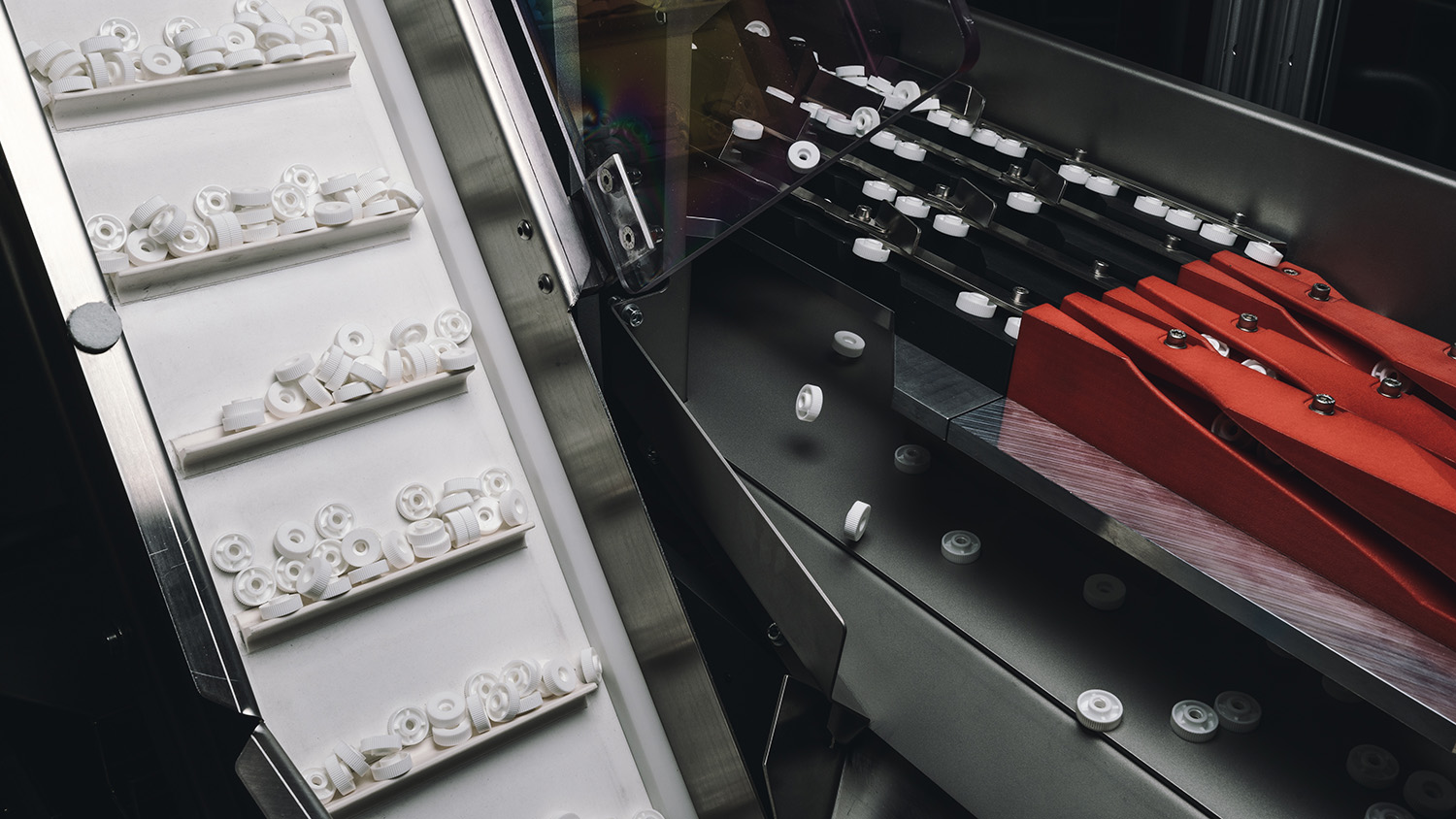
Abstract
Feeding technology is a key process in automated production. In order to develop feeding systems using simulation, the machine’s physics must be known. As a specialist in feeding technology, the RNA Group decrypts all relevant physical phenomena with the help of Polytec's measurement technology and brings them into the digital world using analytical models.
