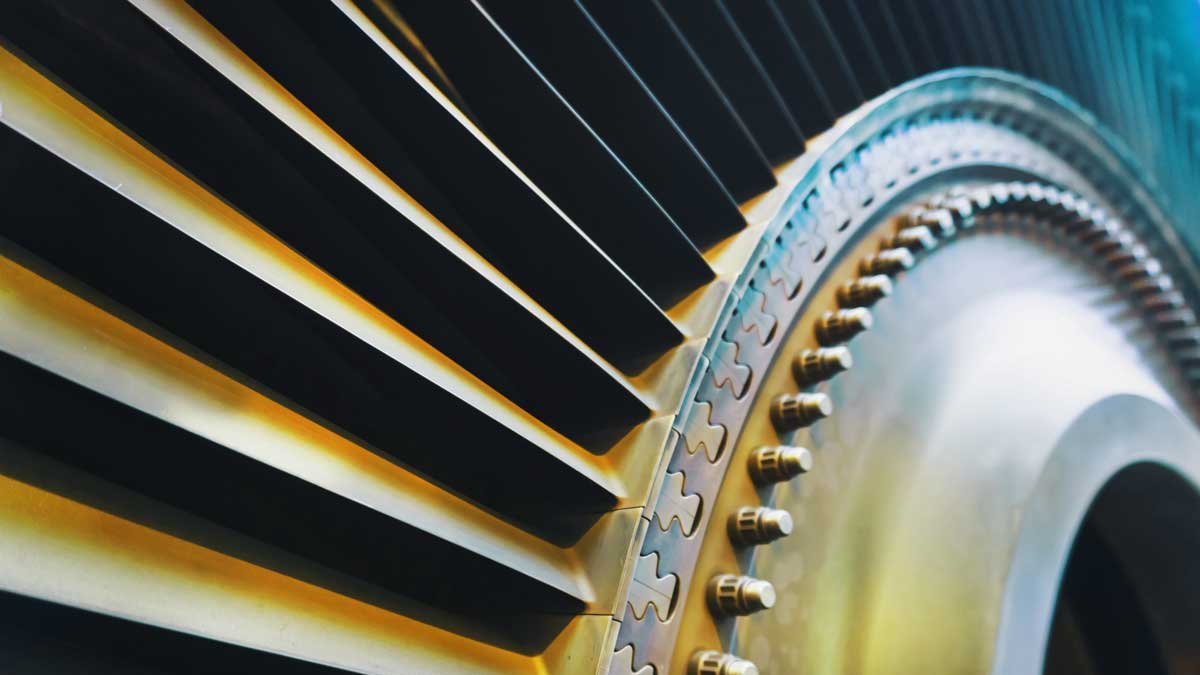
In the realm of vibration testing, a significant obstacle arises in the form of mass loading. The behavior of a dynamic vibration sample, or device under test (DUT), is profoundly influenced by the additional mass applied to it. This phenomenon is particularly pronounced in vibrating cantilevered beams, and it becomes even more intricate when dealing with curved cantilevered beams like turbine blades. Accurate measurement of resonant frequencies in turbine blades using accelerometers is a complex endeavor, primarily due to mass loading. Remarkably, even the minutest accelerometers introduce a mass that disrupts the natural frequency of a turbine blade, making precise measurements a challenging feat.
One approach for avoiding the influence of mass-loading is to measure the turbine blade’s acceleration in a non-contact way using a laser-optical sensor, such as a laser Doppler vibrometer. In the below case study, a lightweight accelerometer (7.5 g) measures the resonant frequencies of a short turbine blade (20.4 g). The test data was again evaluated in the non-contact way using a Polytec vibration sensor VibroGo® (laser vibrometer). Vibration Research’s ObserVR1000 dynamic signal analyzer recorded the data.
