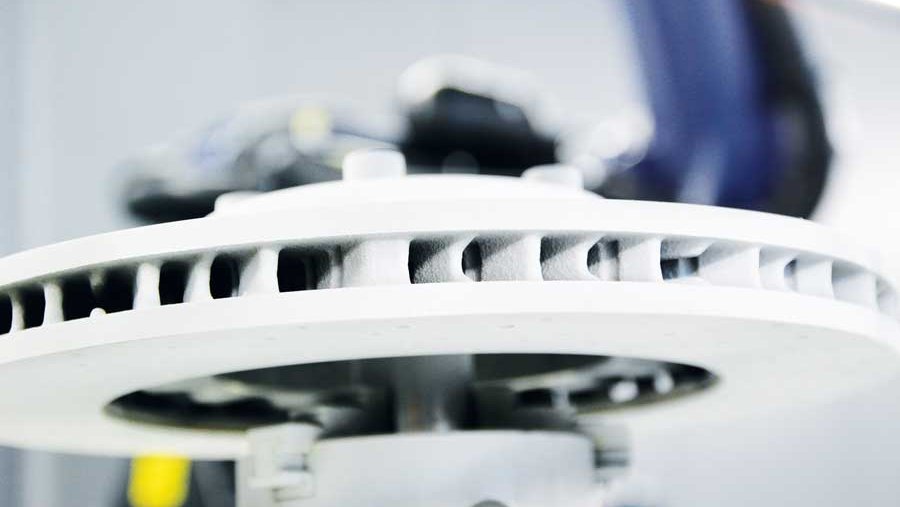
仿真模型的验证是激光测振仪的重要应用领域之一。为此,先将有限元模型的几何数据导入至测量系统的软件中,由系统内置的校准系统完成模型与实物之间的校准,导入的样品几何数据与其实际的几何数据之间的偏差,都将由软件内置的形貌测试程序来进行修正并更新至模型中,这种方法精确度高,还能节省大量时间。
与需要在被测结构上粘贴大量加速度计的传统方法相比,激光测振仪有诸多优点。例如,在汽车的有限元模型验证测试中,若使用传统方法,需要将大约40到400个传感器安装固定在精确计算的位置上,且三个维度上的位置都需保证精准。在此过程中,必须确定欧拉角,方可得到曲面上的传感器在被测物坐标系下的测量方向。
然而,传感器的安装和调整不仅需要耗费大量人力物力,它还会增加测试结果发生误差的几率,因为哪怕是最轻微的传感器定位或校准误差都会造成测试结果发生偏差。与此同时,贴片式传感器还存在附加质量影响,这个不容忽视。此外,受被测结构的尺寸限制,传感器的数量也不可能按需无限增加。
相比之下,扫描式激光测振仪使用激光作为探测手段,不存在任何附加质量影响,而且理论上,测量点数总是能满足实际需求;可直接将仿真模型的有限元网格或CAD图的几何数据导入至测量系统软件中,再使用软件内置的定位校准程序对其坐标位置进行修正,通过这种方式获得的测量结果更精确,更有意义,而且测试所需时间也大为减少,尤其当把扫描式激光测振仪安装在机器人系统上进行全自动测试时(如图1所示),这种优势就更为显著。基于机器人的RoboVib®测振站具有很多优质,以下实例就是最好的证明。
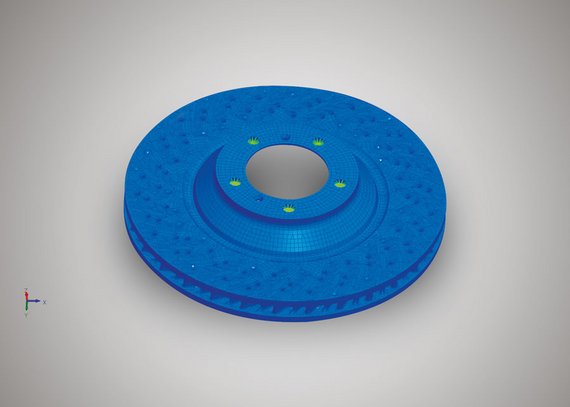
几小时内完成测试准备
在进行制动盘的模态测试前,将制动盘的有限元模型导入至PSV软件,该模型大约有15万个节点(如图2所示)。从网格中选出四个具有代表性的点进行定位校准,以便于软件计算出各点坐标,完成这一步需要将三束激光的交点依次移动到这四个点所在位置,存储相应的机械臂位置,并将有限元网格中的相应坐标分配到这些位置上。
