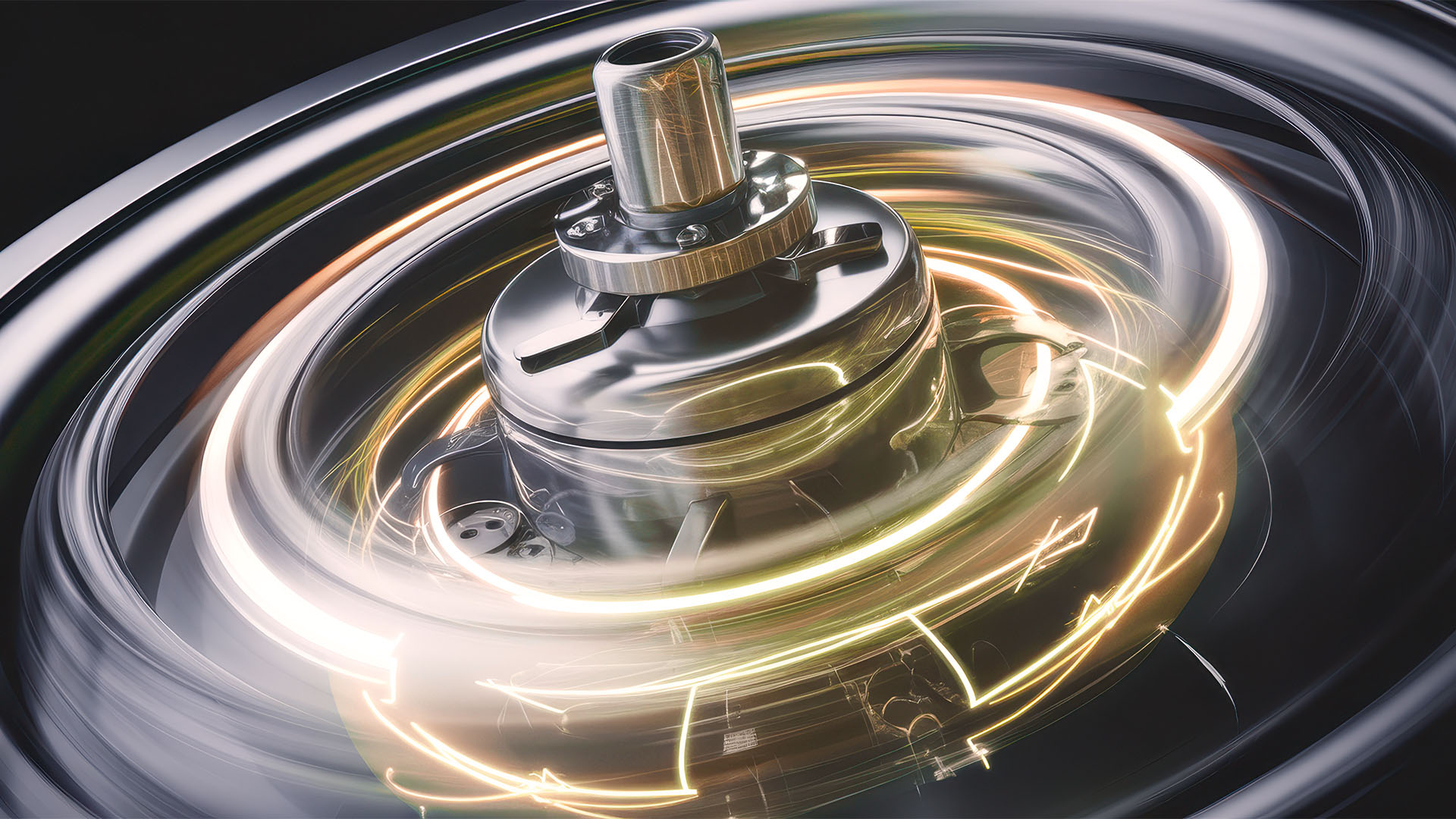
Warum die Akustik elektrischer Antriebe entscheidend ist
Elektrische Maschinen werden zunehmend als primäre Antriebstechnologie in Fahrzeugen eingesetzt. Das akustische Verhalten des Antriebs ist ein wesentlicher Faktor für das Qualitätsempfinden von Elektrofahrzeugen. In der Entwicklung von elektrischen Antrieben werden deshalb früh numerische Verfahren zur Bewertung und Optimierung des akustischen Verhaltens eingesetzt. Das strukturdynamische Übertragungsverhalten des Antriebs spielt bei der Bewertung der Amplituden eine wichtige Rolle. Da die Prognosefähigkeit von heutigen Dämpfungsmodellen insbesondere für elektrische Antriebe begrenzt ist, werden effiziente Messverfahren zur Modellvalidierung benötigt.