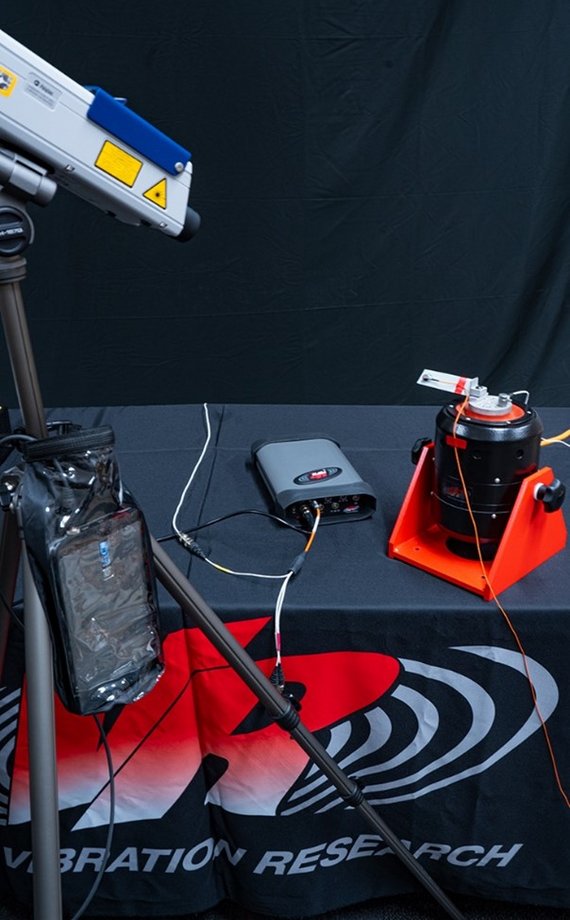
Procedure
The laser vibrometer for this test operated in the velocity setting however it is capable of measuring direct displacement as well. Velocity is the preferred option because it offers a more consistent frequency response, thanks to the scaling factor that relates acceleration, velocity, and displacement. While acceleration increases with frequency and displacement decreases, velocity maintains a relatively stable response. The velocity setting was chosen to avoid any potential lag or inaccuracies in data processing.
For the test, a bandwidth of 1 kHz was considered. A velocity range of 1 m/s (peak) was considered optimal so as to not cause decoder saturation and hence overrange.
Finally, to optimize measurements, the laser vibrometer was positioned at an ideal stand-off distance. The vibrometer used had a basic stand-off distance formula of 463 mm + (183 mm * n). The vibrometer was placed at a distance of 877 mm from the turbine blade's tip, as shown in Figure 1. Note that it is not mandatory to place the vibrometer at an optimal stand-off distance, however if time/space permits, it is the preferred protocol.
Laser vibrometer settings
Bandwidth: 1 kHz
High pass filter: 13 Hz
Velocity range: 1 m/s
Sensitivity: 250 mm/s/V
Optimal stand-off distance: 877 mm
A flat 1g sine sweep from 50 Hz to 500 Hz was conducted on the turbine blade at a 1 Octave/min sweep rate. The test was conducted with and without mass loading; the „mass“ in this case being the attached accelerometer.
In the first test, an accelerometer was attached to the end of the turbine blade (mass loading situation) to measure the resonances of the turbine blade. Simultaneously, the vibrometer was collecting data at the same location as the accelerometer (Figure 2).
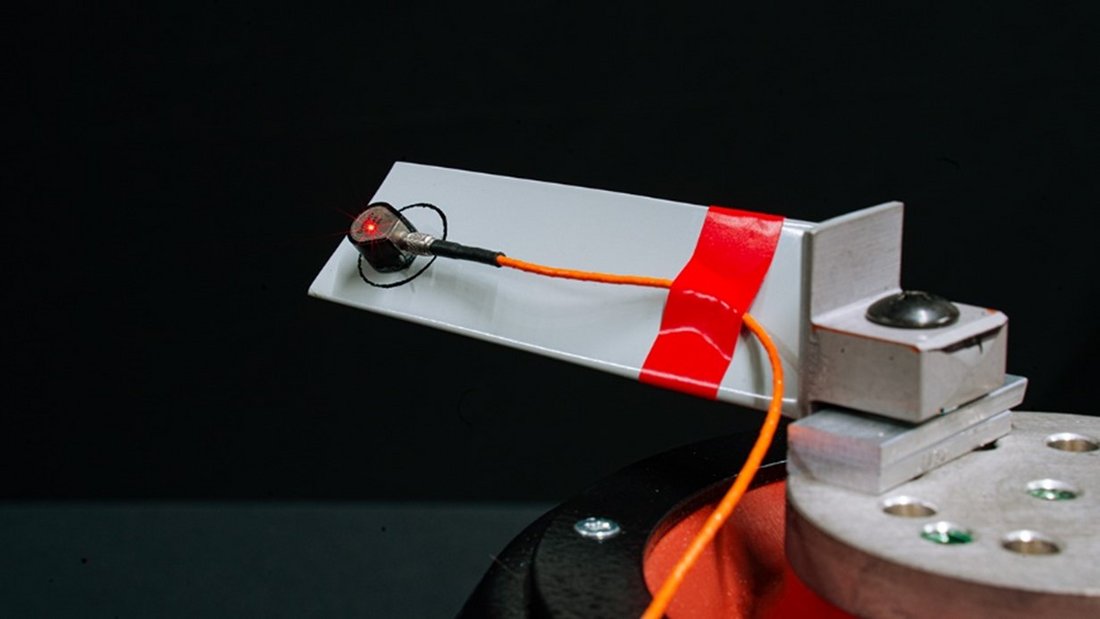
In the second test, the accelerometer was removed (no mass loading) and the vibrometer collected the vibration data from the end of the turbine blade (Figure 3).
