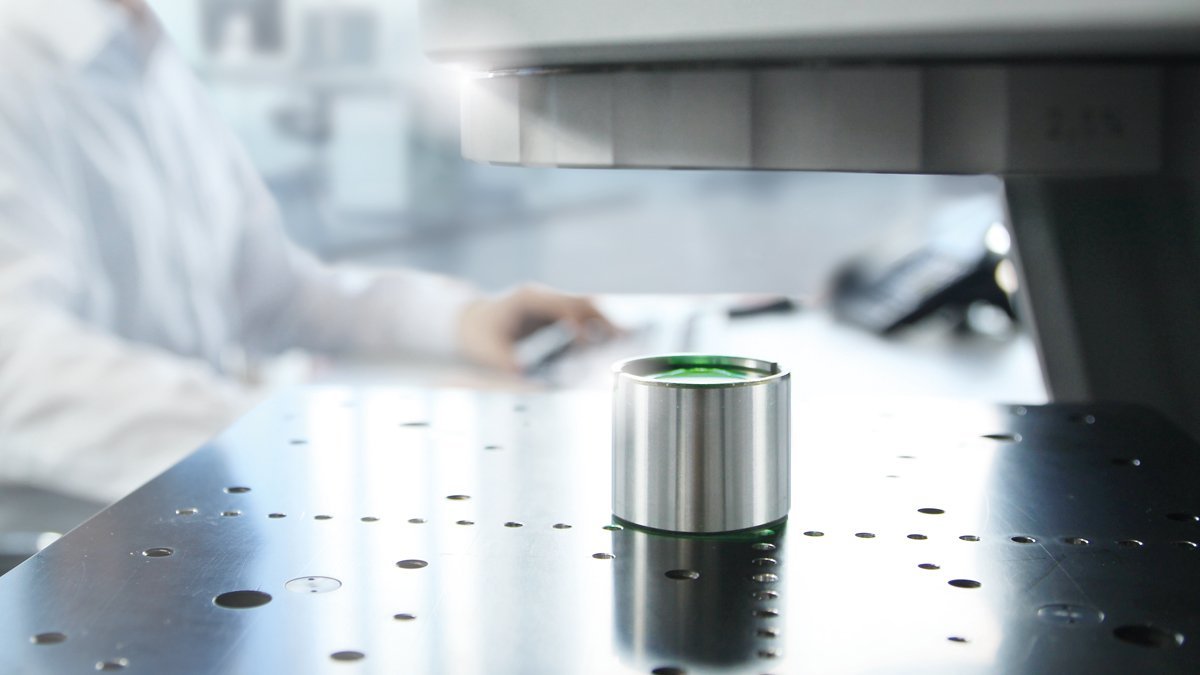
For applications where tactile surface measurement techniques have shortcomings, non-contact optical instruments have been developed to overcome these shortcomings. Especially with the development of computing capability, these methods provide surface information quickly and with high resolution.
Surface measurement techniques like chromatic confocal probing, white-light interferometry, focus-variation or confocal methods are the most common examples. Every technique has its pros and cons.
Chromatic confocale probing
As an optical method, chromatic confocal probing is most similar to stylus profilers. Surface data is acquired by scanning a point sensor with the help of a laterally translated stage and, as with tactile methods, the length of the scanned profile is only limited by the displacement of the stage. Such a configuration allows for tracing complex shapes and even circular profiles can be measured. It is limited for time sensitive areal measurements though, but it comes without any vertical scanning unit, which makes this technology completely static.
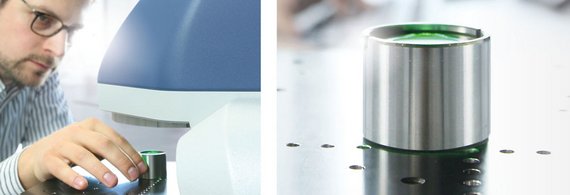
Confocal microscopy
Surface information by confocal microscopy is generated by acquisition of sequential confocal images through the depth of focus of the objectives. Even the numerical aperture of those objectives show advantages in some cases. The vertical resolution depends on the selected objectives. In other words metrological performance changes with the magnification/field of view of the objective. Objectives with higher numerical aperture can reduce the noise, but due to their small measurement fields, in most cases, a combination of multiple fields (stitching) is required, which takes additional time. On the other hand objectives with lower magnification have comparably larger measurement area but suffer from poorer vertical resolution and reduced slope acceptance which means surfaces with localized steepness will prove difficult to measure.