In elektrischen Antrieben treten im gesamten hörbaren Frequenzbereich akustische Anregungen auf. Zum Beispiel entstehen aufgrund der Ansteuerung der Maschine mit moderner Leistungselektronik Kräfte und Geräusche im höheren kHz-Bereich, die oft als besonders störend empfunden werden. Für die experimentelle Untersuchung von elektrischen Antrieben ergeben sich daraus besondere Herausforderungen.
Zur eindeutigen Rekonstruktion der teils sehr komplexen Schwingungsformen im höheren Frequenzbereich werden sehr viele Messpunkte benötigt. Außerdem ist das Verhalten von elektrischen Maschinen aufgrund des mechanischen Aufbaus teilweise nichtlinear.
Mit den modernsten robotergestützten 3D-Laser-Doppler-Vibrometern von Polytec ist es möglich, eine Antwort auf diese besonderen Herausforderungen bei der akustischen Analyse von elektrischen Antrieben zu geben. Das optische Messverfahren minimiert die Einflüsse des Versuchsaufbaus auf die Messergebnisse und erfasst gleichzeitig eine nahezu unbegrenzte Anzahl von Messpunkten. Laser-Doppler-Vibrometer mit der QTec-Technologie ermöglichen einen deutlich vergrößerten Signal-Rausch-Abstand. Dadurch kann die Messzeit reduziert, der auswertbare Frequenzbereich gesteigert und eine zuverlässige Dämpfungsschätzung durchgeführt werden.
Die zuvor beschriebenen Eigenschaften werden im Folgenden am Beispiel der experimentellen Modalanalyse eines elektrischen Antriebes untersucht.
Präzision in Perfektion: Wie Schwingungen sichtbar gemacht werden
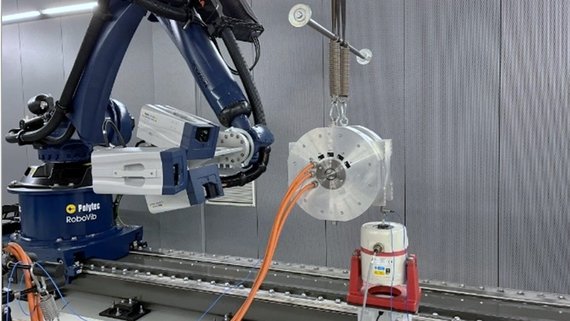
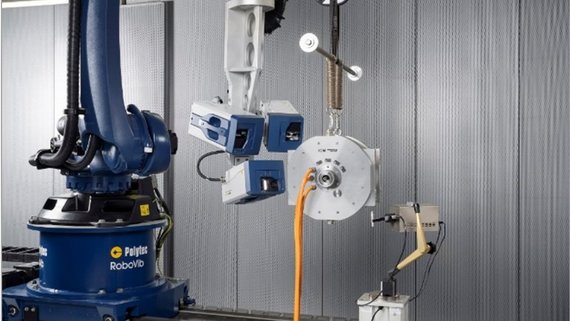
Die experimentelle Modalanalyse wird im vollautomatischen RoboVib-Testzentrum durchgeführt. Ziel der experimentellen Modalanalyse ist es, das strukturdynamische Übertragungsverhalten auf Basis der Eigenfrequenzen, Eigenvektoren und der Dämpfung zu beschreiben und mit dem numerischen Modell abzugleichen.
In Abbildung 1 und Abbildung 2 sind zwei ausgewählte Versuchsaufbauten der Messkampagne dargestellt. Der elektrische Antrieb wird zur Reduktion der äußeren Einflüsse elastisch mit Federn aufgehängt. Die Federsteifigkeit der Aufhängung wird dabei so gewählt, dass die Eigenfrequenz der Aufhängung ausreichend weit von der ersten erwarteten Eigenfrequenz der Maschine entfernt ist, um den Einfluss der Aufhängung auf das Dämpfungsverhalten der Maschine zu minimieren.
