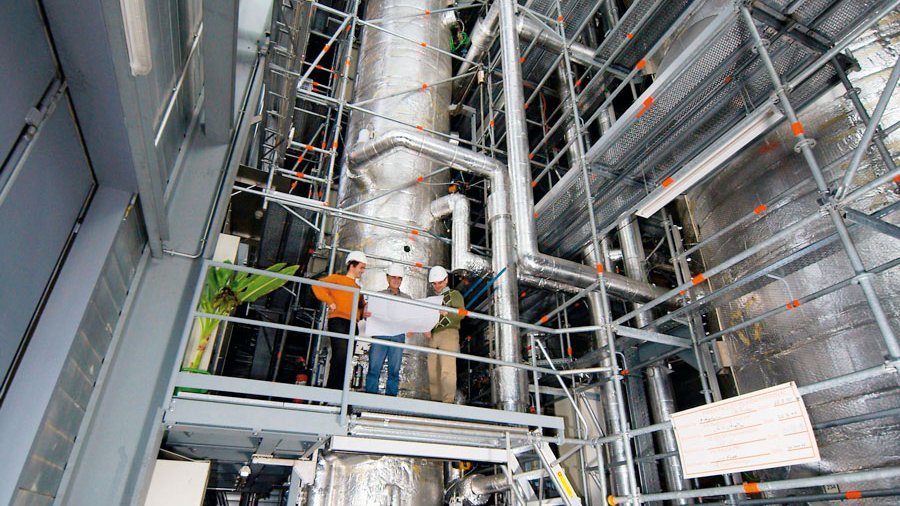
Temperaturmessungen sind in der chemischen Verfahrenstechnik unentbehrlich. Reaktionsverläufe lassen sich damit räumlich und zeitlich genau beschreiben. Herkömmliche Messverfahren kommen schnell an ihre Grenzen, wenn elektromagnetische Unempfindlichkeit oder eine hohe Messpunktdichte gefordert wird, oder wenn chemisch aggressive Umgebungsbedingungen herrschen. Die minimalinvasive faseroptische Sensorik eröffnet hier Möglichkeiten, die bisherige Verfahren weit in den Schatten stellen …
Faseroptische Sensorik
Glasfaserbasierte Sensoren werden seit vielen Jahren für die Messung von Temperatur oder Dehnung eingesetzt. Wesentliche Vorteile gegenüber ihren elektrischen Pendants ergeben sich bei Messumgebungen mit großen elektromagnetischen Feldern, schwierigen chemischen Bedingungen sowie bei Anwendungen, für die eine hohe Messpunktdichte gefordert ist, große Entfernungen überbrückt werden müssen oder kompakte Sensormaße bzw. geringes Gewicht entscheidend sind.
Konzeptionell bestehen solche faserbasierten Systeme aus einer Ausleseeinheit und der daran angeschlossenen passiven Sensorfaser. Die Ausleseeinheit sendet Licht in die Faser und analysiert reflektierte oder rückgestreute Anteile. Es wird zwischen punktförmig und verteilt messenden Systemen unterschieden. Punktförmige Sensorlösungen haben einen einzelnen Sensor am Faserende. Alternativ wird eine begrenzte Anzahl von sogenannten Faser-Bragg-Gittern an zuvor definierten Positionen entlang der Faser eingeschrieben. Jedes Gitter entspricht dabei einem Sensor.
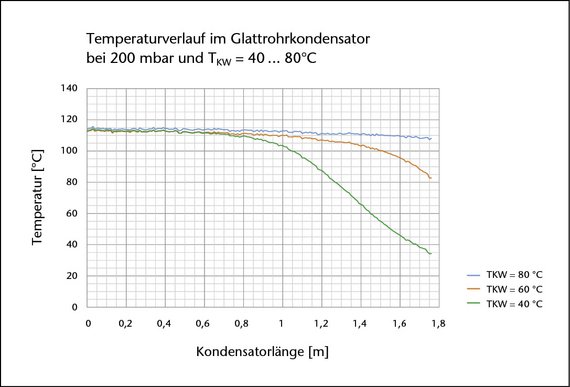
Bei verteilt messenden Systemen müssen keine Sensoren in die Faser eingebracht werden. Vielmehr wird vom Fasermaterial selbst zurückgestreutes Licht ausgewertet, um die gewünschte Information über Temperatur oder Dehnung zu erhalten. Auch hier werden zwei Arten unterschieden, die je nach Anwendungsfall zu bevorzugen sind: Systeme, die auf dem Raman- bzw. Brillouin-Effekt basieren, eignen sich für Messstrecken bis zu einigen 10 km bei einer räumlichen Auflösung entlang der Faser bis zu 10 cm.