Focus variation
Focus variation uses the small focus depth of the optics to gather information from a surface, illuminating the area with modulated white-light and detecting the reflected light from the probe. While the distance between probe and objective constantly changes, the data is acquired. Depending on the sample topography, different sections of the probe are displayed on a digital sensor. For each position of the object, the focus is calculated anew.
The focus variation technique provides images with color but the vertical resolution is limited in comparison to the confocal and white-light interferometry techniques. And similar to confocal techniques, the vertical metrological performance of focus variation systems also depends on the chosen objective. In some cases, there is also a need to enhance textures on the workpiece to provide enough light for a robust measurements.
White-light interferometry
Although the numerical aperture of the objectives is limited, white-light interferometry provides high vertical resolving power. Moreover vertical resolution is independent of measurement field (field of view). Therefore even larger surfaces can be measured with nanometer vertical resolution. Similar to the other optical techniques, the lateral resolution is determined by the objective magnification.
In summary, it can be stated that every technique has its own limitations and strengths. However, in some applications, the user cannot compromise and needs some special solutions. This is where Polytec’s modular and multi-sensor concept for surface metrology shows its full potential.
Multi-sensor applications
In several applications, it is required to characterize surfaces with measurements like distance, width, height, form, surface texture, roughness, volume or film thickness. And the information about the quality of large surfaces (in the sense of micro- and nano metrology), which demands large measurement ranges (mm2 to cm2), can only be assessed by combining measurements on nano- and micrometer scales.
For such applications, measurement tools with multi-sensor capability provide more flexibility. Especially for the characterization of sealing surfaces, concepts with different measurement capabilities are required. Typically those applications require the measurement of form deviation on larger surfaces in mm range and at the same time evaluation of roughness with nanometer resolution. If the form deviation is out of tolerance, the required contact between different surfaces cannot be achieved. Even with a perfect surface finish, there would be leakages due to the empty volume in contact regions. If the form deviation is within tolerance, roughness of the contact surfaces is the second important factor to achieve the required sealing performance. In terms of surface metrology, a system which enables the measurement of form deviation on large surfaces and the characterization of roughness on long profiles will be the right solution.
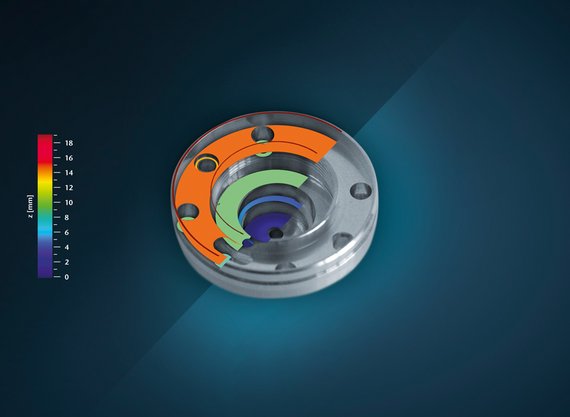
White-light interferometry combined with chromatic confocal probing
The vertical resolution of white-light interferometers is independent from the objective magnification, thereby resolving even large surfaces in a very short time. Whereas, other techniques would require objectives with high magnification. Polytec’s TopMap Pro.Surf is a white-light interferometer specially designed for large area measurement. The measurement volume (without stitching) of 30 x 40 x 70 mm3 (X x Y x Z) can be acquired with a vertical resolution in nanometer range and at the same time an appropriate lateral resolution.
For the applications in which high lateral resolution is required, the multi-sensor concept integrated with chromatic confocal probing is available. As an example, after having characterized the form deviation on the whole surface with the white-light interferometer, additional measurements with the chromatic confocal sensor can be performed to evaluate roughness. Similar to stylus measurements, the position, length and the shape of the profile can be chosen by the user. TopMap Pro.Surf+, the newest member of Polytec’s surface metrology family, makes it possible to measure the whole area of 228 mm x 221 mm for the application where form deviation and roughness is required simultaneously.
Conclusion
As manufacturing technologies continue to develop, there is a pressing demand to understand surfaces in more detail, both in the lab and on the production floor. Identifying a single superior measurement technique to fulfill all requirements is not possible. Depending on the interaction with the surface, regardless of optical or tactile method, every technique has its own advantages and disadvantages. Therefore, new multi-sensor concepts combining different techniques are the best answer to cope with the wide range of surface metrology applications.
Images courtesy: Images courtesy of the authors unless otherwise specified.