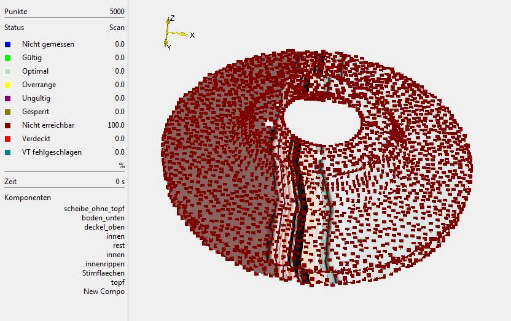
然后将导入的FE网格粗化到5000个测点,15万个测点并非不可,但测试耗时较久,(如图3所示)。而且,即使为获取最复杂的振动模态,也不需要像FE模型那么高的空间分辨率。为便于随后的对比验证,在粗化过程中对于测点我们只删除而不移动。剩下的5000个点还是在它们原来的位置,编号也不更改。
接下来, 编程确定机器人位置约为20个,通过扫描头内置的摆镜完成制动盘整个表面的振动测量。参考点的确定、机器人的位置编程及程序的试运行只需一个工作日。到此,整个测量系统已经准备就绪。整个测试过程无需专人看守,因为RoboVib测试系统可以自动完成整个模态测试工作。它甚至能通宵工作而不占用工作时间。
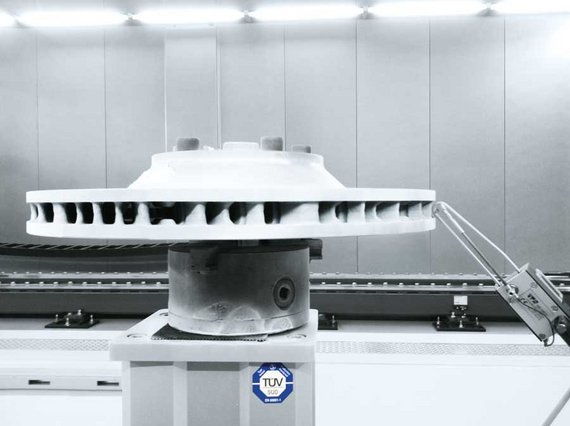
复杂振型的细节展示
本次试验中,我们使用锤击法,通过自动力锤为制动盘提供激励,力锤以一定角度敲击制动盘,尽可能激出多重模态(如图4a所示)。相比电动激振器,力锤能避免电阻式传感器的不良影响。同时,它能激发出远高于本试验所需的频率。
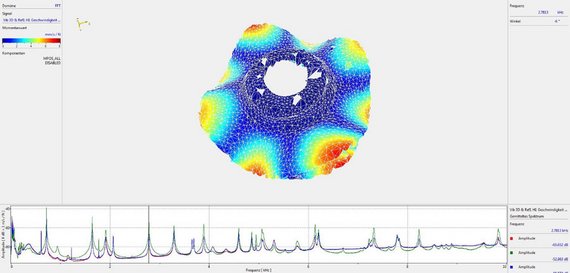
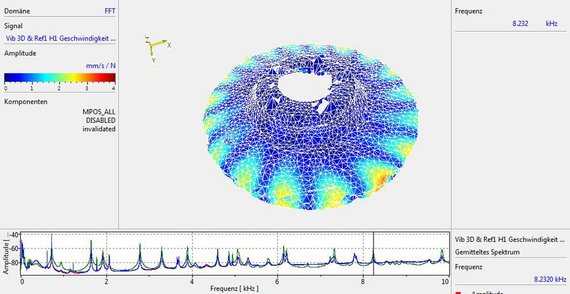
本次试验的评估频率高达10kHz。试验结果表明,我们完全可以获取结构在高频下的复杂振型细节(如图4b所示)。由于是3D测量,系统获取的是三维振动数据。测试数据可导出为通用文件格式,并通过FEM工具进行模态参数提取。
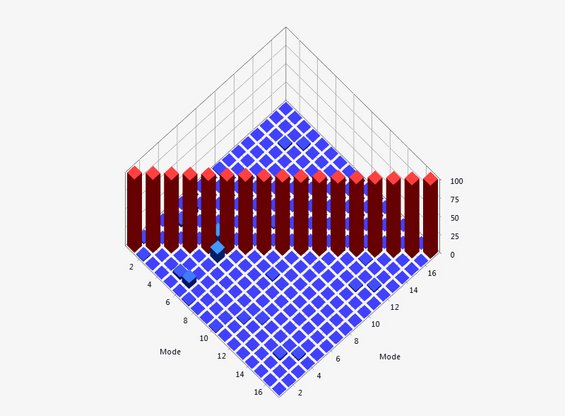
上图显示为前17阶模态提取后的AutoMac矩阵
得益于PSV系统所具有的空间分辨率及非接触式测试方法,我们能轻松地识别复模态振型(如图5所示)。将这些模态振型与有限元模型进行比对,校验有限元模型质量,拟合最佳模型参数。
Images courtesy: Images courtesy of the authors unless otherwise specified.