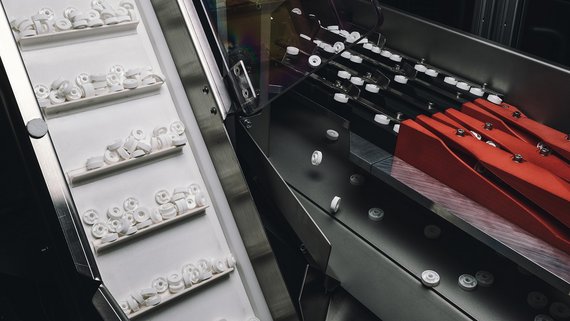
Motivation
Feeding technology has become an indispensable part of automated production. Feeding systems are tasked with sorting bulk goods (e.g. lids, screws, Lego bricks, ammunition, tablets, etc.) and feeding them to the main production system at a specific rate and output orientation.
Feeding systems are a critical interface. If the feeding breaks down due to a malfunction, the entire production plant comes to a standstill. No parts supply means production downtime. And production downtime causes unnecessary costs. It is therefore important that feeding systems have a high level of technical availability and always meet their desired performance characteristics.
Feeding systems work according to the vibration conveying principle. A drive unit oscillates at 100 Hz in a specific operating mode. That causes a conveying process, and the feeding parts start to move in a certain direction. This conveying process is the result of constantly repeating micro-impacts between the feeding parts and the feeding system. Each feeding system is unique, precisely tailored to a specific feeding part. When developing a feeding system, the art is to manipulate the vibration drive so that the resulting operating mode creates a stable conveying process. Traditionally, feeding systems are first built and then the vibration drive is changed on the shop floor by trial and error until a satisfactory solution is found. As a global technology and market leader, the RNA Group has developed a new approach: the completely digital design of the feeding system using simulation - before the system is built. However, in order to develop a simulation model, the machine’s physics must be known.
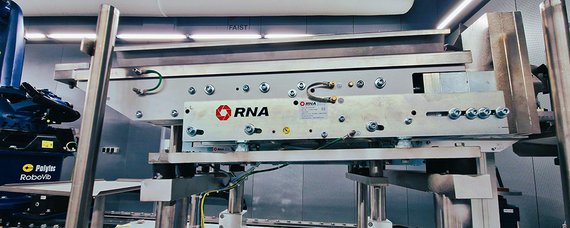
Application at Polytec
Since 2017, we have been working with Polytec to decrypt various drive architectures from the RNA portfolio and bring them into the digital world. A day of measurement at Polytec now has a well-known protocol. In advance, the measurement points are determined using a CAD model and the application engineers then teach them offline and define the coordinate system accordingly. The feed system has usually already arrived at Polytec in advance and has been set in the measuring lab.
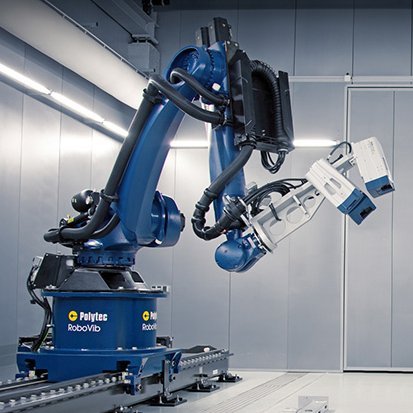
Since the operating modes exhibit three-dimensional spatial properties, a scanning 3D laser Doppler vibrometer is used for full-field vibration analysis. The vibrometer is also coupled to an industrial robot (RoboVib®) to adjust measuring positions quickly and flexibly as needed.
The measurements take place in the time domain and all measuring points are synchronized via a further 1D laser Doppler vibrometer, which acts as a trigger. In order to decipher the physical behaviour of the drive, the structural mechanics of the drive are gradually changed over a series of experiments. Spring elements are installed or removed, angles of springs are changed, and the mass properties of certain elements are manipulated. The feed system is excited using integrated electromagnets and a control unit. Excitation always takes place in the resonance range of the operation-relevant mode. The structural response measured with the 3D laser Doppler vibrometer then serves as the basis for the subsequent analysis.