Die zweite Gruppe sind Systeme, die auf der Auswertung der Rayleigh-Streuung basieren und mit Auflösungen im Millimeterbereich bis zu 50 m lange Messstrecken erlauben. Damit wird praktisch jeder Punkt der Glasfaser zum Sensor. Herkömmliche Verfahren benötigten dafür hunderte oder tausende konventioneller Punktsensoren mit zugehörigen Leitungen und immensem Installationsaufwand.
Einsatz in der chemischen Verfahrenstechnik
Im Bereich der chemischen Verfahrenstechnik findet die verteilte faseroptische Temperaturmessung zunehmend Verbreitung. Die Kenntnis von Temperaturprofilen entlang einer Kühl- oder Reaktionsstrecke erlaubt eine bessere Prozesskontrolle und liefert hilfreiche Ansätze zur Optimierung der Anlagengeometrie. Die hohe Messpunktdichte verteilt arbeitender Systeme erlaubt erstmals einen quantitativen Abgleich zu bestehenden FEM-Modellen und verbessert das Verständnis ablaufender Prozesse. Drei Praxisbeispiele aus der Verfahrenstechnik verdeutlichen die Anwendungsvorteile.
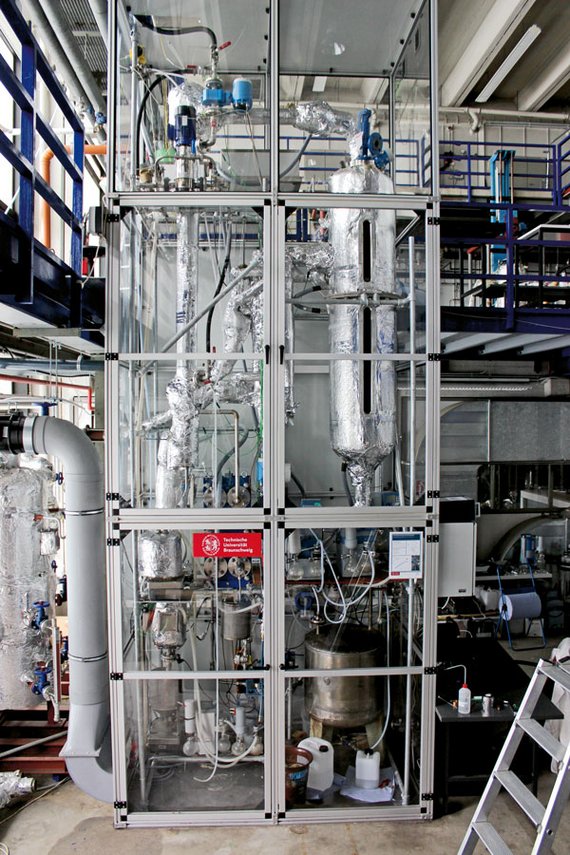
Optimierung von Kondensationsprozessen
Die TU Braunschweig hat in Zusammenarbeit mit der britischen Firma CalGavin Ltd., Alcester, Untersuchungen zum Wärmeübergang und Druckverlust an einem 2 m hohen Kondensationsreaktor (Glattrohrapparat) am Beispiel der Kondensation von Hexanol durchgeführt. Der Kondensationsverlauf in den Rohren des Reaktors wird maßgeblich durch die Auslegung der Kühlung beeinflusst. In mehrere Rohre wurde über die gesamte Kondensatorlänge eine kapillargeführte Glasfaser verlegt. Diese ist minimalinvasiv, der Einfluss auf die Strömungsbedingungen also vernachlässigbar gering. Die gemessenen Temperaturprofile und deren zeitlicher Verlauf beschreiben das Kondensationsverhalten sehr gut. Sowohl unter Variation der Reaktorgeometrie als auch bei Veränderung der Betriebsparameter Druck oder Hexanolmenge am Eintritt des Kondensators.
Die Temperaturprofile wurden mit dem verteilt messenden System ODiSI-A mit einer Ortsauflösung von 1 mm bestimmt. Die Grafik unten links verdeutlicht den Einfluss der Kühlwassertemperatur (TKW) auf den Kondensationspunkt im Reaktor. Bei allen Temperaturprofilen ist die gemessene Temperatur zu Beginn der Kondensation konstant. Ab einer Länge von ca. 0,8 m ist bei einer KühlwasserEintrittstemperatur von 40°C die Kondensation fast abgeschlossen. Anschließend wird nur noch die Gasströmung in der Mitte des Rohrs abgekühlt, was im Temperaturabfall zu erkennen ist. Bei einer Kühlwasser-Eintrittstemperatur von 60°C ist dieses Abknicken merklich später und bei 80°C gar nicht mehr zu sehen.