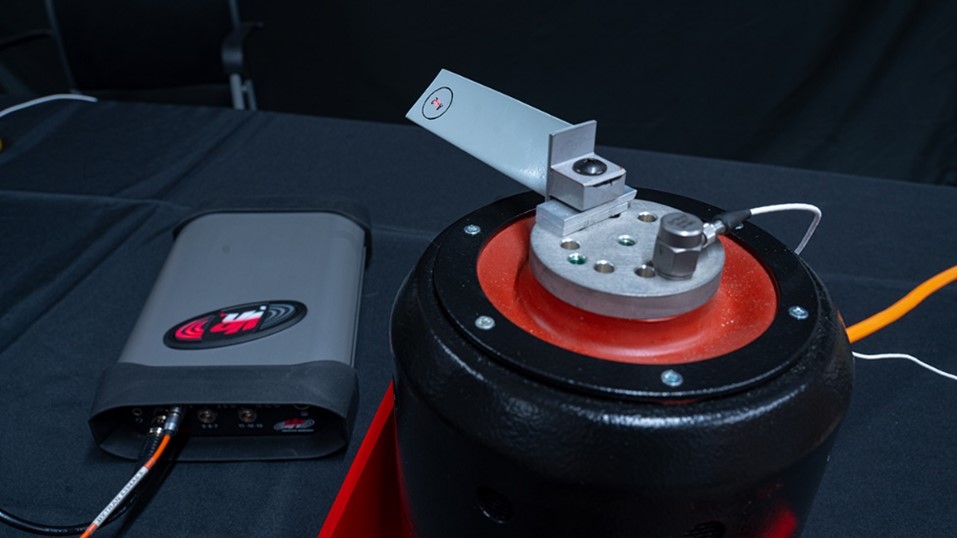
The results of these tests were compared to confirm that the laser vibrometer could collect the same data as the accelerometer and confirm the effect of mass loading on a resonant beam.
Results
A flat 1g sine sweep test was conducted on the turbine blade, sweeping down from 500 Hz to 30 Hz at a 1-oct/min sweep rate. Several resonances were detected during this sine test. Both the accelerometer and the vibrometer were able to detect the same resonances (Figure 4).
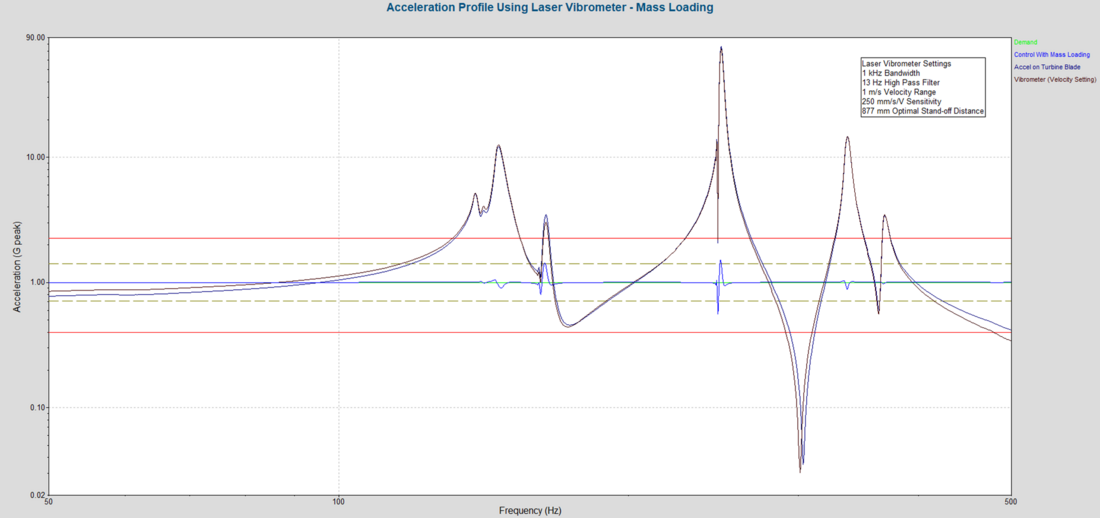
The results of the testing demonstrate that mass loading causes a downward shift in the resonances of the turbine blade (Figure 5). This corroborates well with the fundamental single-DOF model (SDOF, single degree of freedom) that shows an inverse relationship between natural frequency and mass.