Zur definierten Anregung der Maschine bei der Modalanalyse stehen unterschiedliche Methoden und Anregungssignale zur Verfügung. Untersucht werden zum einen die Anregung mit einem Shaker der Firma LDS durch Pseudo-Rauschen sowie weißem Rauschen und zum anderen die Anregung mittels automatischem Modalhammer der Firma NV-Tech. Um plastische Verformungen bei der Nutzung des automatischen Modalhammers zu vermeiden, werden dünne gehärtete Stahlplättchen an den Anregungspunkten befestigt. Die Stellen zur optimalen Anregung der Struktur werden mit speziell entwickelten Verfahren vorab unter Berücksichtigung der Versuchsrandbedingungen im numerischen Modell bestimmt.
Zur Messung der Schwingungsantwort kommen zwei verschiedene Laser-Doppler-Vibrometer (PSV Xtra und PSV QTec) im RoboVib-Testzentrum zum Einsatz.
Aufgrund der gekrümmten Oberfläche der elektrischen Maschine muss zur optischen Vermessung mit verschiedenen Positionen der Vibrometer gearbeitet werden. Das RoboVib-Messsystem realisiert diese Messungen wiederholgenau und vollständig automatisiert mit insgesamt 17 Positionen (vgl. Video).
Wie die QTec-Technologie die Signalqualität revolutioniert
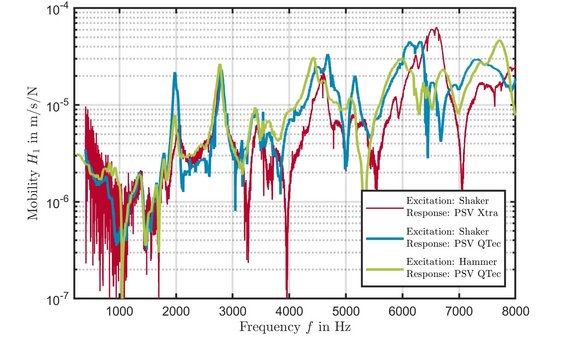
Abbildung 4 zeigt exemplarisch die Ergebnisse einer Übertragungsfunktion, um die Versuchsaufbauten zu vergleichen: die Anregung mittels Shaker oder automatischem Modalhammer sowie die Messung der Schwingungsantwort mit dem PSV Xtra oder dem PSV QTec.
Für den Aufbau mit Shaker und PSV Xtra zeigt sich ein starker Rauschanteil in der Übertragungsfunktion im gesamten Frequenzbereich. Im Gegensatz dazu kann bei Verwendung des QTec-Systems der Rauschanteil deutlich reduziert werden. Der Einsatz eines automatischen Modalhammers anstelle des Shakers führt zu einer weiteren Verbesserung der Qualität der Messdaten.
In Abbildung 5 und 6 sind die Zeitsignale der gemessenen Oberflächengeschwindigkeit mit und ohne QTec-Technologie für einen ausgewählten Messpunkt bei Anregung mit dem automatischen Modalhammer dargestellt. Aufgrund des Versuchsaufbaus und der notwendigen elastischen Lagerungen führen die Querbewegungen der Maschine zu Signal-Aussetzern (Drop-outs), wenn kein QTec zum Einsatz kommt.
Durch die Mehrkanal-Detektion von QTec können diese Signal-Aussetzer vollständig vermieden und dadurch die Signalqualität für diese Anwendung erheblich verbessert werden.
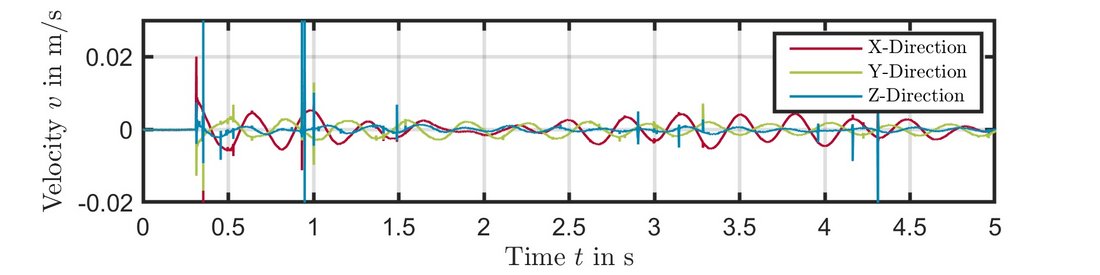
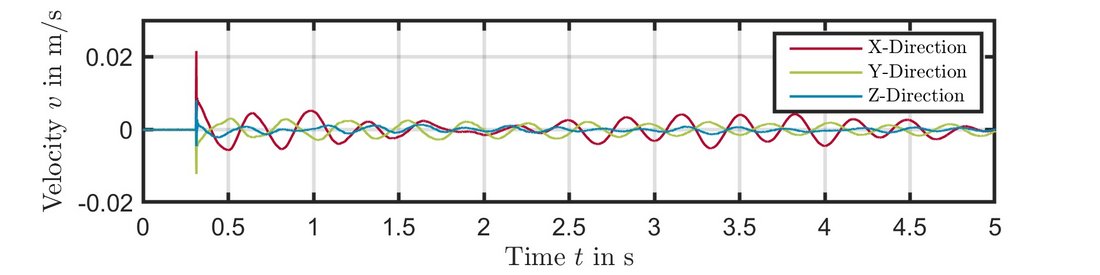
Insgesamt ist es mit dem Versuchsaufbau mit automatischem Modalhammer und QTec-Vibrometer möglich, eine experimentelle Modalanalyse der elektrischen Maschine bis 12 kHz durchzuführen. Die folgenden Abbildungen zeigen exemplarische Schwingungsformen bei ausgewählten Resonanzfrequenzen 2,8 und 4,6 kHz sowie 6,2 und 9,8 kHz.