Das bedeutet, dass bei 80°C der Kondensator nicht mehr in der Lage ist, den eintretenden Hexanoldampf vollständig zu kondensieren. Diese Erkenntnis hilft maßgeblich bei der Optimierung der Anlagen- und Betriebsparameter und trägt letztlich zur Erhöhung des Stoffumsatzes bei.
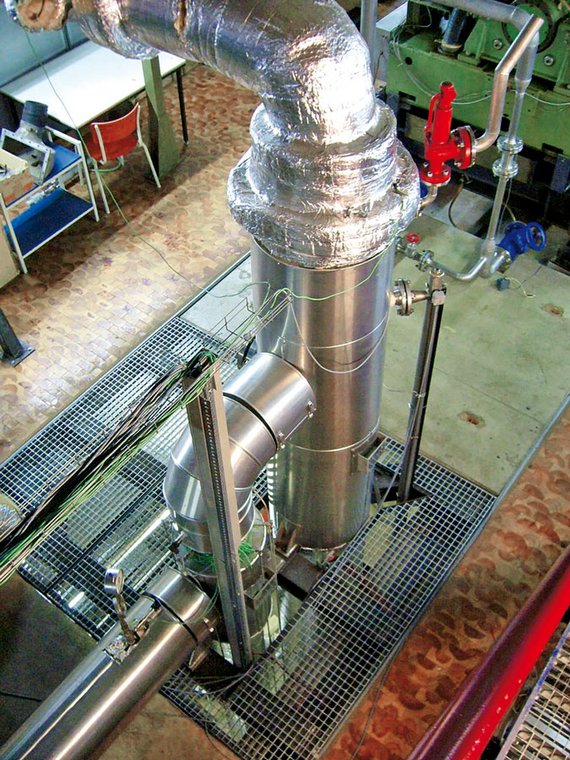
Untersuchung in einem Naturumlaufverdampfer
Die Hochschule der Bundeswehr in Hamburg setzte ein ODiSI-System für Messungen in einem Naturumlaufverdampfer ein. Verdampfer werden vielfach in der chemischen Industrie als Sumpfheizung von Destillationskolonnen und in Dampfkraftwerken eingesetzt. Sie kommen ohne Pumpen aus, da die Umlaufströmung durch anteiliges Verdampfen des Massenstroms entsteht.
Untersucht wurden lokale Wärmeübergänge und Strömungen unter Variation der Betriebsparameter mit anschließender Modellbildung. Dazu wurde u.a. die Methode der hoch ortsaufgelösten, faseroptischen Temperaturmessung verwendet. Ein besseres Verständnis der Wechselwirkungen soll den Gesamtprozess stabilisieren, den Stoffumsatz erhöhen und somit eine Kostenreduktion für den laufenden Betrieb schaffen.
Das Herzstück des Verdampfers besteht aus einem senkrecht angeordneten Rohrbündel mit definiert beheizbaren Wänden. In eines der Rohre wurde eine 4 m lange, kapillargeführte Sensorfaser bis zum Sumpf des Verdampfers verlegt. Die Edelstahl-Kapillare ist mit 0,8 mm Außendurchmesser minimal strömungsinvasiv. Sie ist zudem chemisch inert und bis weit oberhalb von 100 bar druckbeständig. Da prinzipiell auch Temperaturen von 550°C und darüber verlässlich bestimmt werden können, ist die Messanordnung auch für andere Typen von Rohrreaktoren bestens geeignet.
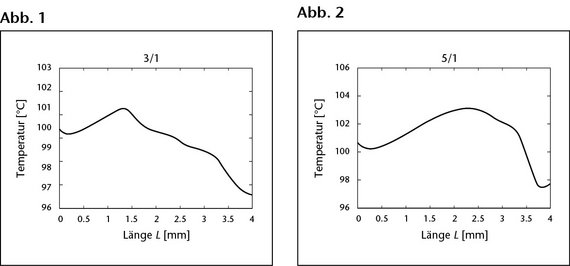
Abbildung 1 und 2 zeigen den Temperaturverlauf vom oberen Austritt des Dampfes bis zum 4 m tiefer gelegenen Eintritt des Kondensats. Bei konstantem Betriebsdruck des Prozessfluids von 1 bar wurde der Druck des Heizdampfes zwischen 2 und 5 bar variiert. Dabei wurde eine räumliche Verschiebung des Maximums im Temperaturprofil festgestellt. Die Ortsauflösung der Messung betrug 5 mm. Der Druck am Austritt von 1 bar stimmt sehr gut mit den gemessenen 100°C (Siedepunkt von Wasser) überein. In Richtung Eintritt steigt der Druck auf ca. 1,4 bar an, was einer lokalen Absenkung der Temperatur um 3 bis 4°C entspricht. Die verteilte Temperaturmessung bestätigt dies.