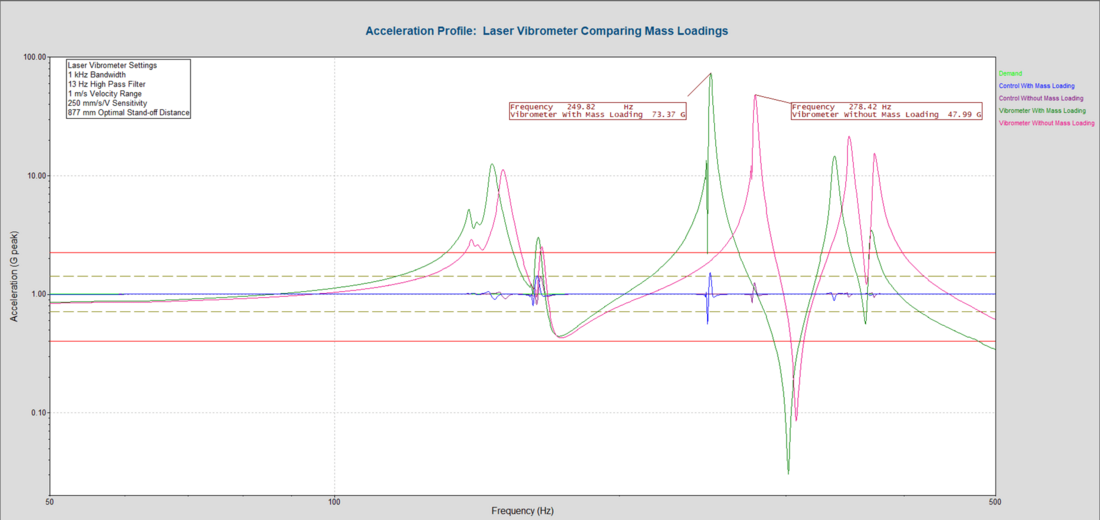
The results also show that the controller was able to control better within tolerances when there was no mass on the turbine blade (Figure 6). Mass loading makes controlling through resonances more difficult.
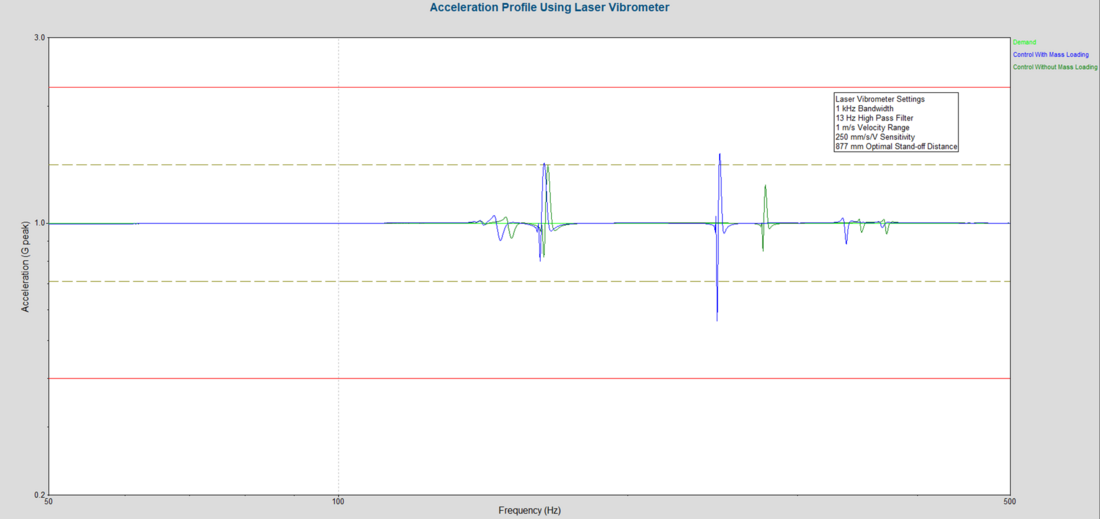
Conclusion
The underlying case study reveals three insights. First, the results show that a laser vibrometer can provide the same measurements as a traditional accelerometer. Second, the results show that the mass loading effect indeed is an issue that engineers need to address actively. The resonant frequencies of the turbine blade changed when the accelerometer was removed. Finally, the results show that a non-contact measurement technique such as laser Doppler vibrometry can accurately determine the resonant frequencies of a sample that is particularly susceptible to mass loading issues. By using the non-contact sensor for precise determination of the sample's resonant frequencies, the controller will also be able to better control through the resonances than when the turbine blade is affected by mass loading problems.
This article is an adaptation of the application note by www.VibrationResearch.com: Mass loading and benefits of a laser vibrometer.
Images courtesy: Images courtesy of the authors unless otherwise specified. Cover image: Aleksandr Grechanyuk/shutterstock.com