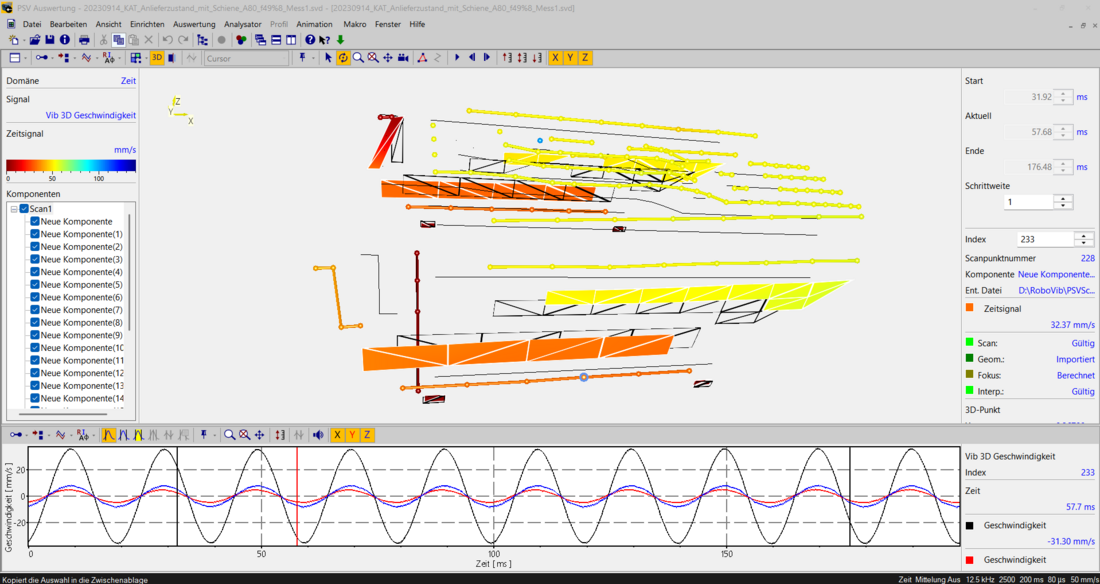
Polytec's evaluation software is used to analyse the measurements. Vibration drives for feeding technology should normally behave as classic mass-spring-damper elements, whereby the masses should have rigid body properties in the excitation range around 100 Hz. With the precise measurement by the 3D laser Doppler vibrometer, we can immediately see whether the vibrating masses on the drive behave as rigid bodies, or whether the rigid body operating mode is superimposed by disruptive deformations. In such cases, we can optimize the drives at the deformation points accordingly to ensure a permanently stable conveying process. Thanks to Polytec's measurement technology, this optimization step has already been successfully implemented several times.
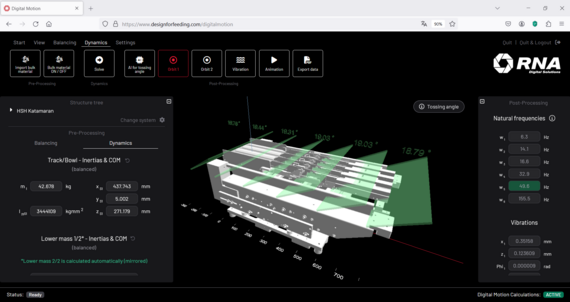
Digital Feeding Technology
The findings from the measurements are ultimately used to create a simulation model for each vibration drive. This is an analytical model in which, for example, the degrees of freedom and kinematic constraints are derived from the measurements. The creation of the model and the parameterization represent an one-time effort. As soon as a drive unit has been fully physically decrypted and modelled, it is stored in the RNA simulation software Digital Motion and can be used for all future projects. Digital Motion is cloud-native and available to both RNA and all external customers via www.designforfeeding.com.
With the help of Digital Motion, the structural mechanics of the drives for new feeding system developments can be optimized within a few seconds. The know-how of drive optimization is stored in the software and accelerates the development of feeding systems enormously. Digitally optimized feeding systems ultimately lead to stable conveying processes with high technical reliability.
Summary
Polytec's measurement technology is a key element in deciphering the complex machine physics of feeding systems. Thanks to this technology, we can fully understand and simulate vibration drives. Both the RNA Group and all of our customers benefit from the know-how – by faster system development and better performance over the entire operating life cycle.