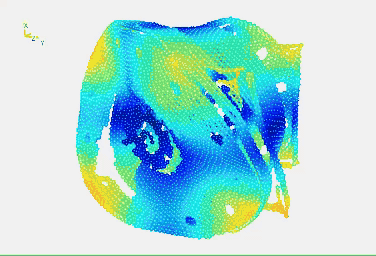
Abbildung 7a: Schwingform bei 2,8 kHz
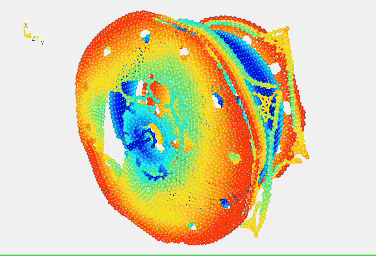
Abbildung 7b: Schwingform bei 4,6 kHz
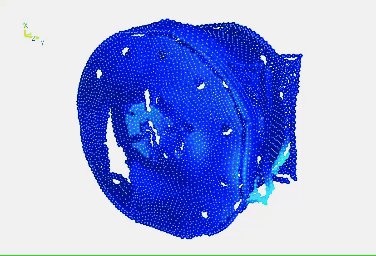
Abbildung 8a: Schwingform bei 6,2 kHz
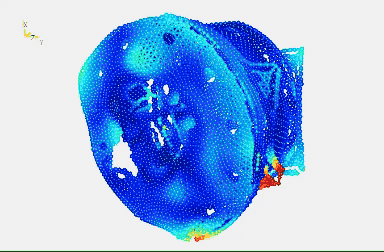
Abbildung 8b: Schwingform bei 9,8 kHz
Grenzen der Simulation: Was wir aus Messungen lernen
Eine Korrelation zwischen Messung und Simulation zeigt für eine Frequenz beispielsweise, dass auf der Vorderseite der Maschine (Abbildung 9a) eine große Übereinstimmung zwischen Modell und Messung vorliegt. Auf der Rückseite der Maschine (Abbildung 9b) stimmen die Schwingungsmoden lokal nicht überein. Das lässt darauf schließen, dass mit aktuellen Modellierungsmethoden insbesondere der Einfluss der Verkabelung der elektrischen Maschine nicht ausreichend in diesem Frequenzbereich berücksichtigt werden kann.