Kühlsystem-Untersuchungen bei Atomreaktoren
Die PANDA-Einrichtung am schweizerischen Paul-Scherrer-Institut (Titelbild) ist eine große thermohydraulische Testeinrichtung für Untersuchungen zur Sicherheit von Kernreaktor-Abschirmsystemen sowie verschiedener fortschrittlicher Leichtwasserreaktor-Designs. Die Einrichtung untersucht Kühlsysteme für passive radioaktive Zerfallswärme und das Verhalten von Sicherheitsbehältern einfacher Siedewasserreaktoren bei Störfällen. PANDA ist modular aufgebaut. Dadurch kann für wechselnde Applikationen das Verhalten von Druckkesseln, Wasserbecken oder Kondensatoren nachgestellt und systematisch untersucht werden.
Das Gesamtvolumen der Kessel beträgt ca. 460 m3, ihre Höhe erreicht 25 m. Die maximalen Arbeitsbedingungen liegen bei 10 bar und 200°C. In die Kessel können Luft, Helium und Wasser eingespritzt werden sowie Dampf, der mit max. 1,5 MW beheizt wird. Damit wird die Testumgebung auf die spezifizierten Umgebungsbedingungen gebracht. Zur ortsaufgelösten Temperaturmessung wurde eine Sensorfaser in einer Edelstahl-Kapillare waagrecht durch den unteren Teil eines Druckkessels über einem Kernsprühring verlegt.
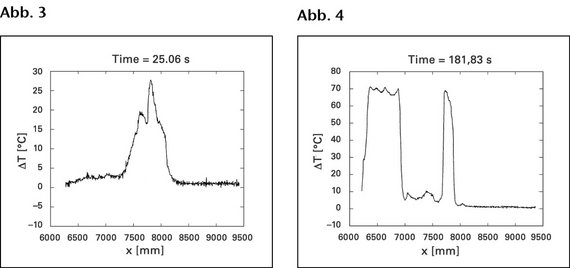
In verschiedenen Untersuchungen wurde Heißluft und Dampf zwischen 15 und 50 g/s eingeblasen. In Abb. 3 ist exemplarisch die radiale Temperaturverteilung im Kessel mit zwei Temperaturmaxima aufgetragen. Nach der Entfernung des Kernsprührings sieht die Temperaturverteilung im Kesselquerschnitt durch die veränderten Strömungen deutlich anders aus (Abb. 4).
Frühere Messungen wurden mit ca. 300 Thermoelementen durchgeführt und waren wegen der geringeren Messpunktdichte deutlich weniger aussagekräftig. Mittels der faseroptischen Messungen konnten bei deutlich geringerem Installationsaufwand sehr viel aussagekräftigere Ergebnisse in kürzerer Zeit geliefert werden.
Fazit
Faseroptische Sensorsysteme eröffnen für die Verfahrenstechnik – speziell im Bereich der Temperaturmessung – Möglichkeiten, die weit über die herkömmlicher Verfahren hinausgehen. Die Unabhängigkeit von elektromagnetischen Feldern, chemisch aggressiven Umgebungen und engen Platzverhältnissen sowie die zeitsparende Implementierung, einfache Handhabung und Dauerbelastbarkeit sind vielversprechend. Anwendungsbeispiele aus der Praxis zeigen, dass die ausgereifte Technologie auch hält, was sie verspricht.
Polytec ist seit über 50 Jahren als Experte in der optischen Messtechnik etabliert. Das Unternehmen verfügt mit seiner langjährigen Erfahrung in industriellen und Forschungsprojekten über eine herstellerunabhängige Beratungskompetenz, die alle marktfähigen Technologien einschließt.
Bildnachweise: Soweit nachfolgend nicht anders aufgeführt bei der Polytec GmbH. Titelbild: Paul-Scherrer-Institut; Bild 1 und 2: TU Braunschweig; Bild 3: Universität der Bundeswehr Hamburg; Abb. 1 u. 2: Universität der Bundeswehr Hamburg, Abb. 3 u. 4: Paul-Scherrer-Institut.