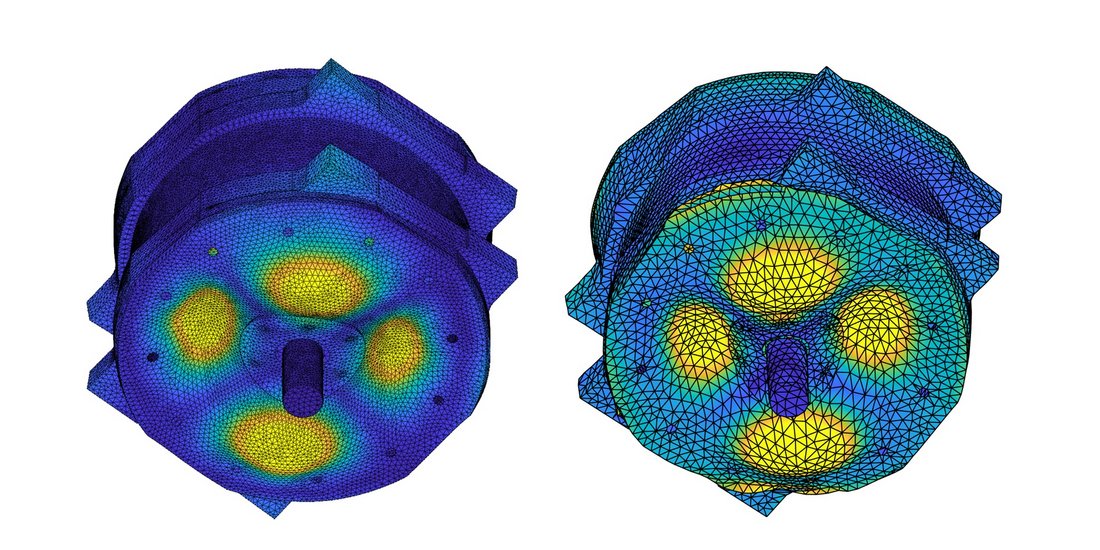
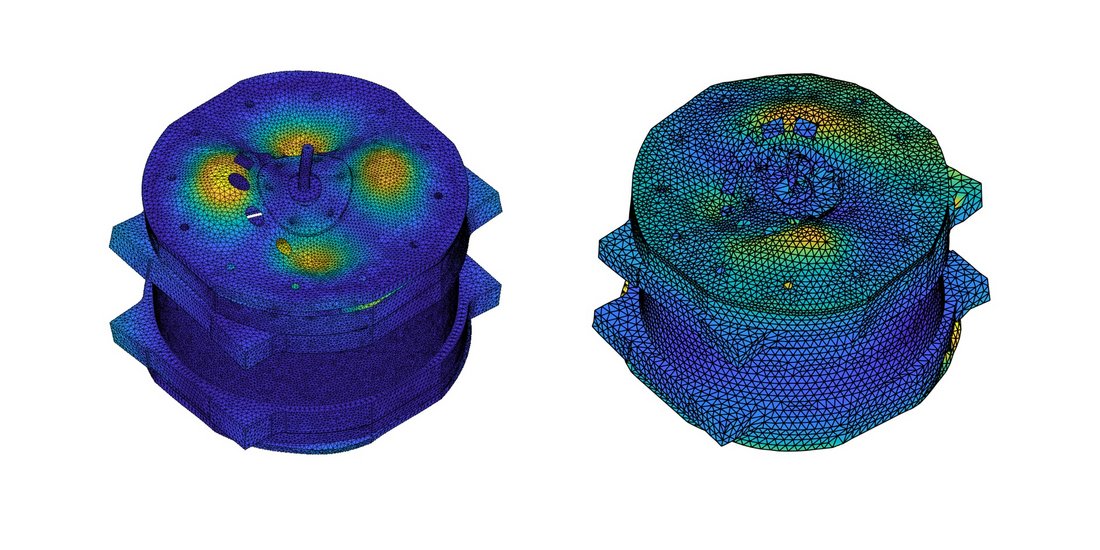
Zusammengefasst: Neue Maßstäbe für die akustische Analyse
Mit den neuesten robotergestützten 3D-Laser-Doppler-Vibrometern von Polytec ist es möglich, eine Antwort auf die besonderen Herausforderungen bei der akustischen Analyse von elektrischen Antrieben zu geben. Es kann durch die vollständige Automatisierung der Messung eine für den höheren kHz-Bereich ausreichende Messpunktanzahl realisiert werden. Durch das optische Messverfahren lassen sich die Einflüsse des Versuchsaufbaus auf die Messergebnisse minimieren. Mit Laser-Doppler-Vibrometern mit der QTec-Technologie kann der Signal-Rausch-Abstand deutlich vergrößert werden. Dadurch wird die Messzeit reduziert, der auswertbare Frequenzbereich gesteigert und eine zuverlässige Dämpfungsschätzung durchgeführt.
Eine Korrelation mit numerischen Modellen zeigt weiter, dass mit aktuellen Berechnungsverfahren das Schwingungsverhalten von elektrischen Maschinen nicht im gesamten Frequenzbereich mit hoher Genauigkeit beschrieben werden kann. Das bedeutet, dass die aktuellen Berechnungsverfahren eine Messung nicht vollständig ersetzen können.
Bildnachweise: Soweit nachfolgend nicht anders aufgeführt bei den Autoren. Titelbild: Tom / stock.adobe.com